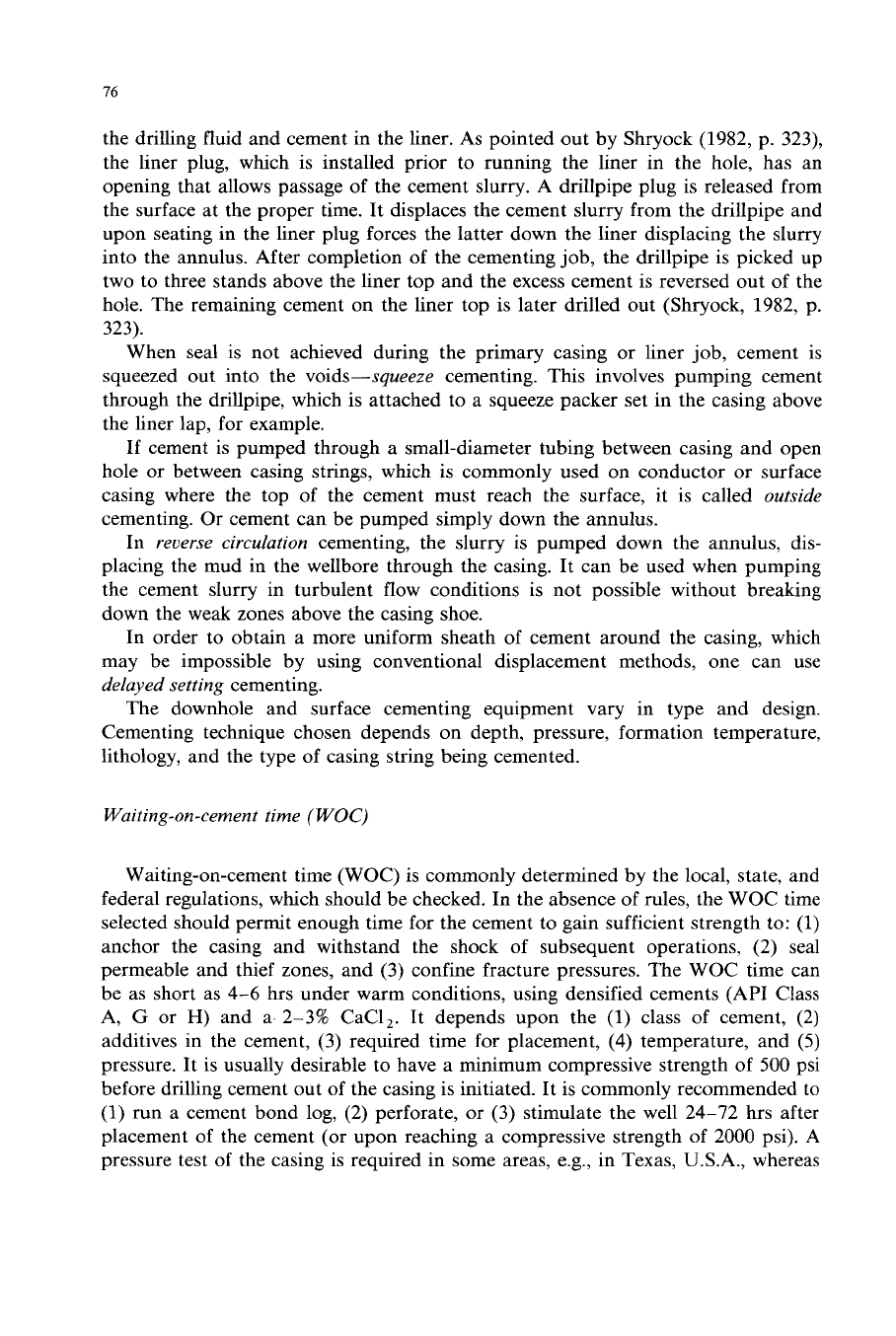
76
the drilling fluid and cement in the liner.
As
pointed out by Shryock (1982, p. 323),
the liner plug, whch is installed prior to running the liner in the hole, has an
opening that allows passage of the cement slurry.
A
drillpipe plug is released from
the surface at the proper time. It displaces the cement slurry from the drillpipe and
upon seating in the liner plug forces the latter down the liner displacing the slurry
into the annulus. After completion of the cementing job, the drillpipe is picked up
two to three stands above the liner top and the excess cement is reversed out
of
the
hole. The remaining cement on the liner top is later drilled out (Shryock, 1982, p.
323).
When seal is not achieved during the primary casing
or
liner job, cement is
squeezed out into the voids-squeeze cementing. This involves pumping cement
through the drillpipe, which is attached to a squeeze packer set in the casing above
the liner lap, for example.
If cement is pumped through a small-diameter tubing between casing and open
hole or between casing strings, which is commonly used on conductor or surface
casing where the top of the cement must reach the surface, it is called outside
cementing. Or cement can be pumped simply down the annulus.
In reverse circulation cementing, the slurry is pumped down the annulus, dis-
placing the mud in the wellbore through the casing. It can be used when pumping
the cement slurry in turbulent flow conditions is not possible without breakmg
down the weak zones above the casing shoe.
In order to obtain a more uniform sheath
of
cement around the casing, whch
may be impossible by using conventional displacement methods, one can use
delayed setting cementing.
The downhole and surface cementing equipment vary in type and design.
Cementing technique chosen depends on depth, pressure, formation temperature,
lithology, and the type of casing string being cemented.
Waiting-on-cement time (WOC)
Waiting-on-cement time (WOC) is commonly determined by the local, state, and
federal regulations, which should be checked. In the absence
of
rules, the WOC time
selected should permit enough time for the cement to gain sufficient strength to: (1)
anchor the casing and withstand the shock of subsequent operations, (2) seal
permeable and thef zones, and (3) confine fracture pressures. The WOC time can
be as short as 4-6 hrs under warm conditions, using densified cements (API Class
A,
G
or
H)
and a 2-3% CaCl,. It depends upon the (1) class of cement,
(2)
additives in the cement,
(3)
required time for placement,
(4)
temperature, and
(5)
pressure. It is usually desirable to have a minimum compressive strength of
500
psi
before drilling cement out of the casing is initiated. It is commonly recommended to
(1) run a cement bond log, (2) perforate, or (3) stimulate the well 24-72 hrs after
placement of the cement (or upon reaching a compressive strength of 2000 psi). A
pressure test of the casing is required in some areas, e.g., in Texas,
U.S.A.,
whereas