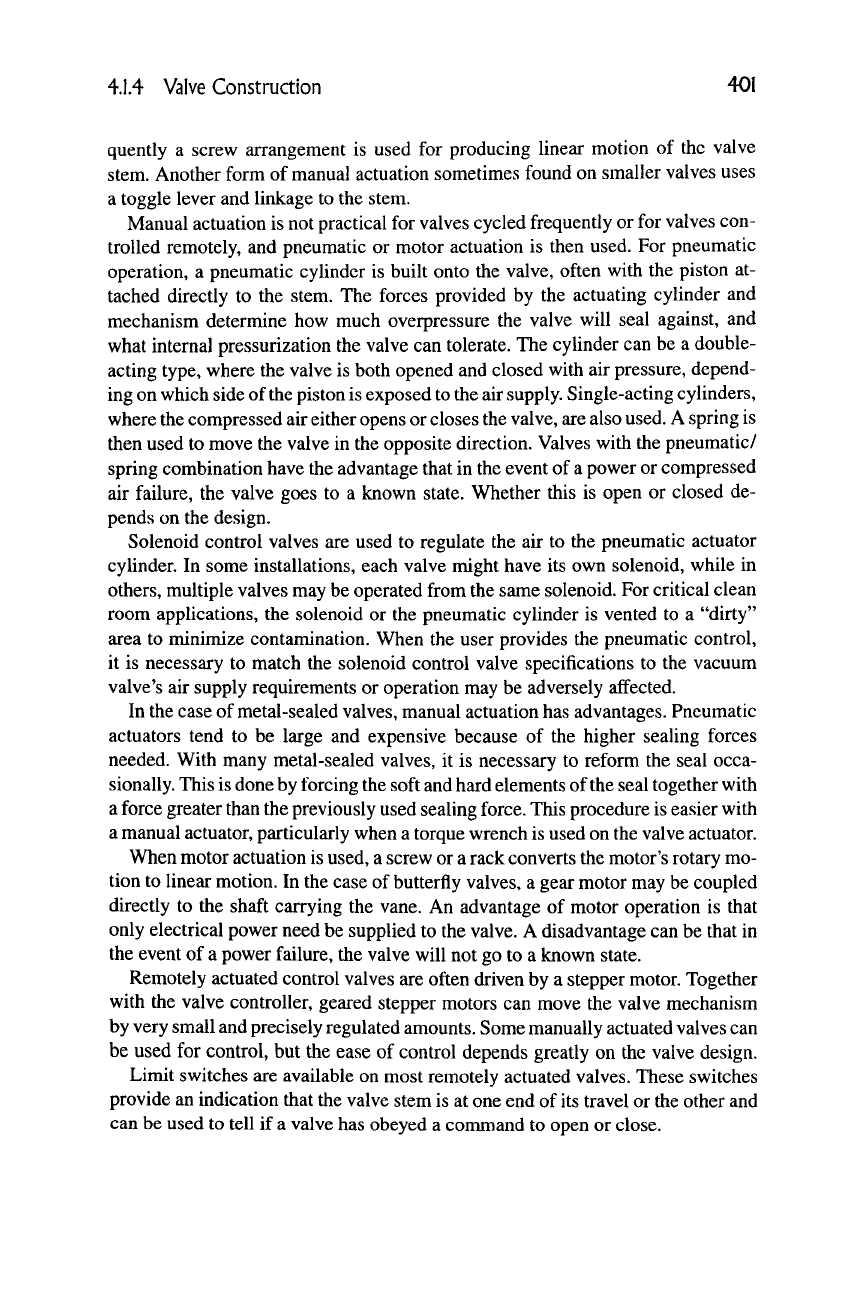
4.1.4 Valve Construction 401
quently a screw arrangement is used for producing linear motion of the valve
stem. Another form of manual actuation sometimes found on smaller valves uses
a toggle lever and linkage to the stem.
Manual actuation is not practical for valves cycled frequently or for valves con-
trolled remotely, and pneumatic or motor actuation is then used. For pneumatic
operation, a pneumatic cylinder is built onto the valve, often with the piston at-
tached directly to the stem. The forces provided by the actuating cylinder and
mechanism determine how much overpressure the valve will seal against, and
what internal pressurization the valve can tolerate. The cylinder can be a double-
acting type, where the valve is both opened and closed with air pressure, depend-
ing on which side of the piston is exposed to the air
supply.
Single-acting cylinders,
where the compressed air either opens or closes the valve, are also used. A spring is
then used to move the valve in the opposite direction. Valves with the pneumatic/
spring combination have the advantage that in the event of a power or compressed
air failure, the valve goes to a known state. Whether this is open or closed de-
pends on the design.
Solenoid control valves are used to regulate the air to the pneumatic actuator
cylinder. In some installations, each valve might have its own solenoid, while in
others, multiple valves may be operated from the same solenoid. For critical clean
room applications, the solenoid or the pneumatic cylinder is vented to a "dirty"
area to minimize contamination. When the user provides the pneumatic control,
it is necessary to match the solenoid control valve specifications to the vacuum
valve's air supply requirements or operation may be adversely affected.
In the case of metal-sealed valves, manual actuation has advantages. Pneumatic
actuators tend to be large and expensive because of the higher sealing forces
needed. With many metal-sealed valves, it is necessary to reform the seal occa-
sionally. This is done by forcing the soft and hard elements of the seal together with
a force greater than the previously used sealing force. This procedure is easier with
a manual actuator, particularly when a torque wrench is used on the valve actuator.
When motor actuation is used, a screw or a rack converts the motor's rotary mo-
tion to linear motion. In the case of butterfly valves, a gear motor may be coupled
directly to the shaft carrying the vane. An advantage of motor operation is that
only electrical power need be supplied to the valve. A disadvantage can be that in
the event of a power failure, the valve will not go to a known state.
Remotely actuated control valves are often driven by a stepper motor. Together
with the valve controller, geared stepper motors can move the valve mechanism
by very small and precisely regulated
amounts.
Some manually actuated valves can
be used for control, but the ease of control depends greatly on the valve design.
Limit switches are available on most remotely actuated valves. These switches
provide an indication that the valve stem is at one end of its travel or the other and
can be used to tell if a valve has obeyed a command to open or close.