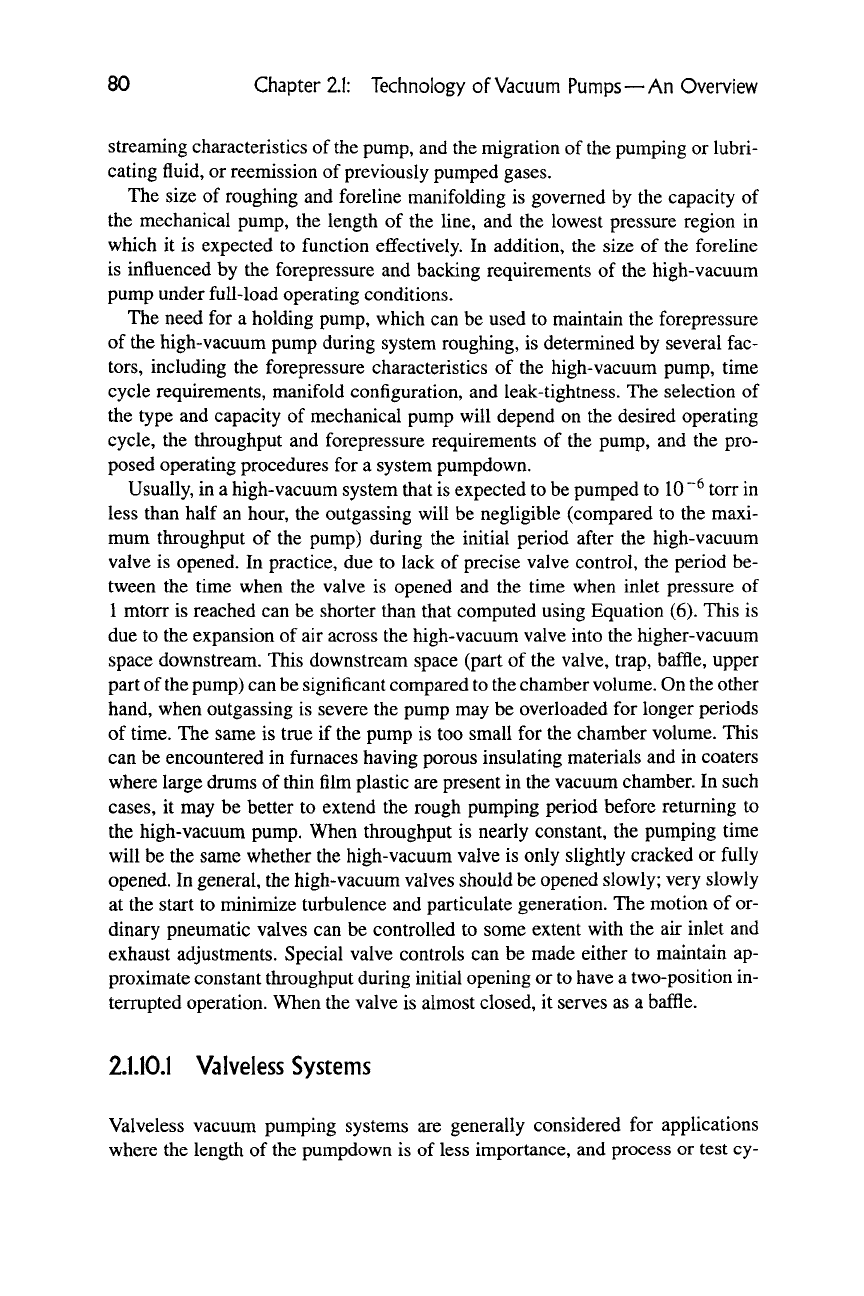
80 Chapter
2.1:
Technology of
Vacuum
Pumps—An Overview
streaming characteristics of the pump, and the migration of the pumping or lubri-
cating fluid, or reemission of previously pumped gases.
The size of roughing and foreline manifolding is governed by the capacity of
the mechanical pump, the length of the line, and the lowest pressure region in
which it is expected to function effectively. In addition, the size of the foreline
is influenced by the forepressure and backing requirements of the high-vacuum
pump under full-load operating conditions.
The need for a holding pump, which can be used to maintain the forepressure
of the high-vacuum pump during system roughing, is determined by several fac-
tors,
including the forepressure characteristics of the high-vacuum pump, time
cycle requirements, manifold configuration, and leak-tightness. The selection of
the type and capacity of mechanical pump will depend on the desired operating
cycle, the throughput and forepressure requirements of the pump, and the pro-
posed operating procedures for a system pumpdown.
Usually, in a high-vacuum system that is expected to be pumped to
10 ~^
torr in
less than half an hour, the outgassing will be negligible (compared to the maxi-
mum throughput of the pump) during the initial period after the high-vacuum
valve is opened. In practice, due to lack of precise valve control, the period be-
tween the time when the valve is opened and the time when inlet pressure of
1 mtorr is reached can be shorter than that computed using Equation (6). This is
due to the expansion of air across the high-vacuum valve into the higher-vacuum
space downstream. This downstream space (part of the valve, trap, baffle, upper
part of the pump) can be significant compared to the chamber
volume.
On the other
hand, when outgassing is severe the pump may be overloaded for longer periods
of time. The same is true if the pump is too small for the chamber volume. This
can be encountered in furnaces having porous insulating materials and in coaters
where large drums of thin film plastic are present in the vacuum chamber. In such
cases,
it may be better to extend the rough pumping period before returning to
the high-vacuum pump. When throughput is nearly constant, the pumping time
will be the same whether the high-vacuum valve is only slightly cracked or fully
opened. In general, the high-vacuum valves should be opened slowly; very slowly
at the start to minimize turbulence and particulate generation. The motion of or-
dinary pneumatic valves can be controlled to some extent with the air inlet and
exhaust adjustments. Special valve controls can be made either to maintain ap-
proximate constant throughput during initial opening or to have a two-position in-
terrupted operation. When the valve is almost closed, it serves as a baffle.
2.1.10.1 Valveless Systems
Valveless vacuum pumping systems are generally considered for applications
where the length of the pumpdown is of less importance, and process or test cy-