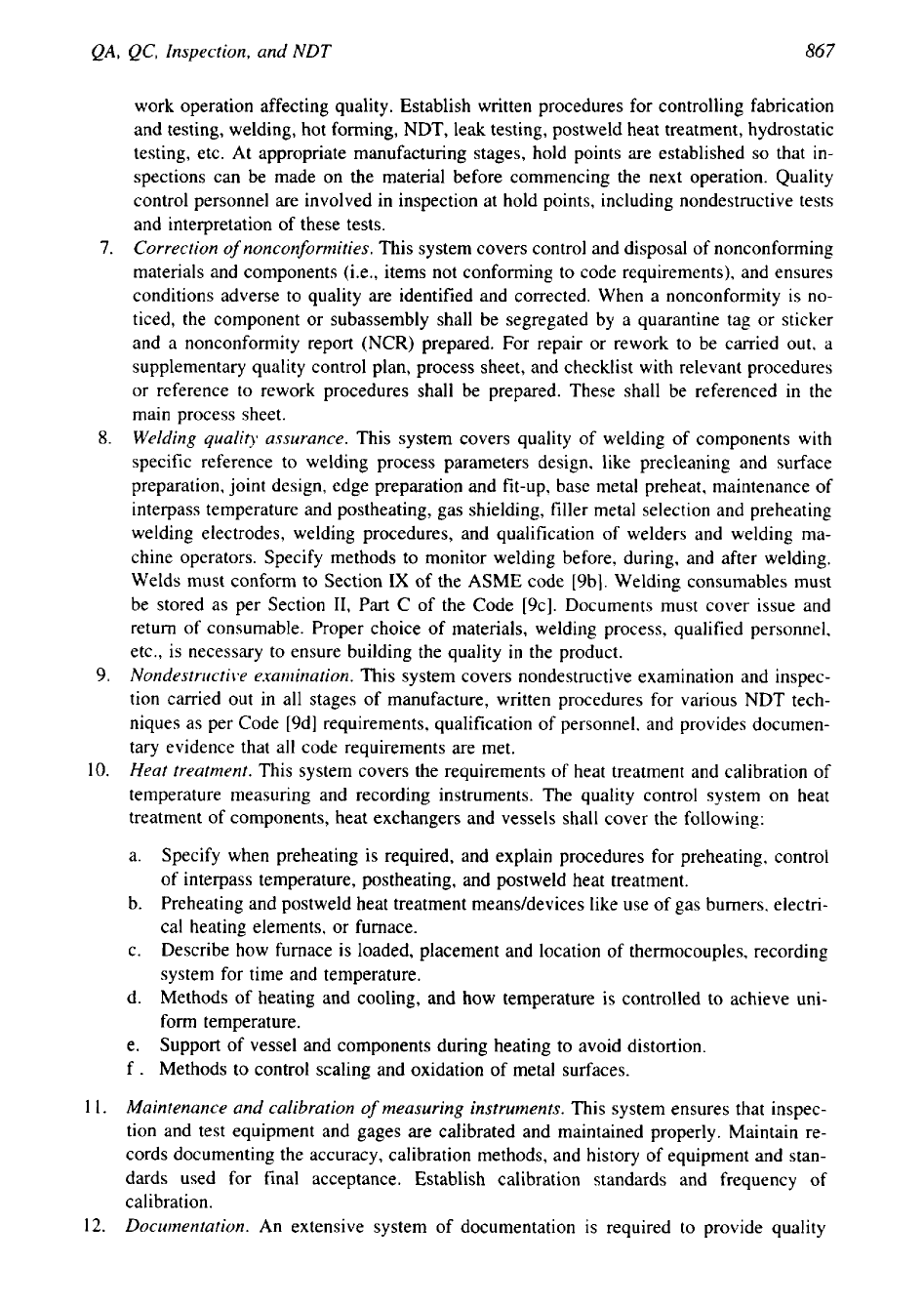
867
QA, QC, Inspection, and
NDT
work operation affecting quality. Establish written procedures for controlling fabrication
and testing, welding, hot forming, NDT, leak testing, postweld heat treatment, hydrostatic
testing, etc. At appropriate manufacturing stages, hold points are established
so
that in-
spections can be made on the material before commencing the next operation. Quality
control personnel are involved in inspection at hold points, including nondestructive tests
and interpretation of these tests.
7.
Correction of nonconformities.
This system covers control and disposal of nonconforming
materials and components (Le., items not conforming to code requirements), and ensures
conditions adverse to quality are identified and corrected. When a nonconformity is no-
ticed, the component or subassembly shall be segregated by a quarantine tag or sticker
and a nonconformity report (NCR) prepared. For repair or rework to be carried out, a
supplementary quality control plan, process sheet, and checklist with relevant procedures
or reference to rework procedures shall be prepared. These shall be referenced
in
the
main process sheet.
8.
Welding quality assurance.
This system covers quality of welding of components with
specific reference to welding process parameters design, like precleaning and surface
preparation, joint design, edge preparation and fit-up, base metal preheat, maintenance of
interpass temperature and postheating, gas shielding, filler metal selection and preheating
welding electrodes, welding procedures, and qualification of welders and welding ma-
chine operators. Specify methods to monitor welding before, during, and after welding.
Welds must conform to Section
IX
of the ASME code [9b]. Welding consumables must
be stored as per Section
11,
Part C of the Code [Sc]. Documents must cover issue and
return of consumable. Proper choice of materials, welding process, qualified personnel,
etc., is necessary to ensure building the quality in the product.
9.
Nondestriictiite examination.
This system covers nondestructive examination and inspec-
tion carried out in all stages of manufacture, written procedures for various NDT tech-
niques as per Code [9d] requirements, qualification of personnel, and provides documen-
tary evidence that all code requirements are met.
10.
Heat treatment.
This system covers the requirements of heat treatment and calibration of
temperature measuring and recording instruments. The quality control system on heat
treatment of components, heat exchangers and vessels shall cover the following:
a. Specify when preheating
is
required, and explain procedures for preheating, control
of interpass temperature, postheating, and postweld heat treatment.
b. Preheating and postweld heat treatment meanddevices like use of gas burners, electri-
cal heating elements, or furnace.
c. Describe how furnace is loaded, placement and location of thermocouples, recording
system for time and temperature.
d. Methods of heating and cooling, and how temperature is controlled to achieve uni-
form temperature.
e. Support of vessel and components during heating to avoid distortion.
f
.
Methods to control scaling and oxidation of metal surfaces.
1
1.
Maintenance and calibration
of
measuring instruments.
This system ensures that inspec-
tion and test equipment and gages are calibrated and maintained properly. Maintain re-
cords documenting the accuracy, calibration methods, and history of equipment and stan-
dards used for final acceptance. Establish calibration standards and frequency
of
calibration.
12. Documentation.
An extensive system of documentation is required to provide quality