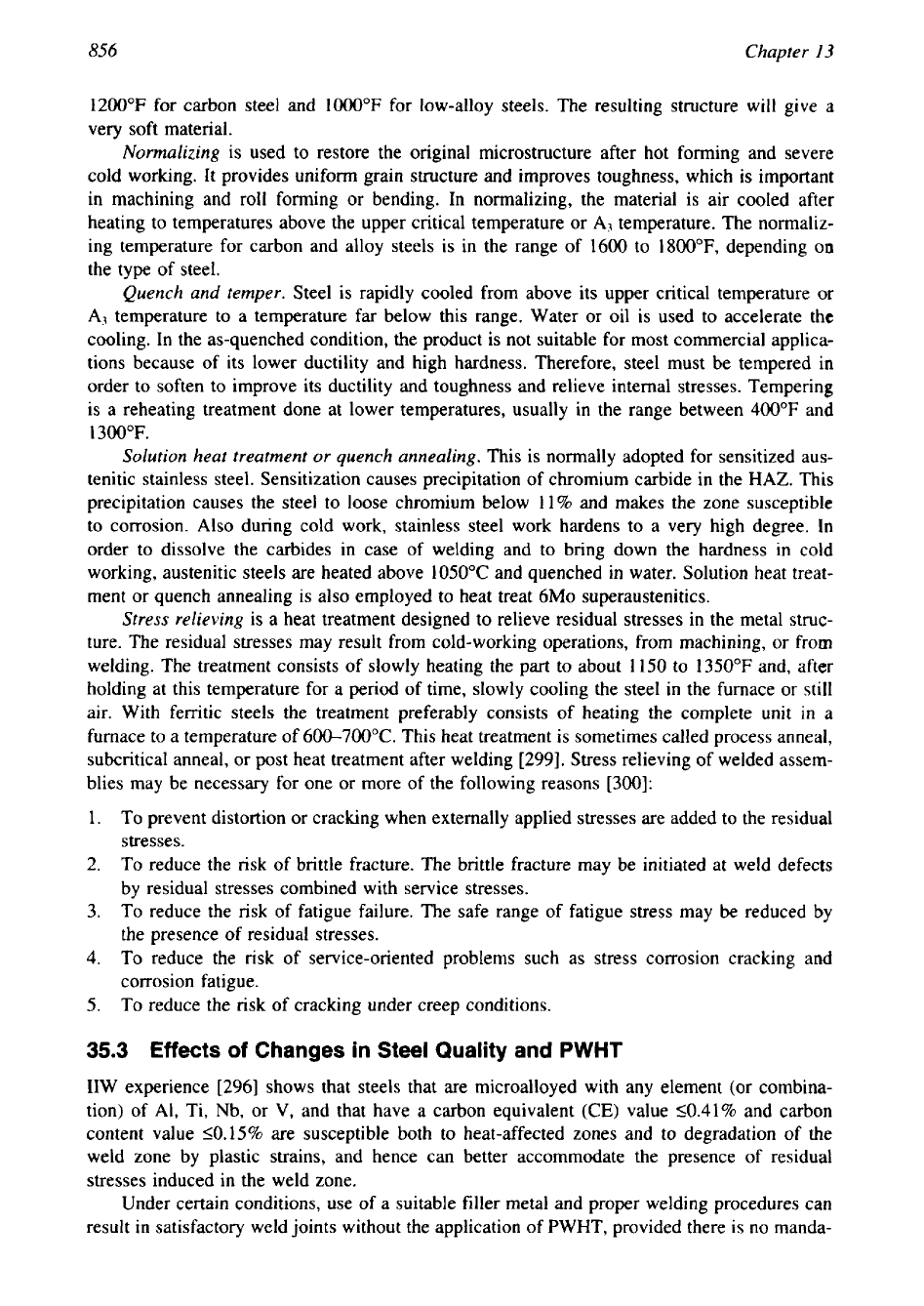
856
Chapter
13
1200°F for carbon steel and 1000°F for low-alloy steels. The resulting structure will give a
very soft material.
Normalizing
is used to restore the original microstructure after hot forming and severe
cold working. It provides uniform grain structure and improves toughness, which is important
in machining and roll forming or bending. In normalizing, the material is air cooled after
heating to temperatures above the upper critical temperature or A3 temperature. The normaliz-
ing temperature for carbon and alloy steels
is
in the range of 1600 to 1800"F, depending
on
the type of steel.
Quench and temper.
Steel is rapidly cooled from above its upper critical temperature
or
A3 temperature to a temperature far below this range. Water or oil is used to accelerate the
cooling. In the as-quenched condition, the product is not suitable for most commercial applica-
tions because of its lower ductility and high hardness. Therefore, steel must be tempered in
order to soften to improve its ductility and toughness and relieve internal stresses. Tempering
is a reheating treatment done at lower temperatures, usually in the range between
400°F
and
1300°F.
Solution heat treatment
or
quench annealing.
This is normally adopted for sensitized aus-
tenitic stainless steel. Sensitization causes precipitation of chromium carbide in the
HAZ.
This
precipitation causes the steel to loose chromium below 11% and makes the zone susceptible
to corrosion. Also during cold work, stainless steel work hardens to a very high degree.
In
order to dissolve the carbides in case of welding and to bring down the hardness in cold
working, austenitic steels are heated above 1050°C and quenched in water. Solution heat treat-
ment or quench annealing is also employed to heat treat 6Mo superaustenitics.
Stress relieving
is a heat treatment designed to relieve residual stresses in the metal struc-
ture. The residual stresses may result from cold-working operations, from machining, or from
welding. The treatment consists of slowly heating the part to about 1150 to
1350°F
and, after
holding at this temperature for a period of time, slowly cooling the steel in the furnace or still
air. With ferritic steels the treatment preferably consists of heating the complete
unit
in
a
furnace to a temperature of 600-700"C. This heat treatment is sometimes called process anneal,
subcritical anneal, or post heat treatment after welding [299]. Stress relieving of welded assem-
blies may be necessary for one or more of the following reasons
[300]:
1. To prevent distortion or cracking when externally applied stresses are added to the residual
stresses.
2.
To
reduce the risk of brittle fracture. The brittle fracture may be initiated at weld defects
by residual stresses combined with service stresses.
3.
To
reduce the risk of fatigue failure. The safe range of fatigue stress may be reduced by
the presence of residual stresses.
4.
To reduce the risk of service-oriented problems such as stress corrosion cracking and
corrosion fatigue.
5.
To reduce the risk of cracking under creep conditions.
35.3
Effects
of
Changes in Steel Quality and PWHT
IIW
experience [296] shows that steels that are microalloyed with any element (or combina-
tion) of Al, Ti, Nb, or
V,
and that have a carbon equivalent (CE) value <0.41% and carbon
content value 10.15% are susceptible both to heat-affected zones and to degradation of the
weld zone by plastic strains, and hence can better accommodate the presence
of
residual
stresses induced in the weld zone.
Under certain conditions, use of a suitable filler metal and proper welding procedures can
result in satisfactory weld joints without the application of PWHT, provided there
is
no manda-