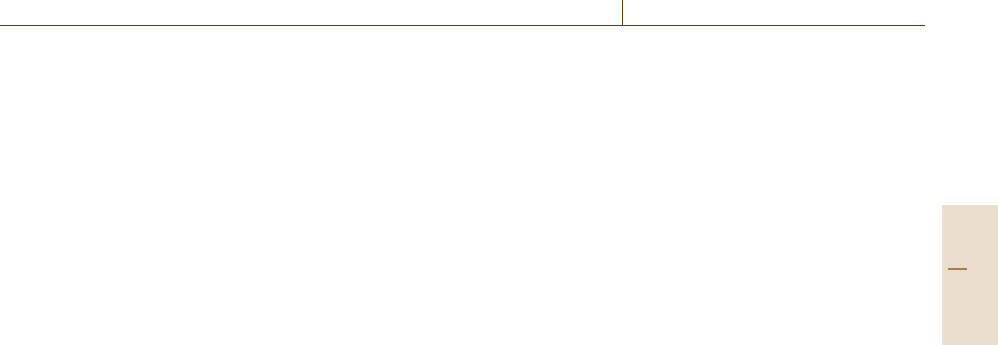
Continuum Constitutive Modeling 18.3 Metallothermomechanical Coupling 1025
where two phases have different free energy levels. This
is due to the characteristics of nondiffusion-type phase
transformation. Combining the stress-induced terms,
the volume of martensite ξ
M
is given by
ξ
M
=1 −exp
φ
1
(M
s
−T ) +φ
2
σ
m
+φ
3
J
1/2
2
.
(18.58)
Here φ
1
, φ
2
and φ
3
are material parameters. The tem-
perature is dominated by the first term while the mean
stress and the deviatoric stress also affect the marten-
site transformation. If a perlite phase ξ
P
exists at the
onset of martensite transformation, the above equation
is modified to
ξ
M
=(1 −ξ
P
)
×
1 −exp
φ
1
(M
s
−T ) +φ
2
σ
m
+φ
3
J
1/2
2
.
(18.59)
This means that only the austenite contributes to the
nucleation of martensite. These are typical kinetics
equations of solid–solid phase transformations. As well
as these equations, one has to consider solid–liquid
transformation when dealing with welding and casting.
In this case, however, one must return to the original
idea that any material parameter is given in an averaged
manner, because the constitutive equation of liquids is
completely different to that of solids, and the shear vis-
cosity is generally much smaller in liquid.
18.3.2 Numerical Methodology
It is important to find an efficient procedure that can be
used to solve the process of thermometallomechanical
coupling in a system. The mechanical equations com-
prise a set of elliptic-type differential equations, while
thermal conduction is governed by a typical diffusion
(parabolic) equation. The kinetics of phase transfor-
mation are also given explicitly. This implies that the
temperature and stress/strain are solved using a finite
element/finite volume method, while the variation in
internal structure can be taken into account using in-
ternal state variables. In order to obtain the numerical
solution step-by-step, a suitable algorithm needs to be
constructed. Using simple estimation of the sensitivity
to each term, it becomes clear that thermal conduction
is generally dominant, and that the time step should be
controlled with reference to the thermal conduction if
the mechanical equation is based on quasi-static mo-
tion. The next greatest influence is the effect of a phase
change on the stress/strain response. Using this, the fol-
lowing numerical scheme can be established.
A schematic of the algorithm is shown in Fig. 18.9
[18.36]. Let Δt be the time increment prescribed on an
object. The temperature is first updated using the solu-
tion for ΔT where ΔT is obtained using only the values
at the current time step t
i
. The time increment Δt is small
enough to obtain a stable solution for the temperature.
Using this temperature increment ΔT , the kinetics are
then updated and the volume fractions Δξ
I
are modified
during the time increment Δt. Since the change in the
volume fraction affects the stress/strain field, the stress
and strain are calculated, with the temperature variation,
last of all. When the mechanical equation is solved for
dynamic motion, substeps with smaller time increments
are superimposed on the time step Δt [18.39]. Although
this iterative process should proceed until the solution is
converges from one time step t
i
to the next t
i+1
, reason-
able solutions can be found even when the calculation
only passes through each step once.
18.3.3 Applications to Heat Treatment
and Metal Forming
Thermometallomechanical coupling simulations have
been applied in the fields of heat treatment, welding,
casting and so on, which have the greatest need for di-
mensional accuracy and to know residual stresses. For
example, when a steel is rapidly cooled from a high-
temperature austenitic state, the structure changes to
martensite below the M
s
transformation state. The vol-
ume increases during this process due to dilatation,
which generally induces compressive stresses. We now
demonstrate a few examples of this from the field of
metal forming.
The austenitic stainless steel type SUS304 has a char-
acteristic feature where the austenite at room temper-
ature is said to be quasi-stable and transformed into
martensite under large inelastic deformation. This im-
plies that the stainless steel shows phase transformation
during the course of forming. Figure 18.10 shows the
volume fraction of the martensite during a stamping pro-
cess [18.39]. A rigid die pushes down from the top of the
object, which generates friction between the die and the
material. The upper figure shows experimental data for
the volume of martensite in % [18.45], while the lower
figure corresponds to simulated results. The distribution
of the martensite structure observed is caused by both the
deformation and the rate of deformation, while the ther-
mal conditions also influence the structural distribution
to some degree. Due to the constraints from the friction
between the die and material, the center of the top of
the material is almost fixed and so less deformation is
Part E 18.3