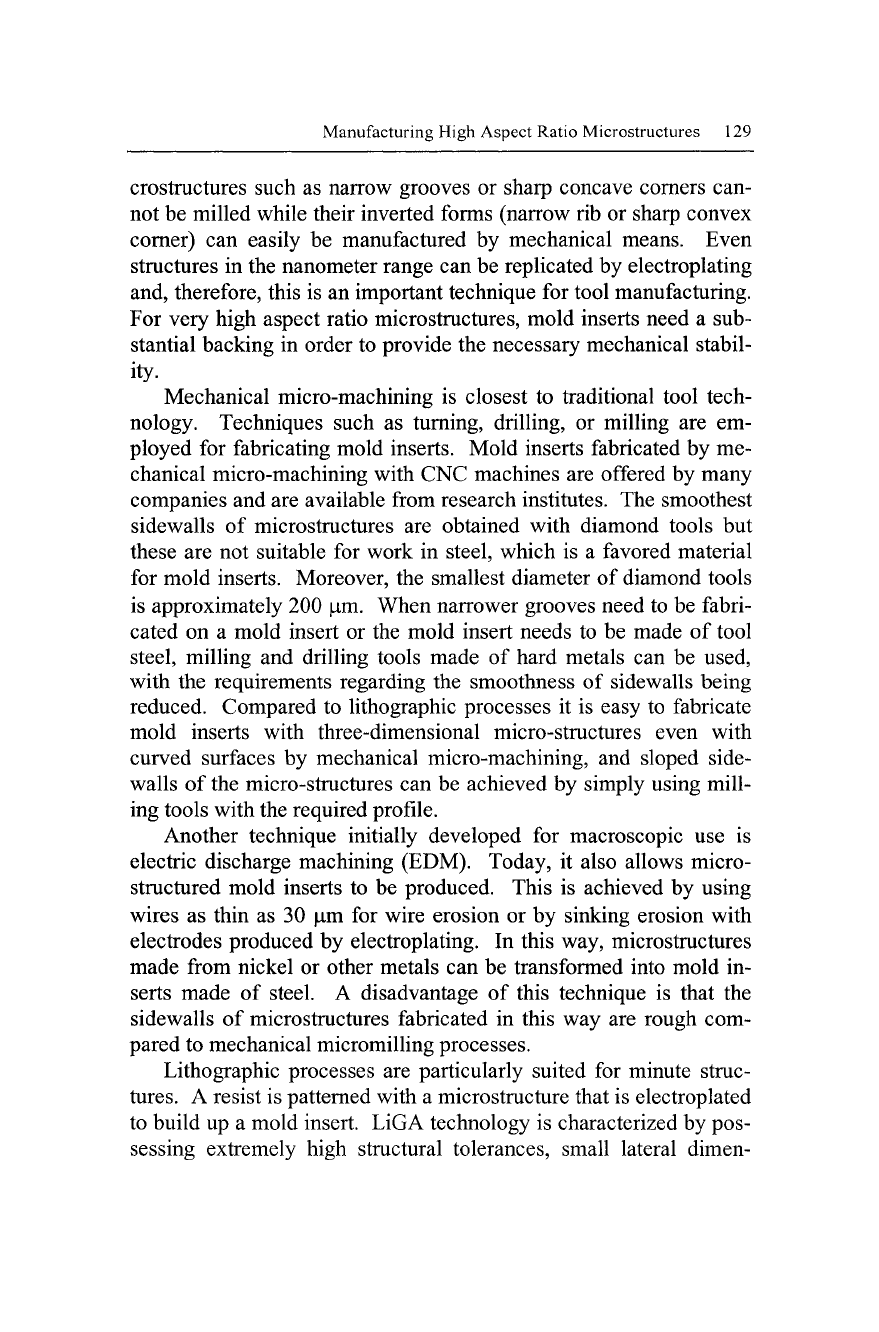
Manufacturing High Aspect Ratio Microstructures 129
crostructures such as narrow grooves or sharp concave comers can-
not be milled while their inverted forms (narrow rib or sharp convex
comer) can easily be manufactured by mechanical means. Even
stmctures in the nanometer range can be replicated by electroplating
and, therefore, this is an important technique for tool manufacturing.
For very high aspect ratio microstmctures, mold inserts need a sub-
stantial backing in order to provide the necessary mechanical stabil-
ity.
Mechanical micro-machining is closest to traditional tool tech-
nology. Techniques such as tuming, drilling, or milling are em-
ployed for fabricating mold inserts. Mold inserts fabricated by me-
chanical micro-machining with CNC machines are offered by many
companies and are available from research institutes. The smoothest
sidewalls of microstmctures are obtained with diamond tools but
these are not suitable for work in steel, which is a favored material
for mold inserts. Moreover, the smallest diameter of diamond tools
is approximately 200 |Lim. When narrower grooves need to be fabri-
cated on a mold insert or the mold insert needs to be made of tool
steel, milling and drilling tools made of hard metals can be used,
with the requirements regarding the smoothness of sidewalls being
reduced. Compared to lithographic processes it is easy to fabricate
mold inserts with three-dimensional micro-stmctures even with
curved surfaces by mechanical micro-machining, and sloped side-
walls of the micro-stmctures can be achieved by simply using mill-
ing tools with the required profile.
Another technique initially developed for macroscopic use is
electric discharge machining (EDM). Today, it also allows micro-
stmctured mold inserts to be produced. This is achieved by using
wires as thin as 30 |Lim for wire erosion or by sinking erosion with
electrodes produced by electroplating. In this way, microstmctures
made from nickel or other metals can be transformed into mold in-
serts made of steel. A disadvantage of this technique is that the
sidewalls of microstmctures fabricated in this way are rough com-
pared to mechanical micromilling processes.
Lithographic processes are particularly suited for minute stmc-
tures.
A resist is patterned with a microstmcture that is electroplated
to build up a mold insert. LiGA technology is characterized by pos-
sessing extremely high stmctural tolerances, small lateral dimen-