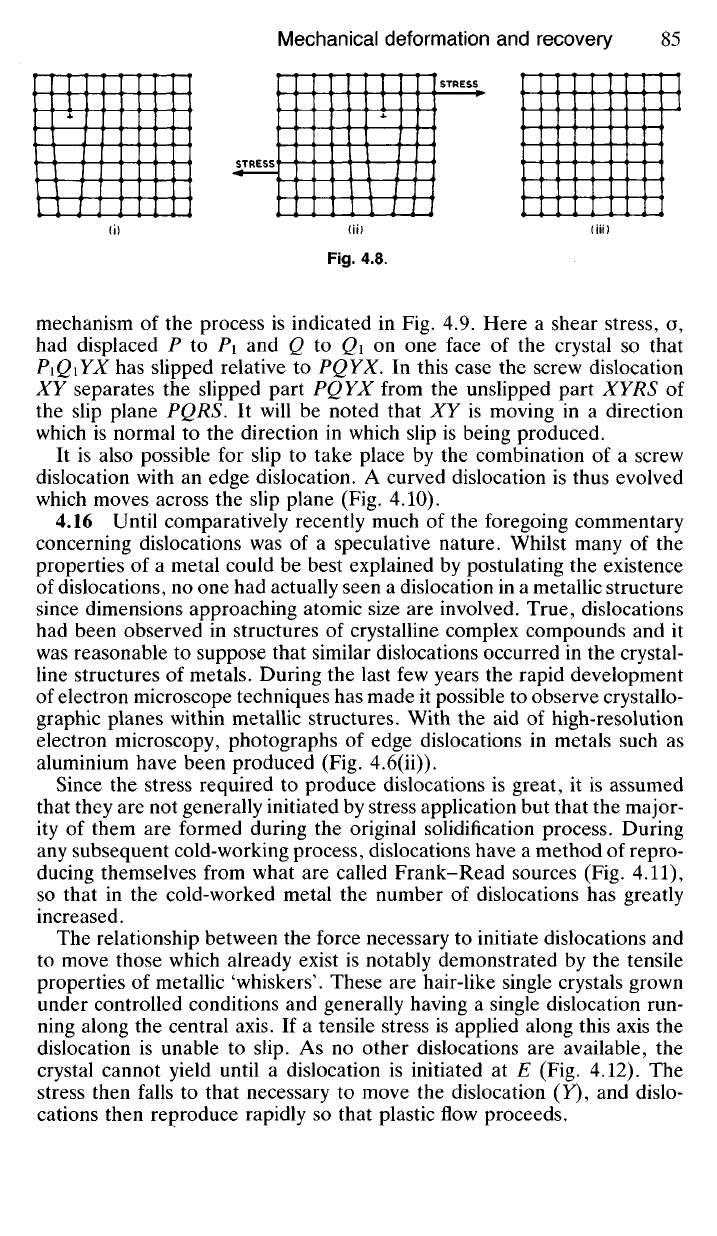
Fig.
4.8.
mechanism of the process is indicated in Fig. 4.9. Here a shear stress, o,
had displaced P to P\ and Q to Qi on one face of the crystal so that
PiQiYX has slipped relative to
PQYX.
In this case the screw dislocation
XY separates the slipped part PQYX from the unslipped part XYRS of
the slip plane PQRS. It will be noted that XY is moving in a direction
which is normal to the direction in which slip is being produced.
It is also possible for slip to take place by the combination of a screw
dislocation with an edge dislocation. A curved dislocation is thus evolved
which moves across the slip plane (Fig. 4.10).
4.16 Until comparatively recently much of the foregoing commentary
concerning dislocations was of a speculative nature. Whilst many of the
properties of a metal could be best explained by postulating the existence
of dislocations, no one had actually seen a dislocation in a metallic structure
since dimensions approaching atomic size are involved. True, dislocations
had been observed in structures of crystalline complex compounds and it
was reasonable to suppose that similar dislocations occurred in the crystal-
line structures of metals. During the last few years the rapid development
of electron microscope techniques has made it possible to observe crystallo-
graphic planes within metallic structures. With the aid of high-resolution
electron microscopy, photographs of edge dislocations in metals such as
aluminium have been produced (Fig. 4.6(ii)).
Since the stress required to produce dislocations is great, it is assumed
that they are not generally initiated by stress application but that the major-
ity of them are formed during the original solidification process. During
any subsequent cold-working process, dislocations have a method of repro-
ducing themselves from what are called Frank-Read sources (Fig. 4.11),
so that in the cold-worked metal the number of dislocations has greatly
increased.
The relationship between the force necessary to initiate dislocations and
to move those which already exist is notably demonstrated by the tensile
properties of metallic 'whiskers'. These are hair-like single crystals grown
under controlled conditions and generally having a single dislocation run-
ning along the central axis. If a tensile stress is applied along this axis the
dislocation is unable to slip. As no other dislocations are available, the
crystal cannot yield until a dislocation is initiated at E (Fig. 4.12). The
stress then falls to that necessary to move the dislocation (Y), and dislo-
cations then reproduce rapidly so that plastic flow proceeds.
STRESS
STRESS