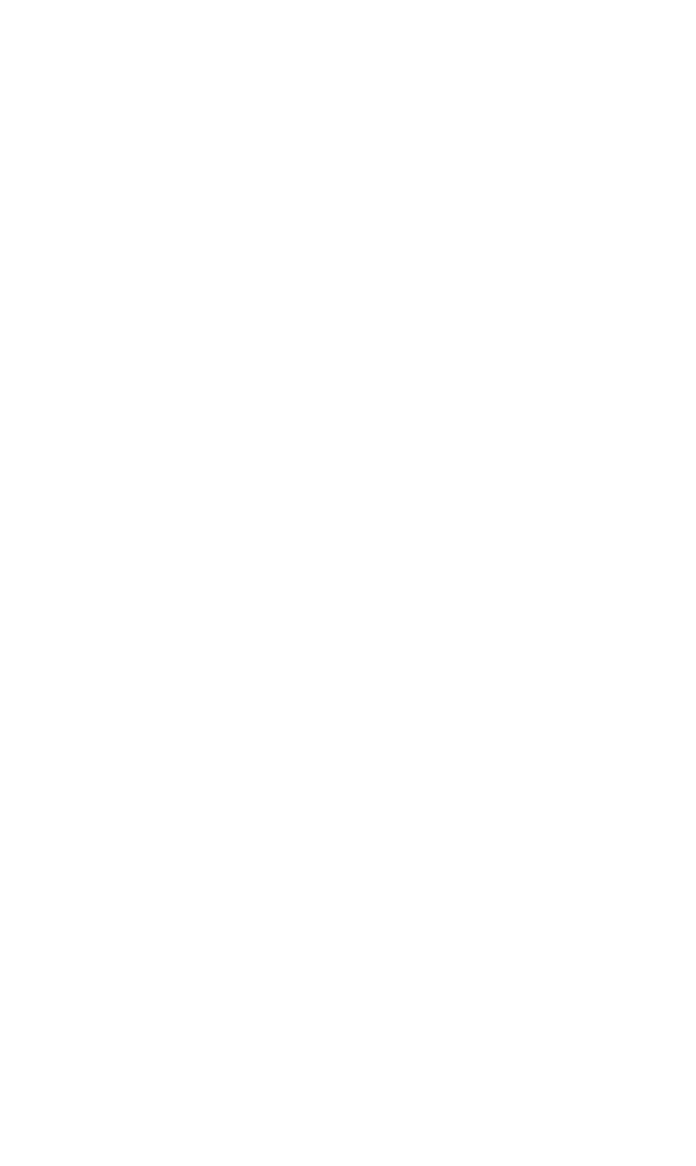
1456 INDEX
Environment(s) (continued )
compatibility of medical products with,
1198
of composite manufacturing, 1367–1368
copper and copper alloys in, 199–200
endurance of electronic packaging in, 1241
failure of plastics in, 778
for magnesium and magnesium alloy use,
267
for metallic materials testing, 540–542
space, advanced composites in, 1141–1142
for superalloys, 316
wear phenomena in, 1276
Environmentally enhanced fractures (brittle
materials), 813–815
EOC, see Equation of continuity
Epitaxy, 1335–1336
Epoxy resins, 352–353, 1240
Equation of continuity (EOC), 998–999
Erosion corrosion, 709, 767
ES, see Electro-stream
ESR, see Electro slag remelting
Ethane, 1424
Ethical considerations (in sport equipment
materials selection), 1270–1272
Europe, all-composite bridges in, 1413–1416
Eutectic reaction, 36
Evaluated data, 460
Evaluation, nondestructive, see Nondestructive
inspection/ evaluation
Evaporation (deposition technique), 1330,
1334–1335
Expandable-bead molding (plastics), 957
Expert systems, 23–24
Extensible markup language (XML), 501
Extensional flow, 994
Extensional-flow-dominated processes (plastic
parts), 995, 1019–1022, 1026–1032
blow molding, 1026–1027
compression molding, 1026
fiber spinning, 1019–1020
film blowing, 1020–1022
rotational molding, 1032
thermoforming, 1027–1032
Extrusion:
of metals, 932–933, 940–941
of plastics, 958, 969–972, 1001–1016
single screw, 1011–1015
twin screw, 1015–1016
Extrusion blow molding (EBM), 977–978
Extrusion covering (plastics), 972–973
Eyecatcher Project, 1408–1410
Eyring model, generalized, 1000–1001
Fabrication. See also specific processes
of carbon vs. stainless steels, 85
of magnesium and magnesium alloys, 262–
264
of microelectromechanical systems, 1326
of nickel and nickel alloys, 252–255
of optical fibers, 1320–1322
selecting process of, 836–838
Fabrics:
co-woven, 1104–1105
noncrimp, 1041, 1042
woven, 1041, 1042
Face-centered-cubic (fcc) arrangement, 30, 31,
47, 294
Failure. See also Failure analysis
of ceramics, 787–790
delayed, 792–794
design as factor in, 788, 798–803
and intrinsic vs. extrinsic flaws, 789–790
materials selection as factor in, 787–788,
803–805
modes of failure, 788
probability of, 789
process as factor in, 788–790
service conditions as factor in, 803–807
under thermal shock conditions, 803–
804
delayed, 792–794
of metals, 705–712
brinnelling failure, 708
brittle fracture failure, 708
buckling failure, 707, 712
combined creep and fatigue failure, 708,
712
corrosion failure, 707, 709
corrosion fatigue failure, 708, 712
corrosion wear failure, 708, 712
creep buckling failure, 707, 712
creep failure, 707, 711
criteria of failure, 705–706
ductile rupture failure, 708
elastic deformation failure, 708
fatigue failure, 706–709
fretting failure, 707, 710–711
fretting fatigue failure, 710–711
galling and seizure failure, 707, 711
impact failure, 707, 710
modes of failure, 706–712
radiation damage, 707, 712
spalling failure, 707, 711–712
stress corrosion failure, 708, 712
stress rupture failure, 707, 711
theories of, 714–716
thermal relaxation failure, 707, 711
thermal shock failure, 707, 711
wear failure, 707, 709–710
yielding failure, 708
modes of, 706–712