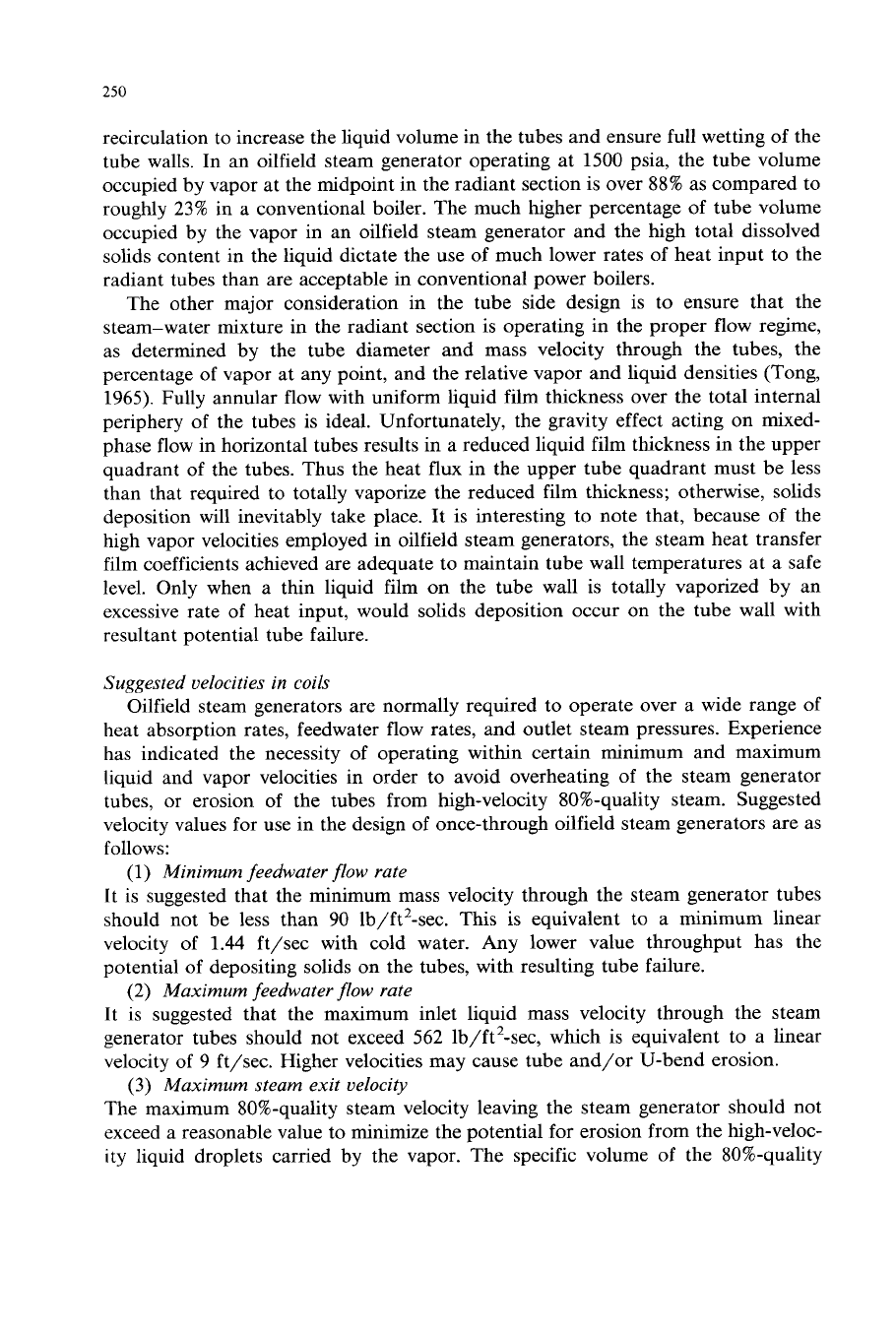
250
recirculation to increase the liquid volume in the tubes and ensure full wetting of the
tube walls. In an oilfield steam generator operating at 1500 psia, the tube volume
occupied by vapor at the midpoint in the radiant section is over
88%
as compared to
roughly 23% in a conventional boiler. The much higher percentage
of
tube volume
occupied by the vapor in an oilfield steam generator and the high total dissolved
solids content in the liquid dictate the use of much lower rates of heat input to the
radiant tubes than are acceptable in conventional power boilers.
The other major consideration in the tube side design is to ensure that the
steam-water mixture in the radiant section is operating in the proper flow regime,
as
determined by the tube diameter and mass velocity through the tubes, the
percentage
of
vapor at any point, and the relative vapor and liquid densities (Tong,
1965). Fully annular flow with uniform liquid film thickness over the total internal
periphery of the tubes is ideal. Unfortunately, the gravity effect acting on mixed-
phase flow in horizontal tubes results in a reduced liquid film thickness in the upper
quadrant of the tubes. Thus the heat flux in the upper tube quadrant must be less
than that required to totally vaporize the reduced film thickness; otherwise, solids
deposition will inevitably take place. It is interesting to note that, because of the
high vapor velocities employed in oilfield steam generators, the steam heat transfer
film coefficients achieved are adequate to maintain tube wall temperatures at a safe
level. Only when a thin liquid film on the tube wall is totally vaporized by an
excessive rate of heat input, would solids deposition occur on the tube wall with
resultant potential tube failure.
Suggested velocities in coils
Oilfield steam generators are normally required to operate over a wide range of
heat absorption rates, feedwater flow rates, and outlet steam pressures. Experience
has indicated the necessity of operating within certain minimum and maximum
liquid and vapor velocities in order to avoid overheating
of
the steam generator
tubes, or erosion of the tubes from high-velocity 80%-quality steam. Suggested
velocity values for use in the design of once-through oilfield steam generators are as
follows:
It is suggested that the minimum mass velocity through the steam generator tubes
should not be less than
90
lb/ft2-sec. This is equivalent to a minimum linear
velocity of 1.44 ft/sec with cold water. Any lower value throughput has the
potential of depositing solids
on
the tubes, with resulting tube failure.
It
is suggested that the maximum inlet liquid mass velocity through the steam
generator tubes should not exceed 562 lb/ft2-sec, which is equivalent to a linear
velocity of 9 ft/sec. Higher velocities may cause tube and/or U-bend erosion.
The maximum 80%-quality steam velocity leaving the steam generator should not
exceed a reasonable value to minimize the potential for erosion from the high-veloc-
ity
liquid droplets carried by the vapor. The specific volume
of
the 80%-quality
(1)
Minimum feedwater flow rate
(2)
Maximum feedwater flow rate
(3)
Maximum steam
exit
velocity