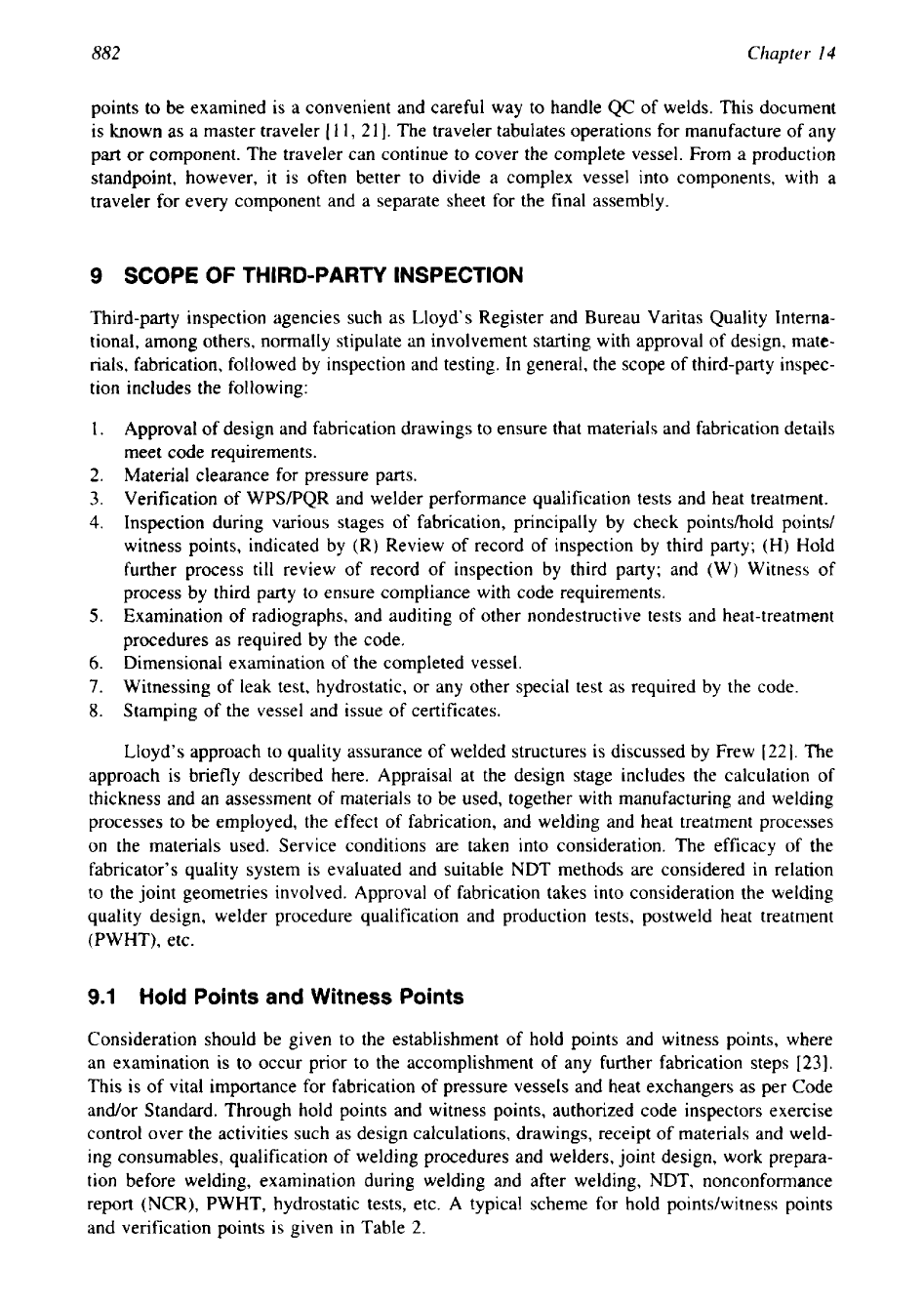
882
Chapter
14
points to be examined is a convenient and careful way to handle QC of welds. This document
is known as a master traveler
[
1
1,
2
11.
The traveler tabulates operations for manufacture of any
part or component. The traveler can continue to cover the complete vessel. From a production
standpoint, however,
it
is often better to divide a complex vessel into components, with a
traveler for every component and a separate sheet for the final assembly.
9
SCOPE
OF THIRD-PARTY INSPECTION
Third-party inspection agencies such as Lloyd’
s
Register and Bureau Varitas Quality Interna-
tional, among others, normally stipulate an involvement starting with approval of design, mate-
rials, fabrication, followed by inspection and testing. In general, the scope of third-party inspec-
tion includes the following:
1.
Approval of design and fabrication drawings to ensure that materials and fabrication details
meet code requirements.
2.
Material clearance for pressure parts.
3.
Verification of WPSPQR and welder performance qualification tests and heat treatment.
4.
Inspection during various stages
of
fabrication, principally by check pointshold points/
witness points, indicated by (R) Review of record of inspection by third party; (H) Hold
further process till review of record of inspection by third party; and (W) Witness of
process by third party to ensure compliance with code requirements.
5.
Examination of radiographs, and auditing of other nondestructive tests and heat-treatment
procedures as required by the code.
6.
Dimensional examination
of
the completed vessel.
7.
Witnessing of leak test, hydrostatic, or any other special test as required by the code.
8.
Stamping of the vessel and issue of certificates.
Lloyd’s approach to quality assurance of welded structures is discussed by Frew
[22].
The
approach is briefly described here. Appraisal at the design stage includes the calculation of
thickness and an assessment of materials to be used, together with manufacturing and welding
processes to be employed, the effect of fabrication, and welding and heat treatment processes
on the materials used. Service conditions are taken into consideration. The efficacy of the
fabricator’s quality system is evaluated and suitable NDT methods are considered
in
relation
to the joint geometries involved. Approval of fabrication takes into consideration the welding
quality design, welder procedure qualification and production tests, postweld heat treatment
(PWHT), etc.
9.1
Hold
Points and Witness Points
Consideration should be given to the establishment of hold points and witness points, where
an examination is to occur prior to the accomplishment of any further fabrication steps
[23].
This is of vital importance for fabrication of pressure vessels and heat exchangers as per Code
andor Standard. Through hold points and witness points, authorized code inspectors exercise
control over the activities such as design calculations, drawings, receipt of materials and weld-
ing consumables, qualification of welding procedures and welders, joint design, work prepara-
tion before welding, examination during welding and after welding, NDT, nonconformance
report (NCR),
PWHT,
hydrostatic tests, etc.
A
typical scheme for hold points/witness points
and verification points is given in Table
2.