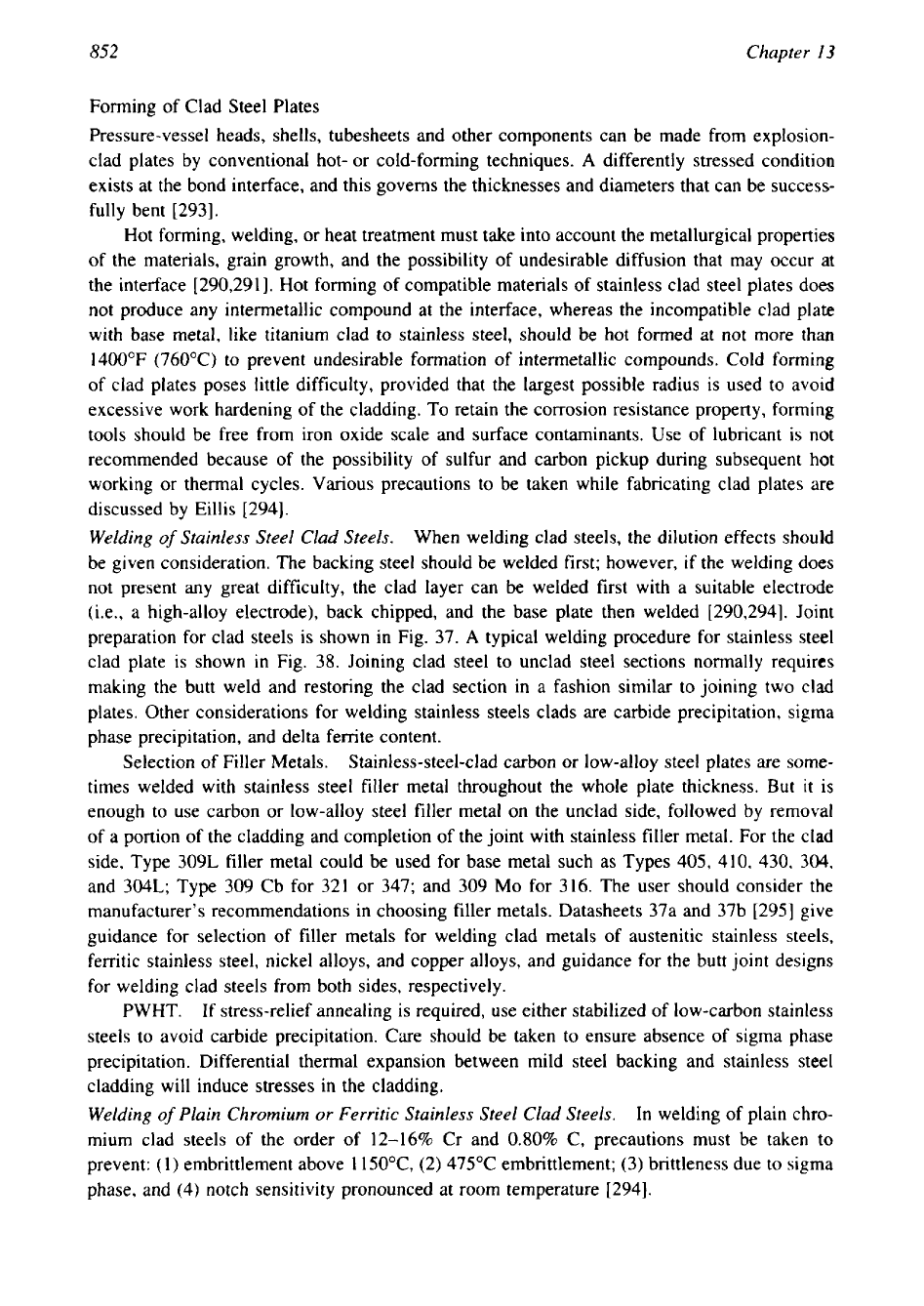
852
Chapter
I3
Forming of Clad Steel Plates
Pressure-vessel heads, shells, tubesheets and other components can be made from explosion-
clad plates by conventional hot- or cold-forming techniques.
A
differently stressed condition
exists at the bond interface, and this governs the thicknesses and diameters that can be success-
fully bent [293].
Hot forming, welding, or heat treatment must take into account the metallurgical properties
of the materials, grain growth, and the possibility of undesirable diffusion that may occur at
the interface [290,291]. Hot forming of compatible materials of stainless clad steel plates does
not produce any intermetallic compound at the interface, whereas the incompatible clad plate
with base metal, like titanium clad to stainless steel, should be hot formed at not more than
1400°F (760°C) to prevent undesirable formation of intermetallic compounds. Cold forming
of
clad plates poses little difficulty, provided that the largest possible radius is used to avoid
excessive work hardening of the cladding. To retain the corrosion resistance property, forming
tools should be free from iron oxide scale and surface contaminants. Use of lubricant is not
recommended because
of
the possibility of sulfur and carbon pickup during subsequent hot
working or thermal cycles. Various precautions to be taken while fabricating clad plates are
discussed by Eillis [294].
Welding
of
Stainless
Steel
Clad Steels.
When welding clad steels, the dilution effects should
be given consideration. The backing steel should be welded first; however, if the welding does
not present any great difficulty, the clad layer can be welded first with a suitable electrode
(i.e,, a high-alloy electrode), back chipped, and the base plate then welded [290,294]. Joint
preparation for clad steels is shown in Fig. 37.
A
typical welding procedure for stainless steel
clad plate is shown in Fig. 38. Joining clad steel to unclad steel sections normally requires
making the butt weld and restoring the clad section in a fashion similar to joining two clad
plates. Other considerations for welding stainless steels clads are carbide precipitation, sigma
phase precipitation, and delta ferrite content.
Selection of Filler Metals.
Stainless-steel-clad carbon or low-alloy steel plates are some-
times welded with stainless steel filler metal throughout the whole plate thickness. But
it
is
enough to use carbon or low-alloy steel filler metal on the unclad side, followed by removal
of a portion of the cladding and completion of the joint with stainless filler metal. For the clad
side, Type 309L filler metal could be used for base metal such as Types 405, 410, 430,
304,
and 304L; Type 309 Cb for 321 or 347; and 309
MO
for 316. The user should consider the
manufacturer’s recommendations in choosing filler metals. Datasheets 37a and 37b [295] give
guidance for selection of filler metals for welding clad metals of austenitic stainless steels,
ferritic stainless steel, nickel alloys, and copper alloys, and guidance for the butt joint designs
for welding clad steels from both sides, respectively.
PWHT.
If stress-relief annealing is required, use either stabilized of low-carbon stainless
steels to avoid carbide precipitation. Care should be taken to ensure absence of sigma phase
precipitation. Differential thermal expansion between mild steel backing and stainless steel
cladding will induce stresses in the cladding.
Welding
of
Plain Chromium
or
Ferritic Stainless Steel Clad Steels.
In
welding of plain chro-
mium clad steels of the order of 12-16% Cr and
0.80%
C, precautions must be taken to
prevent:
(1)
embrittlement above 1 15OoC, (2) 475°C embrittlement; (3) brittleness due to sigma
phase, and
(4)
notch sensitivity pronounced at room temperature [294].