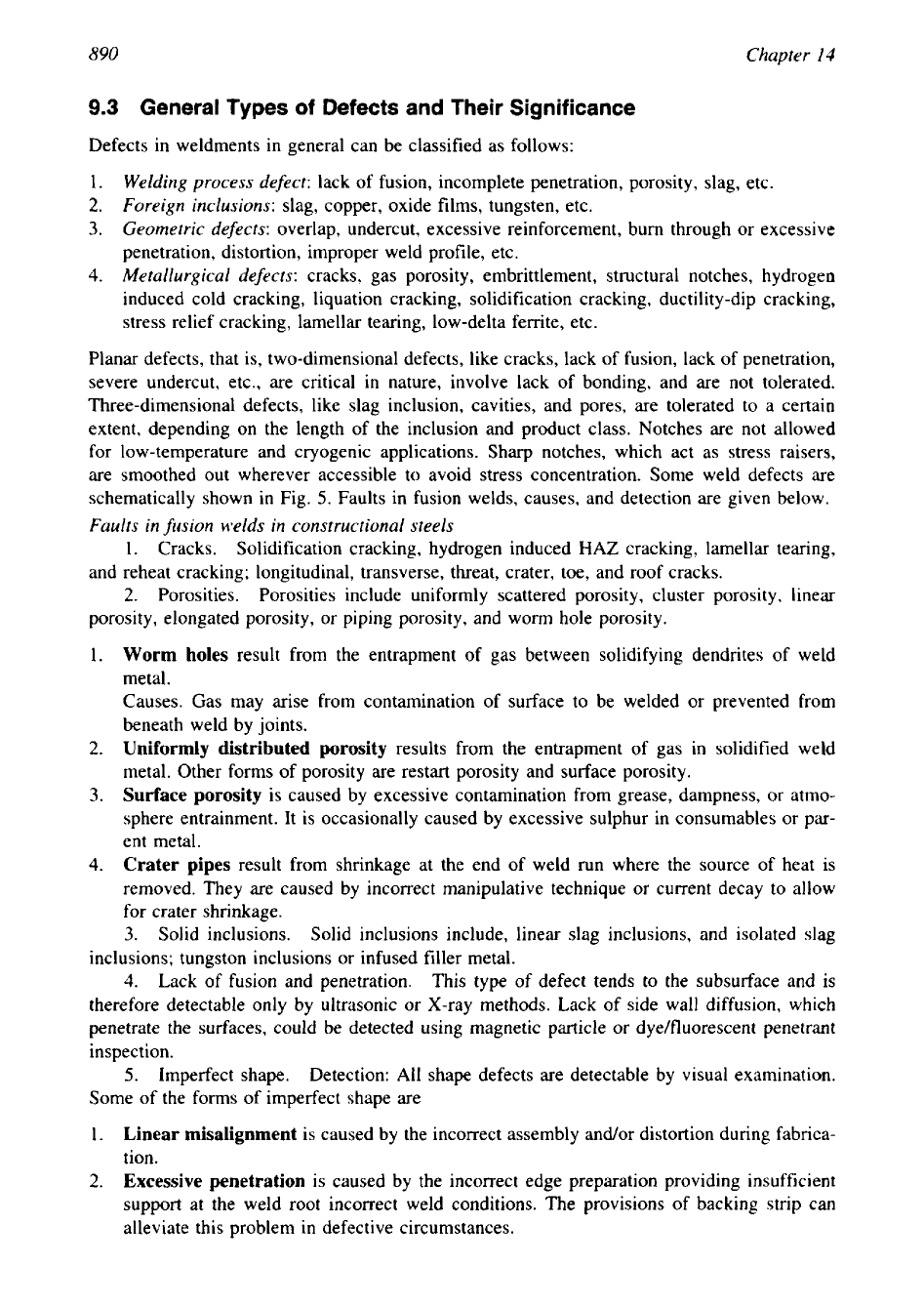
890
Chapter 14
9.3
General Types of Defects and Their Significance
Defects in weldments in general can be classified as follows:
1.
Welding process defect:
lack of fusion, incomplete penetration, porosity, slag, etc.
2.
Foreign inclusions:
slag, copper, oxide films, tungsten, etc.
3.
Geometric defects:
overlap, undercut, excessive reinforcement, burn through or excessive
penetration, distortion, improper weld profile, etc.
4.
Metallurgical defects:
cracks, gas porosity, embrittlement, structural notches, hydrogen
induced cold cracking, liquation cracking, solidification cracking, ductility-dip cracking,
stress relief cracking, lamellar tearing, low-delta ferrite, etc.
Planar defects, that is, two-dimensional defects, like cracks, lack of fusion, lack of penetration,
severe undercut, etc., are critical in nature, involve lack of bonding, and are not tolerated.
Three-dimensional defects, like slag inclusion, cavities, and pores, are tolerated to a certain
extent, depending on the length of the inclusion and product class. Notches are not allowed
for low-temperature and cryogenic applications. Sharp notches, which act as stress raisers,
are smoothed out wherever accessible to avoid stress concentration. Some weld defects are
schematically shown in Fig.
5.
Faults
in
fusion welds, causes, and detection are given below.
Faults in fitsion welds in constructional steels
1.
Cracks. Solidification cracking, hydrogen induced
HAZ
cracking, lamellar tearing,
and reheat cracking; longitudinal, transverse, threat, crater, toe, and roof cracks.
2.
Porosities. Porosities include uniformly scattered porosity, cluster porosity, linear
porosity, elongated porosity, or piping porosity, and worm hole porosity.
Worm holes
result from the entrapment of gas between solidifying dendrites of weld
metal.
Causes. Gas may arise from contamination of surface to be welded or prevented from
beneath weld by joints.
Uniformly distributed porosity
results from the entrapment of gas in solidified weld
metal. Other forms of porosity are restart porosity and surface porosity.
Surface porosity
is caused by excessive contamination from grease, dampness, or atmo-
sphere entrainment. It is occasionally caused by excessive sulphur in consumables or par-
ent metal.
Crater pipes
result from shrinkage at the end of weld run where the source of heat is
removed. They are caused by incorrect manipulative technique or current decay to allow
for crater shrinkage.
3.
Solid inclusions. Solid inclusions include, linear slag inclusions, and isolated slag
inclusions; tungston inclusions or infused filler metal.
4.
Lack of fusion and penetration. This type
of defect tends to the subsurface and
is
therefore detectable only by ultrasonic or X-ray methods. Lack of side wall diffusion, which
penetrate the surfaces, could be detected using magnetic particle or dye/fluorescent penetrant
inspection.
5.
Imperfect shape.
Detection: All shape defects are detectable by visual examination.
Some of the forms of imperfect shape are
1.
Linear misalignment
is caused by the incorrect assembly andor distortion during fabrica-
tion.
2.
Excessive penetration
is caused by the incorrect edge preparation providing insufficient
support at the weld root incorrect weld conditions. The provisions of backing strip can
alleviate this problem in defective circumstances.