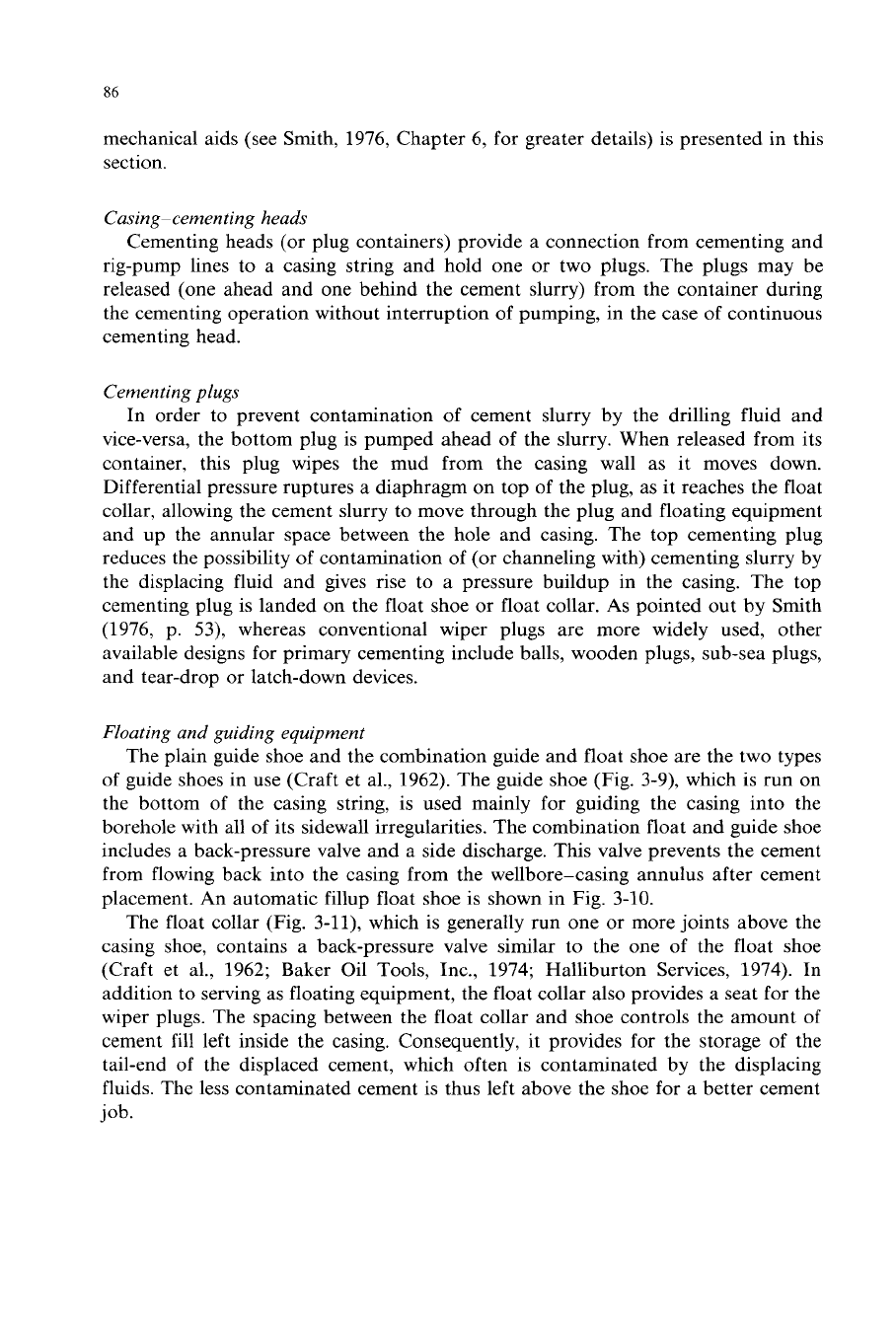
86
mechanical aids (see Smith, 1976, Chapter 6, for greater details) is presented in this
section.
Casing- cemen ting heads
Cementing heads (or plug containers) provide a connection from cementing and
rig-pump lines to a casing string and hold one or two plugs. The plugs may be
released (one ahead and one behind the cement slurry) from the container during
the cementing operation without interruption of pumping, in the case of continuous
cementing head.
Cementing plugs
In order to prevent contamination
of
cement slurry by the drilling fluid and
vice-versa, the bottom plug is pumped ahead of the slurry. When released from its
container, this plug wipes the mud from the casing wall as it moves down.
Differential pressure ruptures a diaphragm on top of the plug, as it reaches the float
collar, allowing the cement slurry to move through the plug and floating equipment
and up the annular space between the hole and casing. The top cementing plug
reduces the possibility
of
contamination of (or channeling with) cementing slurry by
the displacing fluid and gives rise to a pressure buildup in the casing. The top
cementing plug is landed on the float shoe or float collar.
As
pointed out by Smith
(1976, p. 53), whereas conventional wiper plugs are more widely used,
other
available designs for primary cementing include balls, wooden plugs, sub-sea plugs,
and tear-drop
or
latch-down devices.
Floating and guiding equipment
The plain guide shoe and the combination guide and float shoe are the two types
of guide shoes in use (Craft et al., 1962). The guide shoe (Fig. 3-9), which
is
run on
the bottom of the casing string, is used mainly for guiding the casing into the
borehole with all of its sidewall irregularities. The combination float and guide shoe
includes a back-pressure valve and a side discharge. This valve prevents the cement
from flowing back into the casing from the wellbore-casing annulus after cement
placement. An automatic fillup float shoe is shown in Fig. 3-10.
The float collar (Fig. 3-11), which is generally run one or more joints above the
casing shoe, contains a back-pressure valve similar to the one of the float shoe
(Craft et al., 1962; Baker Oil Tools, Inc., 1974; Halliburton Services, 1974). In
addition to serving as floating equipment, the float collar also provides a seat for the
wiper plugs. The spacing between the float collar and shoe controls the amount of
cement fill left inside the casing. Consequently, it provides for the storage of the
tail-end of the displaced cement, which often is contaminated by the displacing
fluids. The less contaminated cement is thus left above the shoe for a better cement
job.