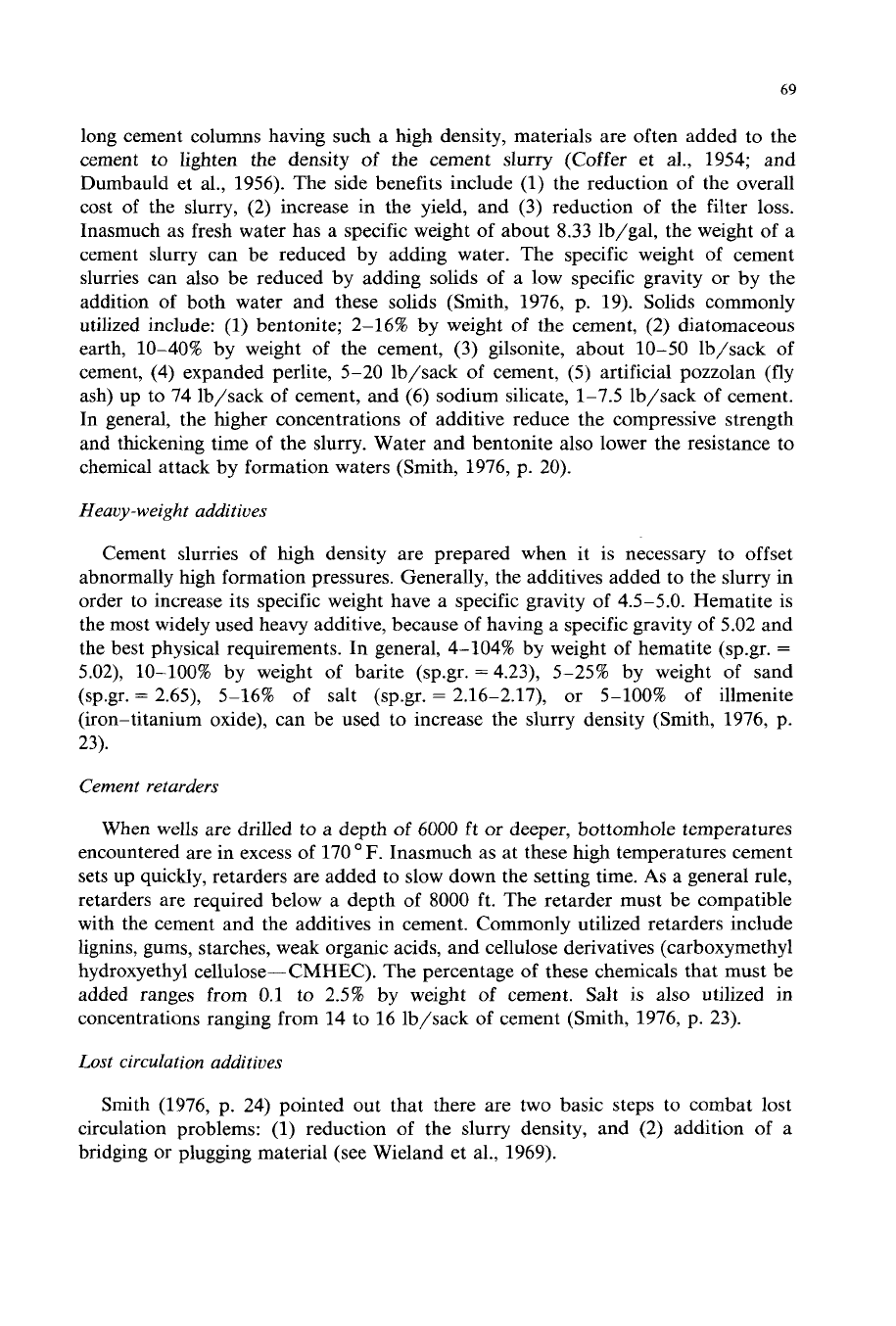
69
long cement columns having such a high density, materials are often added to the
cement
to
lighten the density
of
the cement slurry (Coffer et al., 1954; and
Dumbauld et
al.,
1956). The side benefits include
(1)
the reduction of the overall
cost of the slurry, (2) increase in the yield, and (3) reduction of the filter loss.
Inasmuch as fresh water has a specific weight
of
about 8.33 lb/gal, the weight
of
a
cement slurry can be reduced by adding water. The specific weight of cement
slurries can also be reduced by adding solids
of
a low specific gravity or by the
addition
of
both water and these solids (Smith, 1976, p. 19). Solids commonly
utilized include:
(1)
bentonite; 2-16% by weight of the cement, (2) diatomaceous
earth, 10-40% by weight of the cement,
(3)
gilsonite, about
10-50
lb/sack of
cement,
(4)
expanded perlite,
5-20
lb/sack
of
cement,
(5)
artificial pozzolan (fly
ash) up to 74 lb/sack of cement, and (6) sodium silicate, 1-7.5 lb/sack of cement.
In general, the higher concentrations
of
additive reduce the compressive strength
and thickening time of the slurry. Water and bentonite also lower the resistance to
chemical attack by formation waters (Smith, 1976, p. 20).
Heauy-weight additives
Cement slurries of high density are prepared when it is necessary to offset
abnormally high formation pressures. Generally, the additives added to the slurry in
order to increase its specific weight have a specific gravity
of
4.5-5.0. Hematite is
the most widely used heavy additive, because of having a specific gravity of 5.02 and
the best physical requirements. In general, 4-104% by weight of hematite (sp.gr.
=
5.02),
10-100%
by weight of barite (sp.gr.
=
4.23), 5-25% by weight of sand
(sp.gr.
=
2.65), 5-16% of salt (sp.gr.
=
2.16-2.17), or
5-100%
of illmenite
(iron-titanium oxide), can be used to increase the slurry density (Smith, 1976, p.
23).
Cement retarders
When
wells are drilled to a depth
of
6000 ft or deeper, bottomhole temperatures
encountered are in excess
of
170
O
F.
Inasmuch as at these high temperatures cement
sets up quickly, retarders are added to slow down the setting time.
As
a general rule,
retarders are required below a depth of 8000 ft. The retarder must be compatible
with the cement and the additives in cement. Commonly utilized retarders include
lignins, gums, starches, weak organic acids, and cellulose derivatives (carboxymethyl
hydroxyethyl cellulose-CMHEC). The percentage
of
these chemicals that must be
added ranges from
0.1
to
2.5% by weight
of
cement. Salt
is
also
utilized in
concentrations ranging from 14 to 16 lb/sack of cement (Smith, 1976, p. 23).
Lost circulation additives
Smith (1976, p. 24) pointed out that there are two basic steps to combat lost
circulation problems:
(1)
reduction of the slurry density, and (2) addition
of
a
bridging or plugging material (see Wieland et al., 1969).