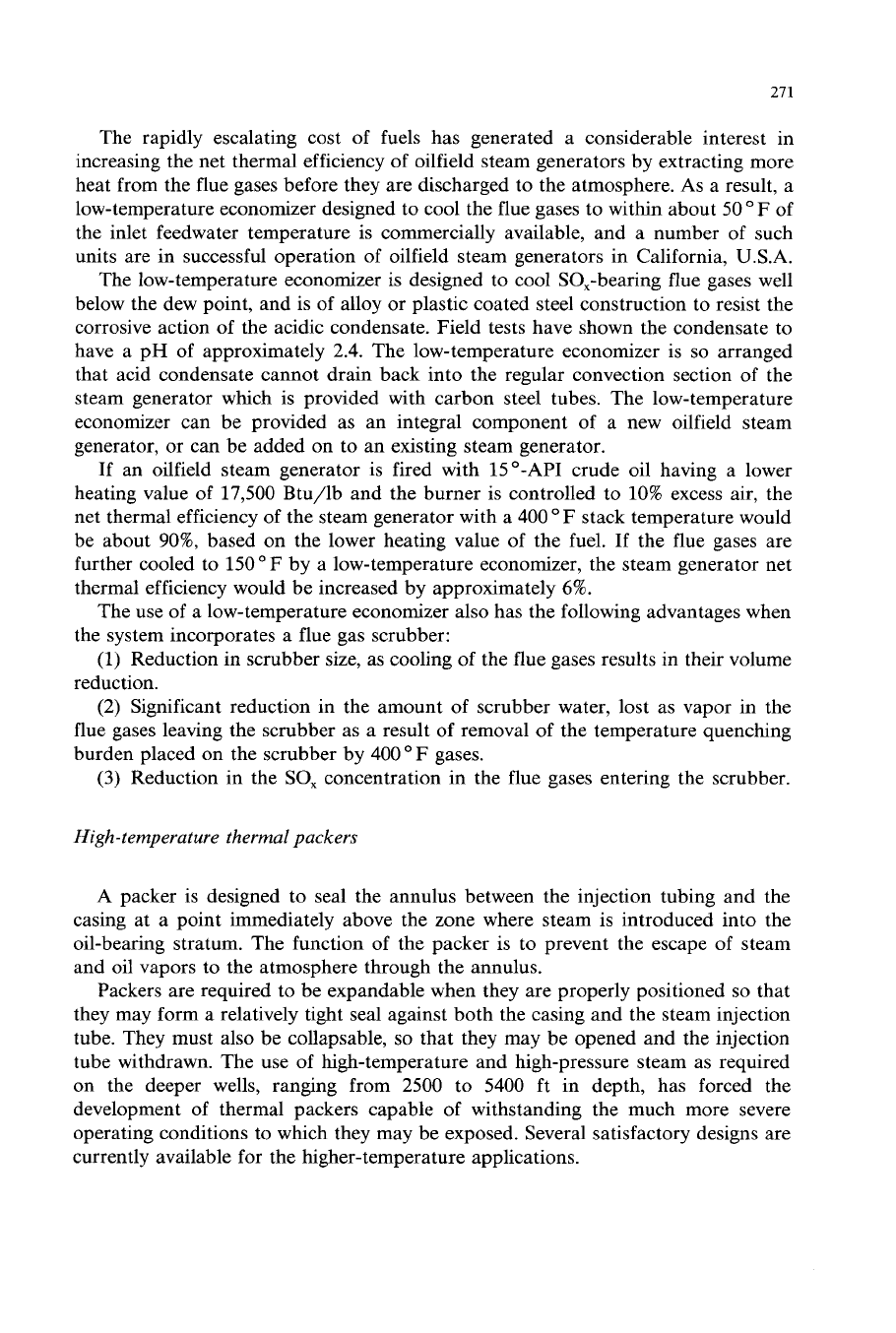
271
The rapidly escalating cost of fuels has generated a considerable interest in
increasing the net thermal efficiency of oilfield steam generators by extracting more
heat from the flue gases before they are discharged to the atmosphere. As a result, a
low-temperature economizer designed to cool the flue gases to within about
50
OF
of
the inlet feedwater temperature is commercially available, and a number of such
units are in successful operation of oilfield steam generators in California, U.S.A.
The low-temperature economizer is designed to cool SOx-bearing flue gases well
below the dew point, and
is
of alloy or plastic coated steel construction to resist the
corrosive action
of
the acidic condensate. Field tests have shown the condensate to
have a pH of approximately
2.4.
The low-temperature economizer is
so
arranged
that acid condensate cannot drain back into the regular convection section
of
the
steam generator which is provided with carbon steel tubes. The low-temperature
economizer can be provided as an integral component
of
a new oilfield steam
generator,
or
can be added on to an existing steam generator.
If an oilfield steam generator is fired with 15O-API crude oil having a lower
heating value of
17,500
Btu/lb and the burner is controlled to
10%
excess air, the
net thermal efficiency of the steam generator with a 400
OF
stack temperature would
be about
9096,
based on the lower heating value of the fuel. If the flue gases are
further cooled to
150
O
F
by a low-temperature economizer, the steam generator net
thermal efficiency would be increased by approximately
6%.
The use of a low-temperature economizer also has the following advantages when
the system incorporates a flue gas scrubber:
(1)
Reduction in scrubber size, as cooling of the flue gases results in their volume
reduction.
(2)
Significant reduction in the amount
of
scrubber water, lost as vapor in the
flue gases leaving the scrubber as a result of removal
of
the temperature quenching
burden placed on the scrubber by
400
O
F
gases.
(3)
Reduction in the SO, concentration in the flue gases entering the scrubber.
High-temperature thermal packers
A packer is designed to seal the annulus between the injection tubing and the
casing at a point immediately above the zone where steam is introduced into the
oil-bearing stratum. The function of the packer is to prevent the escape of steam
and oil vapors to the atmosphere through the annulus.
Packers are required to be expandable when they are properly positioned
so
that
they may form a relatively tight seal against both the casing and the steam injection
tube. They must also be collapsable,
so
that they may be opened and the injection
tube withdrawn. The use
of
high-temperature and high-pressure steam as required
on the deeper wells, ranging from
2500
to
5400
ft in depth, has forced the
development of thermal packers capable of withstanding the much more severe
operating conditions to which they may be exposed. Several satisfactory designs are
currently available for the higher-temperature applications.