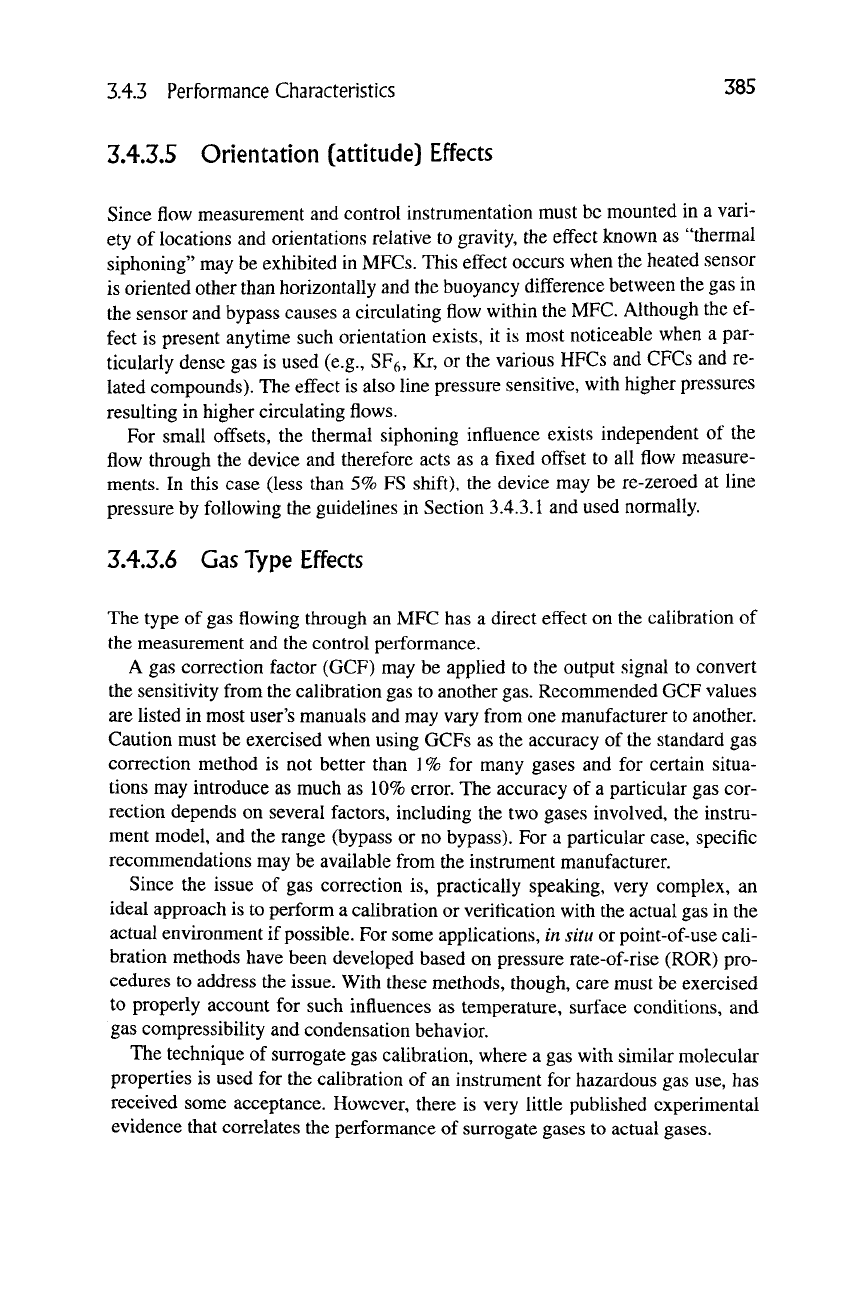
3.4.3 Performance Characteristics
385
3A3.5 Orientation (attitude) Effects
Since flow measurement and control instrumentation must be mounted in a vari-
ety of locations and orientations relative to gravity, the effect known as "thermal
siphoning" may be exhibited in MFCs. This effect occurs when the heated sensor
is oriented other than horizontally and the buoyancy difference between the gas in
the sensor and bypass causes a circulating flow within the MFC. Although the ef-
fect is present anytime such orientation exists, it is most noticeable when a par-
ticularly dense gas is used (e.g., SF6, Kr, or the various MFCs and CFCs and re-
lated compounds). The effect is also line pressure sensitive, with higher pressures
resulting in higher circulating flows.
For small offsets, the thermal siphoning influence exists independent of the
flow through the device and therefore acts as a fixed offset to all flow measure-
ments. In this case (less than 5% FS shift), the device may be re-zeroed at line
pressure by following the guidelines in Section 3.4.3.1 and used normally.
3.4.3.6 Gas Type Effects
The type of gas flowing through an MFC has a direct effect on the calibration of
the measurement and the control performance.
A gas correction factor (GCF) may be applied to the output signal to convert
the sensitivity from the calibration gas to another gas. Recommended GCF values
are listed in most user's manuals and may vary from one manufacturer to another.
Caution must be exercised when using GCFs as the accuracy of the standard gas
correction method is not better than \% for many gases and for certain situa-
tions may introduce as much as 10% error. The accuracy of a particular gas cor-
rection depends on several factors, including the two gases involved, the instru-
ment model, and the range (bypass or no bypass). For a particular case, specific
recommendations may be available from the instrument manufacturer.
Since the issue of gas correction is, practically speaking, very complex, an
ideal approach is to perform a calibration or verification with the actual gas in the
actual environment if
possible.
For some applications, in situ or point-of-use cali-
bration methods have been developed based on pressure rate-of-rise (ROR) pro-
cedures to address the issue. With these methods, though, care must be exercised
to properly account for such influences as temperature, surface conditions, and
gas compressibility and condensation behavior.
The technique of surrogate gas calibration, where a gas with similar molecular
properties is used for the calibration of an instrument for hazardous gas use, has
received some acceptance. However, there is very litde published experimental
evidence that correlates the performance of surrogate gases to actual gases.