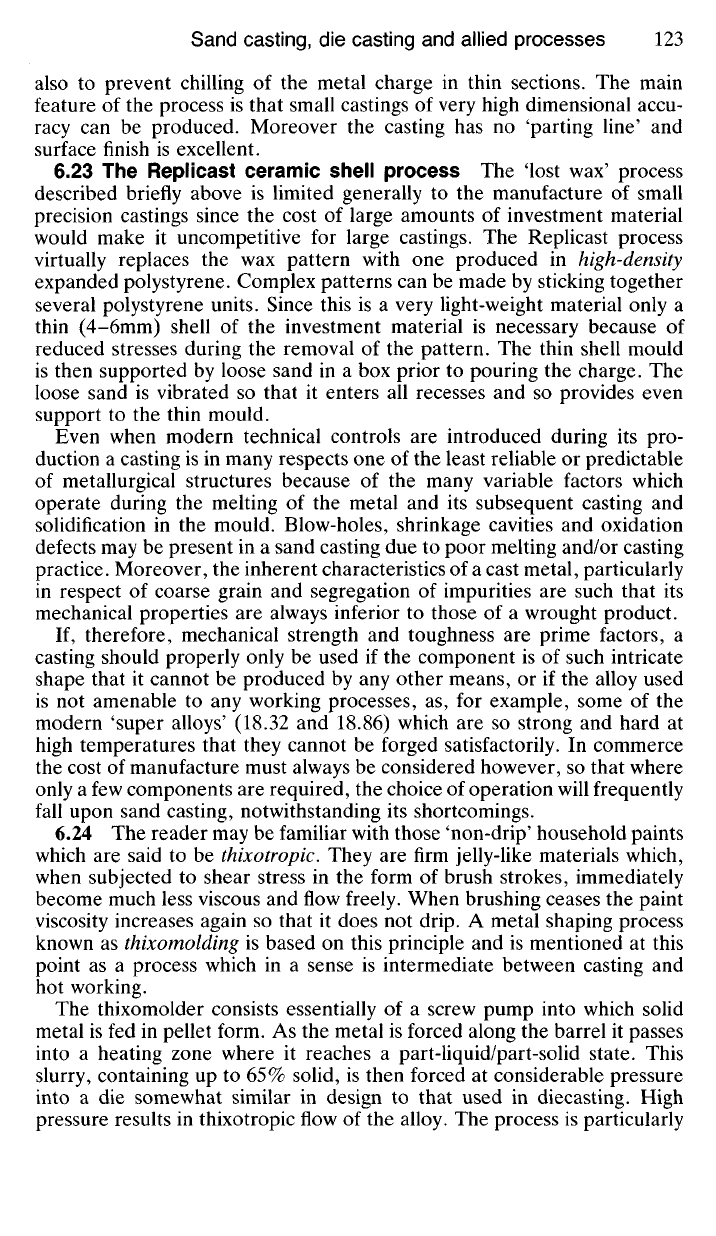
also to prevent chilling of the metal charge in thin sections. The main
feature of the process is that small castings of very high dimensional accu-
racy can be produced. Moreover the casting has no 'parting line' and
surface finish is excellent.
6.23 The Replicast ceramic shell process The lost wax' process
described briefly above is limited generally to the manufacture of small
precision castings since the cost of large amounts of investment material
would make it uncompetitive for large castings. The Replicast process
virtually replaces the wax pattern with one produced in high-density
expanded polystyrene. Complex patterns can be made by sticking together
several polystyrene units. Since this is a very light-weight material only a
thin (4-6mm) shell of the investment material is necessary because of
reduced stresses during the removal of the pattern. The thin shell mould
is then supported by loose sand in a box prior to pouring the charge. The
loose sand is vibrated so that it enters all recesses and so provides even
support to the thin mould.
Even when modern technical controls are introduced during its pro-
duction a casting is in many respects one of the least reliable or predictable
of metallurgical structures because of the many variable factors which
operate during the melting of the metal and its subsequent casting and
solidification in the mould. Blow-holes, shrinkage cavities and oxidation
defects may be present in a sand casting due to poor melting and/or casting
practice. Moreover, the inherent characteristics of a cast metal, particularly
in respect of coarse grain and segregation of impurities are such that its
mechanical properties are always inferior to those of a wrought product.
If, therefore, mechanical strength and toughness are prime factors, a
casting should properly only be used if the component is of such intricate
shape that it cannot be produced by any other means, or if the alloy used
is not amenable to any working processes, as, for example, some of the
modern 'super alloys' (18.32 and 18.86) which are so strong and hard at
high temperatures that they cannot be forged satisfactorily. In commerce
the cost of manufacture must always be considered however, so that where
only a few components are required, the choice of operation will frequently
fall upon sand casting, notwithstanding its shortcomings.
6.24 The reader may be familiar with those 'non-drip' household paints
which are said to be thixotropic. They are firm jelly-like materials which,
when subjected to shear stress in the form of brush strokes, immediately
become much less viscous and flow freely. When brushing ceases the paint
viscosity increases again so that it does not drip. A metal shaping process
known as thixomolding is based on this principle and is mentioned at this
point as a process which in a sense is intermediate between casting and
hot working.
The thixomolder consists essentially of a screw pump into which solid
metal is fed in pellet form. As the metal is forced along the barrel it passes
into a heating zone where it reaches a part-liquid/part-solid state. This
slurry, containing up to 65% solid, is then forced at considerable pressure
into a die somewhat similar in design to that used in diecasting. High
pressure results in thixotropic flow of the alloy. The process is particularly