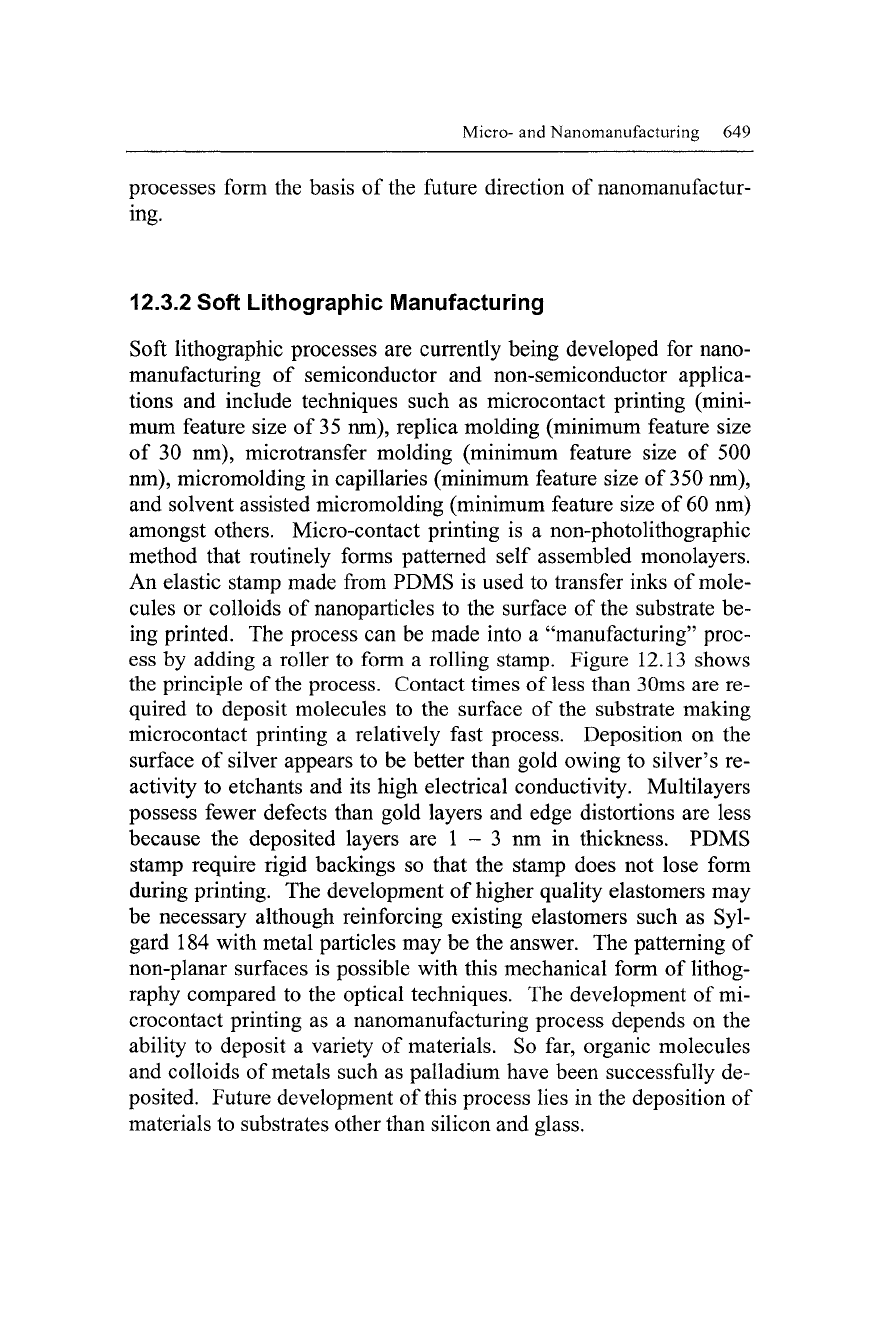
Micro- and Nanomanufacturing 649
processes form the basis of the future direction of nanomanufactur-
ing.
12.3.2 Soft Lithographic IVIanufacturing
Soft lithographic processes are currently being developed for nano-
manufacturing of semiconductor and non-semiconductor applica-
tions and include techniques such as microcontact printing (mini-
mum feature size of 35 nm), replica molding (minimum feature size
of 30 nm), microtransfer molding (minimum feature size of 500
nm),
micromolding in capillaries (minimum feature size of 350 nm),
and solvent assisted micromolding (minimum feature size of 60 nm)
amongst others. Micro-contact printing is a non-photolithographic
method that routinely forms patterned self assembled monolayers.
An elastic stamp made from PDMS is used to transfer inks of mole-
cules or colloids of nanoparticles to the surface of the substrate be-
ing printed. The process can be made into a "manufacturing" proc-
ess by adding a roller to form a rolling stamp. Figure 12.13 shows
the principle of the process. Contact times of less than 30ms are re-
quired to deposit molecules to the surface of the substrate making
microcontact printing a relatively fast process. Deposition on the
surface of silver appears to be better than gold owing to silver's re-
activity to etchants and its high electrical conductivity. Multilayers
possess fewer defects than gold layers and edge distortions are less
because the deposited layers are 1 - 3 nm in thickness. PDMS
stamp require rigid backings so that the stamp does not lose form
during printing. The development of higher quality elastomers may
be necessary although reinforcing existing elastomers such as Syl-
gard 184 with metal particles may be the answer. The patterning of
non-planar surfaces is possible with this mechanical form of hthog-
raphy compared to the optical techniques. The development of mi-
crocontact printing as a nanomanufacturing process depends on the
ability to deposit a variety of materials. So far, organic molecules
and colloids of metals such as palladium have been successfully de-
posited. Future development of this process lies in the deposition of
materials to substrates other than silicon and glass.