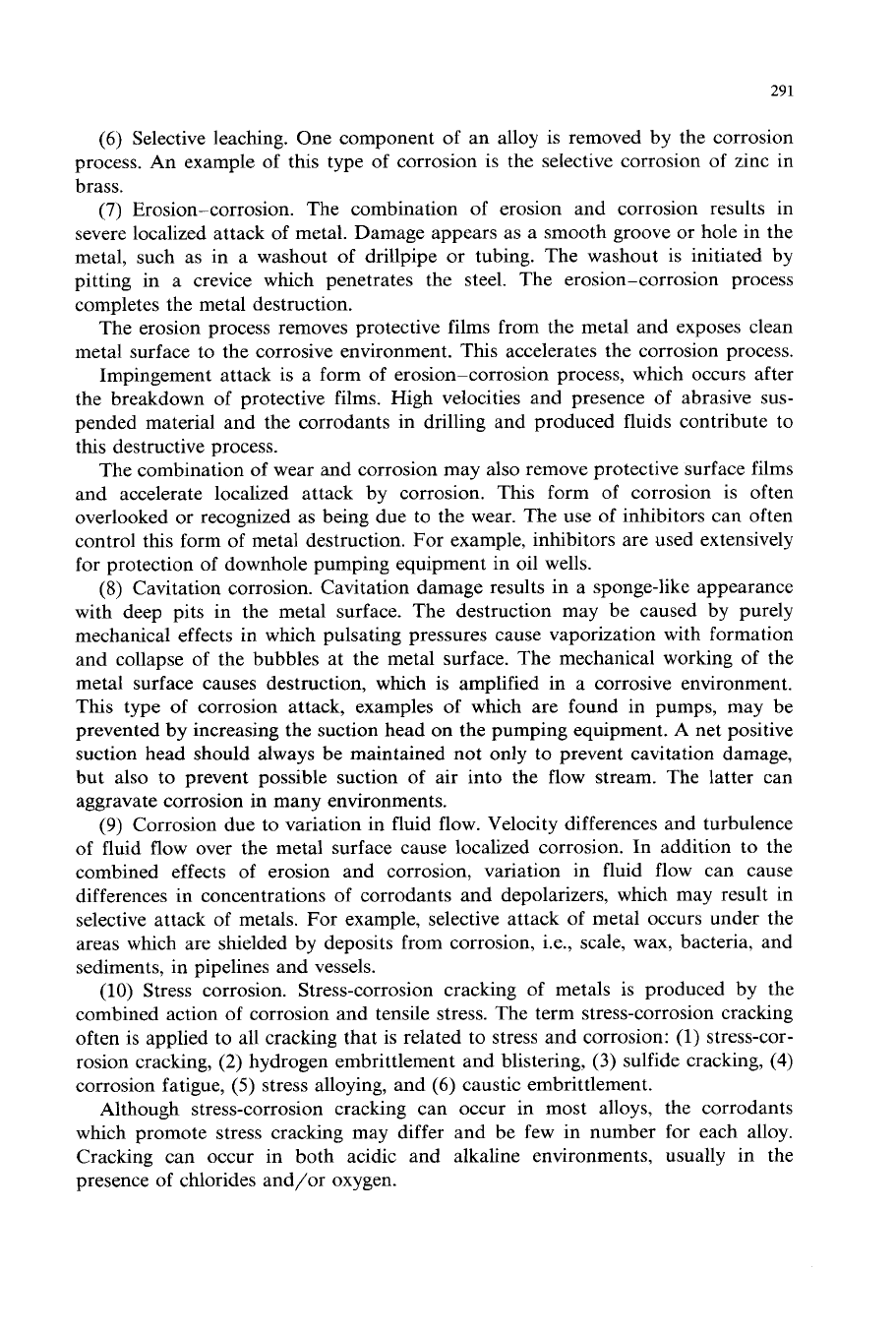
291
(6)
Selective leaching. One component of an alloy is removed by the corrosion
process. An example of this type of corrosion is the selective corrosion of zinc in
brass.
(7)
Erosion-corrosion. The combination of erosion and corrosion results in
severe localized attack of metal. Damage appears as
a
smooth groove or hole in the
metal, such as in a washout
of
drillpipe or tubing. The washout is initiated by
pitting in a crevice which penetrates the steel. The erosion-corrosion process
completes the metal destruction.
The erosion process removes protective films from the metal and exposes clean
metal surface to the corrosive environment. This accelerates the corrosion process.
Impingement attack is a form of erosion-corrosion process, which occurs after
the breakdown
of
protective films. High velocities and presence
of
abrasive
sus-
pended material and the corrodants in drilling and produced fluids contribute to
ths destructive process.
The combination of wear and corrosion may also remove protective surface films
and accelerate localized attack by corrosion. This form
of
corrosion is often
overlooked or recognized as being due to the wear. The use of inhibitors can often
control this form of metal destruction. For example, inhibitors are used extensively
for protection of downhole pumping equipment in oil wells.
(8)
Cavitation corrosion. Cavitation damage results in a sponge-like appearance
with deep pits in the metal surface. The destruction may be caused by purely
mechanical effects in which pulsating pressures cause vaporization with formation
and collapse of the bubbles at the metal surface. The mechanical working
of
the
metal surface causes destruction, which is amplified in a corrosive environment.
This type
of
corrosion attack, examples of which are found in pumps, may be
prevented by increasing the suction head on the pumping equipment. A net positive
suction head should always be maintained not only to prevent cavitation damage,
but also to prevent possible suction
of
air into the flow stream. The latter can
aggravate corrosion in many environments.
(9)
Corrosion due to variation in fluid flow. Velocity differences and turbulence
of fluid flow over the metal surface cause localized corrosion. In addition to the
combined effects of erosion and corrosion, variation in fluid flow can cause
differences in concentrations
of
corrodants and depolarizers, which may result in
selective attack of metals. For example, selective attack of metal occurs under the
areas which are shielded by deposits from corrosion, i.e., scale, wax, bacteria, and
sediments, in pipelines and vessels.
(10)
Stress corrosion. Stress-corrosion cracking of metals is produced by the
combined action of corrosion and tensile stress. The term stress-corrosion cracking
often is applied to all cracking that is related to stress and corrosion:
(1)
stress-cor-
rosion cracking,
(2)
hydrogen embrittlement and blistering,
(3)
sulfide cracking,
(4)
corrosion fatigue,
(5)
stress alloying, and
(6)
caustic embrittlement.
Although stress-corrosion cracking can occur in most alloys, the corrodants
whch promote stress cracking may differ and be few in number for each alloy.
Cracking can occur in both acidic and alkaline environments, usually in the
presence of chlorides and/or oxygen.