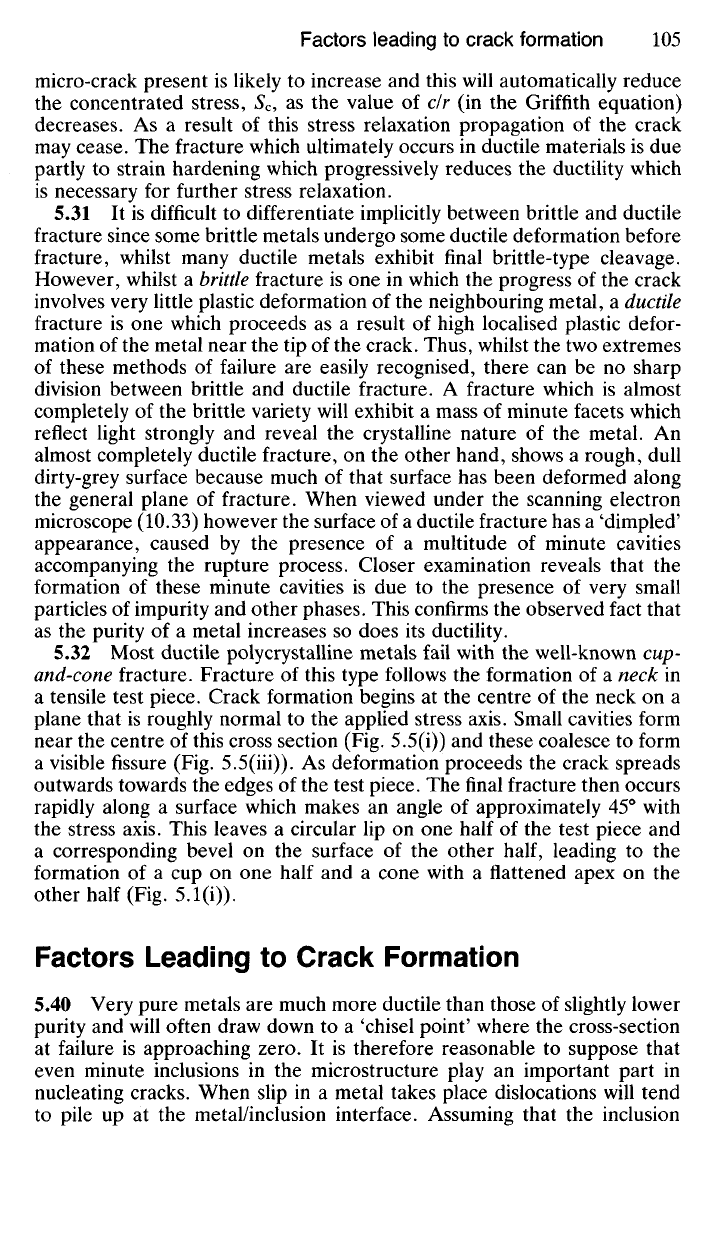
micro-crack present is likely to increase and this will automatically reduce
the concentrated stress, 5
C
, as the value of clr (in the Griffith equation)
decreases. As a result of this stress relaxation propagation of the crack
may cease. The fracture which ultimately occurs in ductile materials is due
partly to strain hardening which progressively reduces the ductility which
is necessary for further stress relaxation.
5.31 It is difficult to differentiate implicitly between brittle and ductile
fracture since some brittle metals undergo some ductile deformation before
fracture, whilst many ductile metals exhibit final brittle-type cleavage.
However, whilst a brittle fracture is one in which the progress of the crack
involves very little plastic deformation of the neighbouring metal, a ductile
fracture is one which proceeds as a result of high localised plastic defor-
mation of the metal near the tip of the crack. Thus, whilst the two extremes
of these methods of failure are easily recognised, there can be no sharp
division between brittle and ductile fracture. A fracture which is almost
completely of the brittle variety will exhibit a mass of minute facets which
reflect light strongly and reveal the crystalline nature of the metal. An
almost completely ductile fracture, on the other hand, shows a rough, dull
dirty-grey surface because much of that surface has been deformed along
the general plane of fracture. When viewed under the scanning electron
microscope (10.33) however the surface of a ductile fracture has a 'dimpled'
appearance, caused by the presence of a multitude of minute cavities
accompanying the rupture process. Closer examination reveals that the
formation of these minute cavities is due to the presence of very small
particles of impurity and other phases. This confirms the observed fact that
as the purity of a metal increases so does its ductility.
5.32 Most ductile polycrystalline metals fail with the well-known cup-
and-cone fracture. Fracture of this type follows the formation of a neck in
a tensile test piece. Crack formation begins at the centre of the neck on a
plane that is roughly normal to the applied stress axis. Small cavities form
near the centre of this cross section (Fig. 5.5(i)) and these coalesce to form
a visible fissure (Fig. 5.5(iii)). As deformation proceeds the crack spreads
outwards towards the edges of the test piece. The final fracture then occurs
rapidly along a surface which makes an angle of approximately 45° with
the stress axis. This leaves a circular lip on one half of the test piece and
a corresponding bevel on the surface of the other
half,
leading to the
formation of a cup on one half and a cone with a flattened apex on the
other half (Fig. 5.1(i)).
Factors Leading to Crack Formation
5.40 Very pure metals are much more ductile than those of slightly lower
purity and will often draw down to a 'chisel point' where the cross-section
at failure is approaching zero. It is therefore reasonable to suppose that
even minute inclusions in the microstructure play an important part in
nucleating cracks. When slip in a metal takes place dislocations will tend
to pile up at the metal/inclusion interface. Assuming that the inclusion