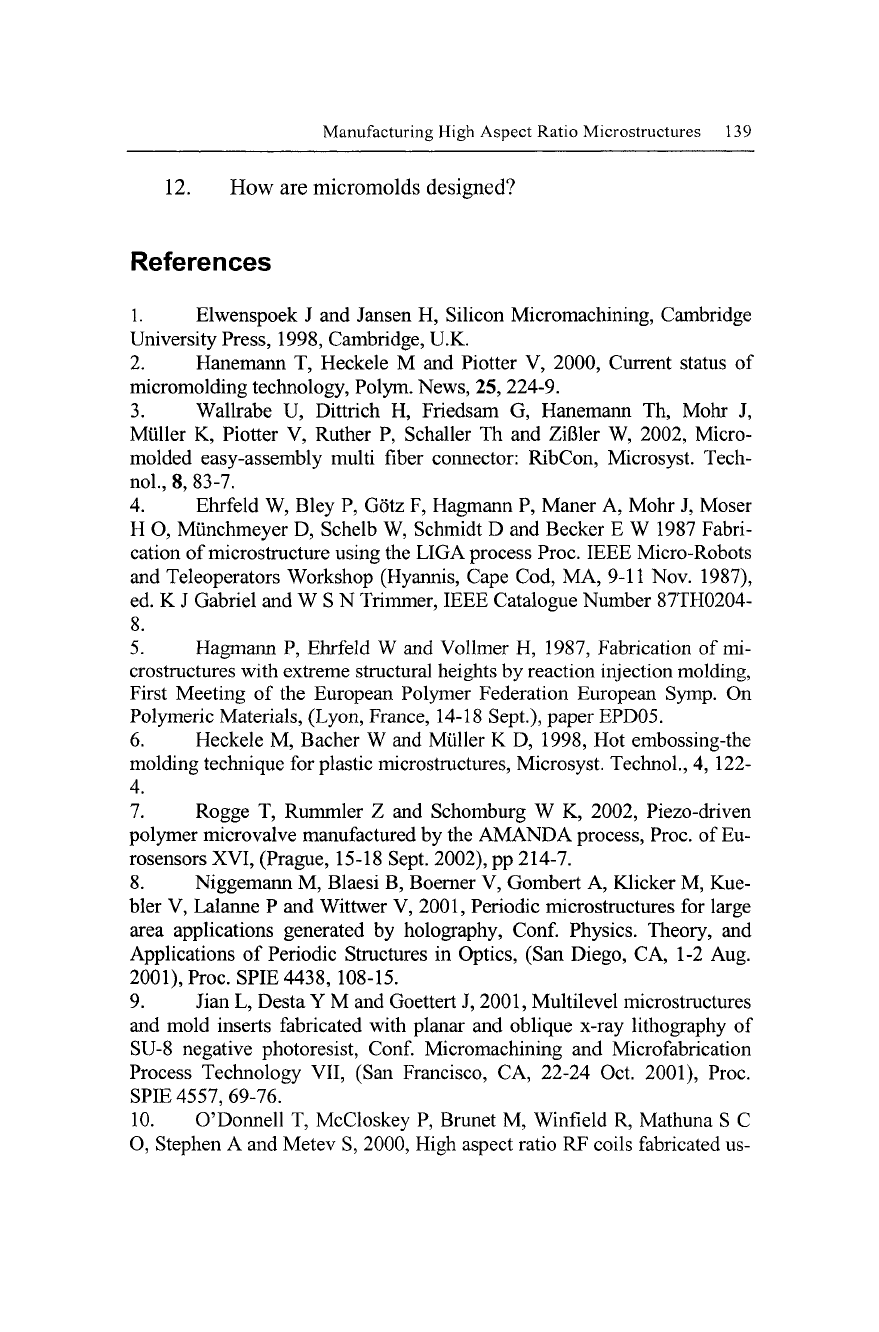
Manufacturing High Aspect Ratio Microstructures 139
12.
How are micromolds designed?
References
1.
Elwenspoek J and Jansen H, Silicon Micromachining, Cambridge
University Press, 1998, Cambridge, U.K.
2.
Hanemann T, Heckele M and Plotter V, 2000, Current status of
micromolding technology, Polym. News, 25, 224-9.
3.
Wallrabe U, Dittrich H, Friedsam G, Hanemann Th, Mohr J,
Muller K, Plotter V, Ruther P, Schaller Th and ZiBler W, 2002, Micro-
molded easy-assembly multi fiber connector: RibCon, Microsyst. Tech-
nol.,
8, 83-7.
4.
Ehrfeld W, Bley P, Gotz F, Hagmann P, Maner A, Mohr J, Moser
H O, Miinchmeyer D, Schelb W, Schmidt D and Becker E W 1987 Fabri-
cation of microstructure using the LIGA process Proc. IEEE Micro-Robots
and Teleoperators Workshop (Hyannis, Cape Cod, MA, 9-11 Nov. 1987),
ed. K J Gabriel aad W S N Trimmer, IEEE Catalogue Number 87TH0204-
8.
5.
Hagmann P, Ehrfeld W and Vollmer H, 1987, Fabrication of mi-
crostructures with extreme structural heights by reaction injection molding,
First Meeting of the European Polymer Federation European Symp. On
Polymeric Materials, (Lyon, France, 14-18 Sept.), paper EPD05.
6. Heckele M, Bacher W and Mtiller K D, 1998, Hot embossing-the
molding technique for plastic microstructures, Microsyst. Technol., 4, 122-
4.
7.
Rogge T, Rummler Z and Schomburg W K, 2002, Piezo-driven
polymer microvalve manufactured by the AMANDA process, Proc. of Eu-
rosensors XVI, (Prague, 15-18 Sept. 2002), pp 214-7.
8. Niggemann M, Blaesi B, Boemer V, Gombert A, Klicker M, Kue-
bler V, Lalanne P and Wittwer V, 2001, Periodic microstructures for large
area applications generated by holography,
Conf.
Physics. Theory, and
Applications of Periodic Structures in Optics, (San Diego, CA, 1-2 Aug.
2001),
Proc. SPIE 4438,108-15.
9. Jian L, Desta Y M and Goettert J, 2001, Multilevel microstructures
and mold inserts fabricated with planar and oblique x-ray lithography of
SU-8 negative photoresist, Conf Micromachining and Microfabrication
Process Technology VII, (San Francisco, CA, 22-24 Oct. 2001), Proc.
SPIE 4557, 69-76.
10.
O'Donnell T, McCloskey P, Brunet M, Winfield R, Mathuna S C
O, Stephen A and Metev S, 2000, High aspect ratio RF coils fabricated us-