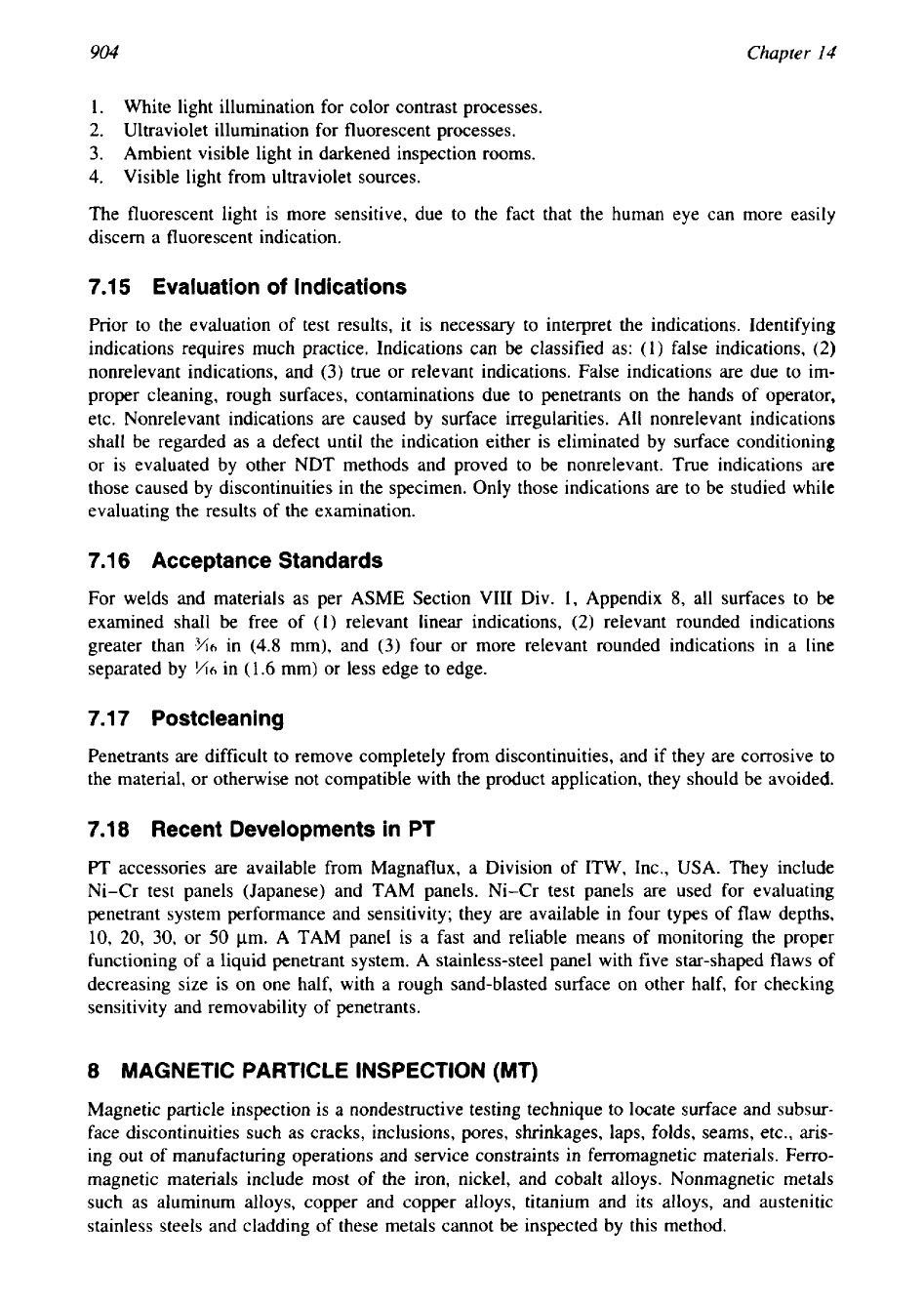
904
Chapter
I4
1. White light illumination for color contrast processes.
2.
Ultraviolet illumination for fluorescent processes.
3.
Ambient visible light in darkened inspection rooms.
4.
Visible light from ultraviolet sources.
The fluorescent light is more sensitive, due to the fact that the human eye can more easily
discern a fluorescent indication.
7.1
5
Evaluation
of
Indications
Prior to the evaluation of test results, it is necessary to interpret the indications. Identifying
indications requires much practice. Indications can be classified as:
(1)
false indications,
(2)
nonrelevant indications, and
(3)
true or relevant indications. False indications are due to im-
proper cleaning, rough surfaces, contaminations due to penetrants on the hands of operator,
etc. Nonrelevant indications are caused by surface irregularities. All nonrelevant indications
shall be regarded as a defect until the indication either is eliminated by surface conditioning
or
is evaluated by other NDT methods and proved to be nonrelevant. True indications are
those caused by discontinuities in the specimen. Only those indications are to be studied while
evaluating the results of the examination.
7.1
6
Acceptance Standards
For welds and materials as per ASME Section VIII Div.
1,
Appendix
8,
all surfaces to be
examined shall be free of (1) relevant linear indications,
(2)
relevant rounded indications
greater than
%6
in
(4.8
mm), and
(3)
four or more relevant rounded indications in a line
separated by
I/ih
in (1.6 mm)
or
less edge to edge.
7.17 Postcleaning
Penetrants are difficult to remove completely from discontinuities, and if they are corrosive
to
the material, or otherwise not compatible with the product application, they should be avoided.
7.18 Recent Developments in PT
PT
accessories are available from Magnaflux, a Division of ITW, Inc., USA. They include
Ni-Cr test panels (Japanese) and TAM panels. Ni-Cr test panels are used for evaluating
penetrant system performance and sensitivity; they are available in four types of flaw depths,
10,
20,
30,
or
50
pm. A TAM panel
is
a fast and reliable means of monitoring the proper
functioning of a liquid penetrant system. A stainless-steel panel with five star-shaped flaws of
decreasing size is on one half, with a rough sand-blasted surface on other half, for checking
sensitivity and removability
of
penetrants.
8
MAGNETIC PARTICLE INSPECTION (MT)
Magnetic particle inspection is a nondestructive testing technique to locate surface and subsur-
face discontinuities such as cracks, inclusions, pores, shrinkages, laps, folds, seams, etc., aris-
ing out of manufacturing operations and service constraints in ferromagnetic materials. Ferro-
magnetic materials include most of the iron, nickel, and cobalt alloys. Nonmagnetic metals
such as aluminum alloys, copper and copper alloys, titanium and its alloys, and austenitic
stainless steels and cladding of these metals cannot
be
inspected by this method.