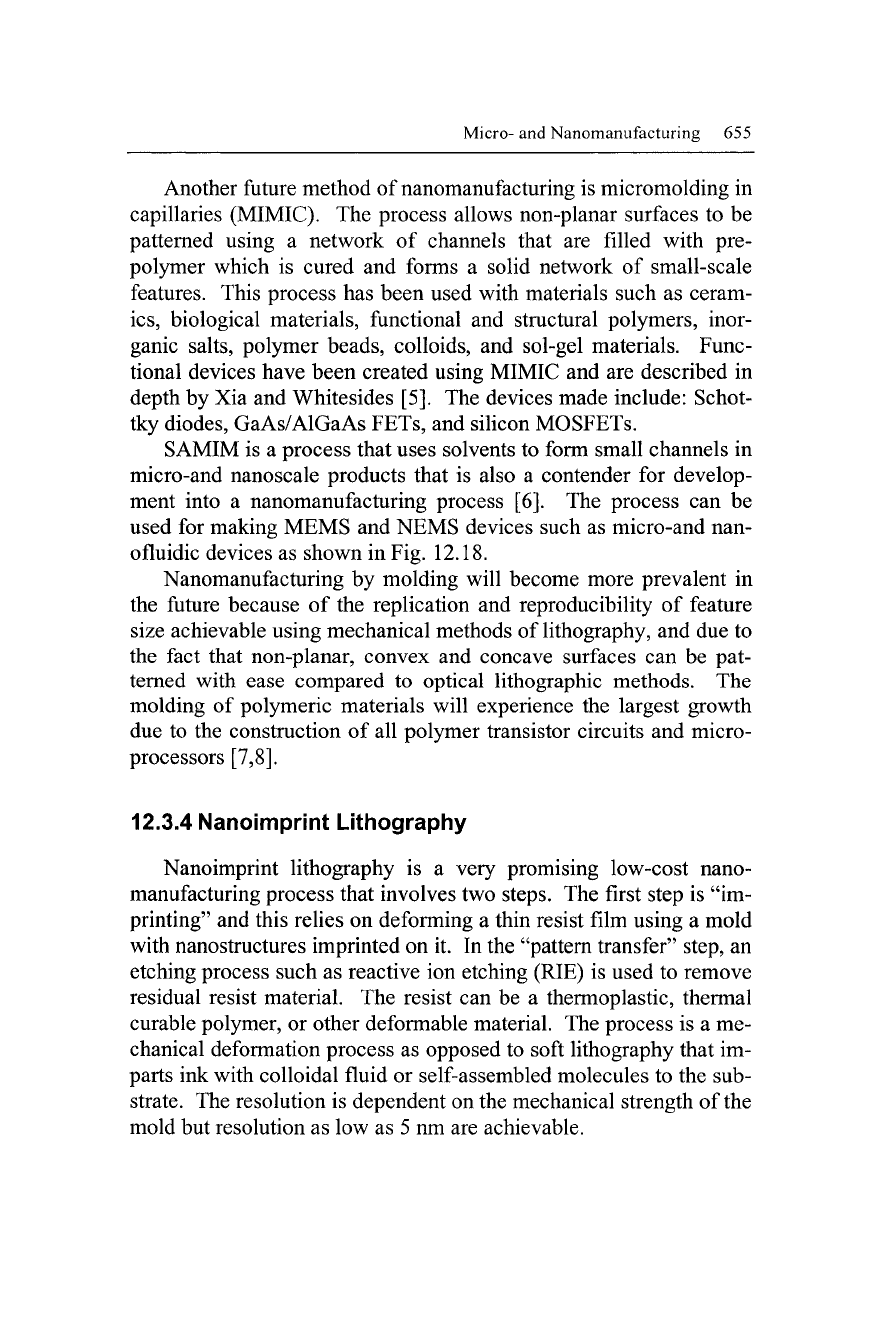
Micro- and Nanomanufacturing 655
Another future method of nanomanufacturing is micromolding in
capillaries (MIMIC). The process allows non-planar surfaces to be
patterned using a network of channels that are filled with pre-
polymer which is cured and forms a solid network of small-scale
features. This process has been used with materials such as ceram-
ics,
biological materials, functional and structural polymers, inor-
ganic salts, polymer beads, colloids, and sol-gel materials. Func-
tional devices have been created using MIMIC and are described in
depth by Xia and Whitesides [5]. The devices made include: Schot-
tky diodes, GaAs/AlGaAs FETs, and silicon MOSFETs.
SAMIM is a process that uses solvents to form small channels in
micro-and nanoscale products that is also a contender for develop-
ment into a nanomanufacturing process [6]. The process can be
used for making MEMS and NEMS devices such as micro-and nan-
ofluidic devices as shown in Fig. 12.18.
Nanomanufacturing by molding will become more prevalent in
the future because of the replication and reproducibility of feature
size achievable using mechanical methods of lithography, and due to
the fact that non-planar, convex and concave surfaces can be pat-
terned with ease compared to optical lithographic methods. The
molding of polymeric materials will experience the largest growth
due to the construction of all polymer transistor circuits and micro-
processors
[7,8].
12.3.4 Nanoimprint Lithography
Nanoimprint lithography is a very promising low-cost nano-
manufacturing process that involves two steps. The first step is "im-
printing" and this relies on deforming a thin resist film using a mold
with nanostructures imprinted on it. In the "pattern transfer" step, an
etching process such as reactive ion etching (RIE) is used to remove
residual resist material. The resist can be a thermoplastic, thermal
curable polymer, or other deformable material. The process is a me-
chanical deformation process as opposed to soft lithography that im-
parts ink with colloidal fluid or self-assembled molecules to the sub-
strate. The resolution is dependent on the mechanical strength of the
mold but resolution as low as 5 nm are achievable.