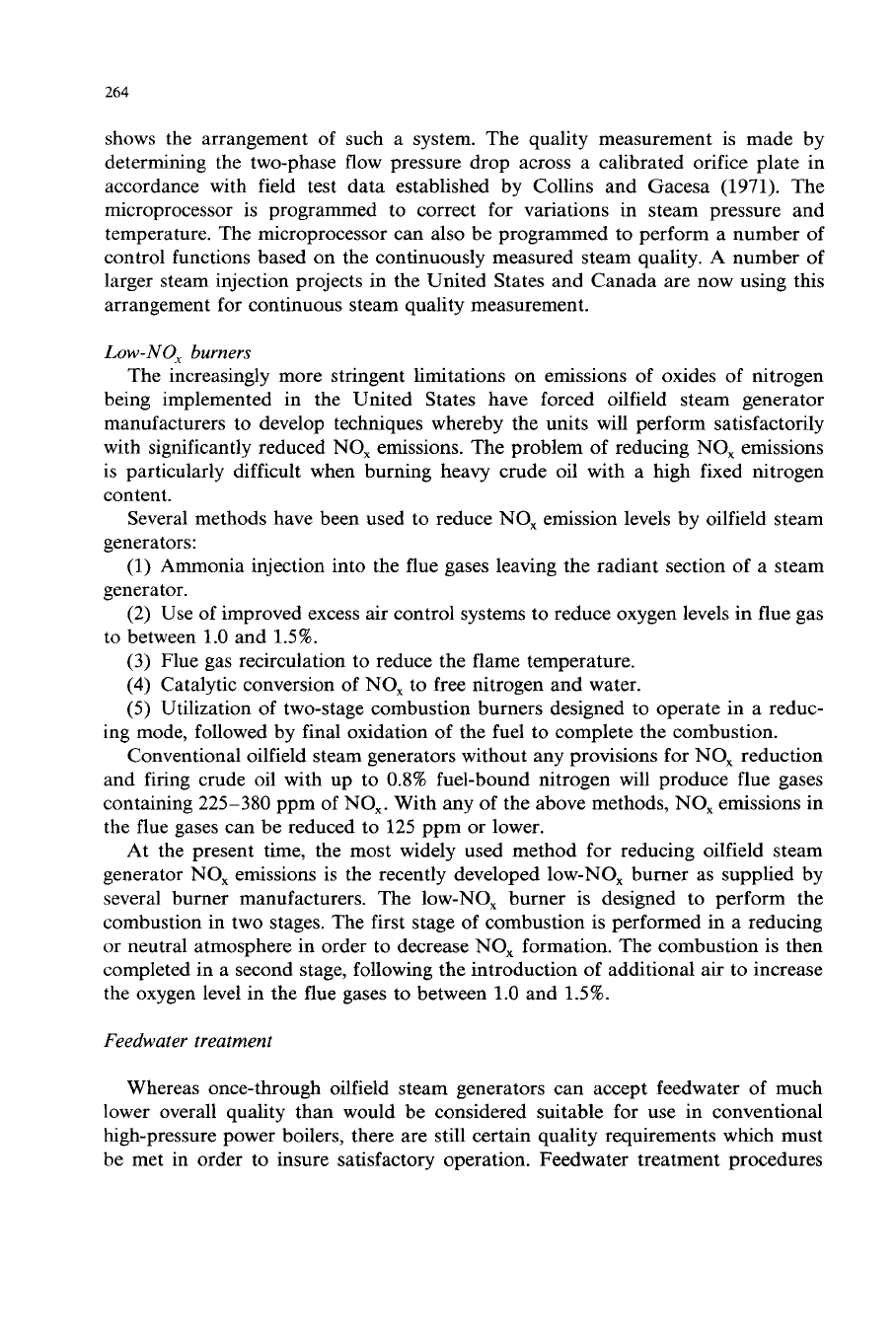
264
shows the arrangement of such a system. The quality measurement is made by
determining the two-phase flow pressure drop across
a
calibrated orifice plate in
accordance with field test data established by Collins and Gacesa (1971). The
microprocessor is programmed to correct for variations in steam pressure and
temperature. The microprocessor can also be programmed to perform a number of
control functions based on the continuously measured steam quality.
A
number of
larger steam injection projects in the United States and Canada are now using this
arrangement for continuous steam quality measurement.
Low
-NO,
burners
The increasingly more stringent limitations on emissions of oxides of nitrogen
being implemented in the United States have forced oilfield steam generator
manufacturers to develop techniques whereby the units will perform satisfactorily
with significantly reduced
NO,
emissions. The problem of reducing NO, emissions
is particularly difficult when burning heavy crude oil with a high fixed nitrogen
content.
Several methods have been used to reduce NO, emission levels by oilfield steam
generators:
(1)
Ammonia injection into the flue gases leaving the radiant section of a steam
generator.
(2) Use of improved excess air control systems to reduce oxygen levels in flue gas
to
between 1.0 and 1.5%.
(3)
Flue gas recirculation to reduce the flame temperature.
(4)
Catalytic conversion of
NO,
to free nitrogen and water.
(5)
Utilization of two-stage combustion burners designed to operate in a reduc-
ing mode, followed by final oxidation of the fuel to complete the combustion.
Conventional oilfield steam generators without any provisions for
NO,
reduction
and firing crude oil with up to 0.8% fuel-bound nitrogen will produce flue gases
containing 225-380 ppm of
NO,.
With any of the above methods, NO, emissions in
the flue gases can be reduced to 125 ppm or lower.
At the present time, the most widely used method for reducing oilfield steam
generator NO, emissions is the recently developed low-NO, burner as supplied by
several burner manufacturers. The low-NO, burner is designed to perform the
combustion in two stages. The first stage of combustion is performed in a reducing
or neutral atmosphere in order to decrease
NO,
formation. The combustion is then
completed in a second stage, following the introduction
of
additional air to increase
the oxygen level in the flue gases to between 1.0 and 1.5%.
Feedwater treatment
Whereas once-through oilfield steam generators can accept feedwater of much
lower overall quality than would be considered suitable for use in conventional
high-pressure power boilers, there are still certain quality requirements which must
be met in order to insure satisfactory operation. Feedwater treatment procedures