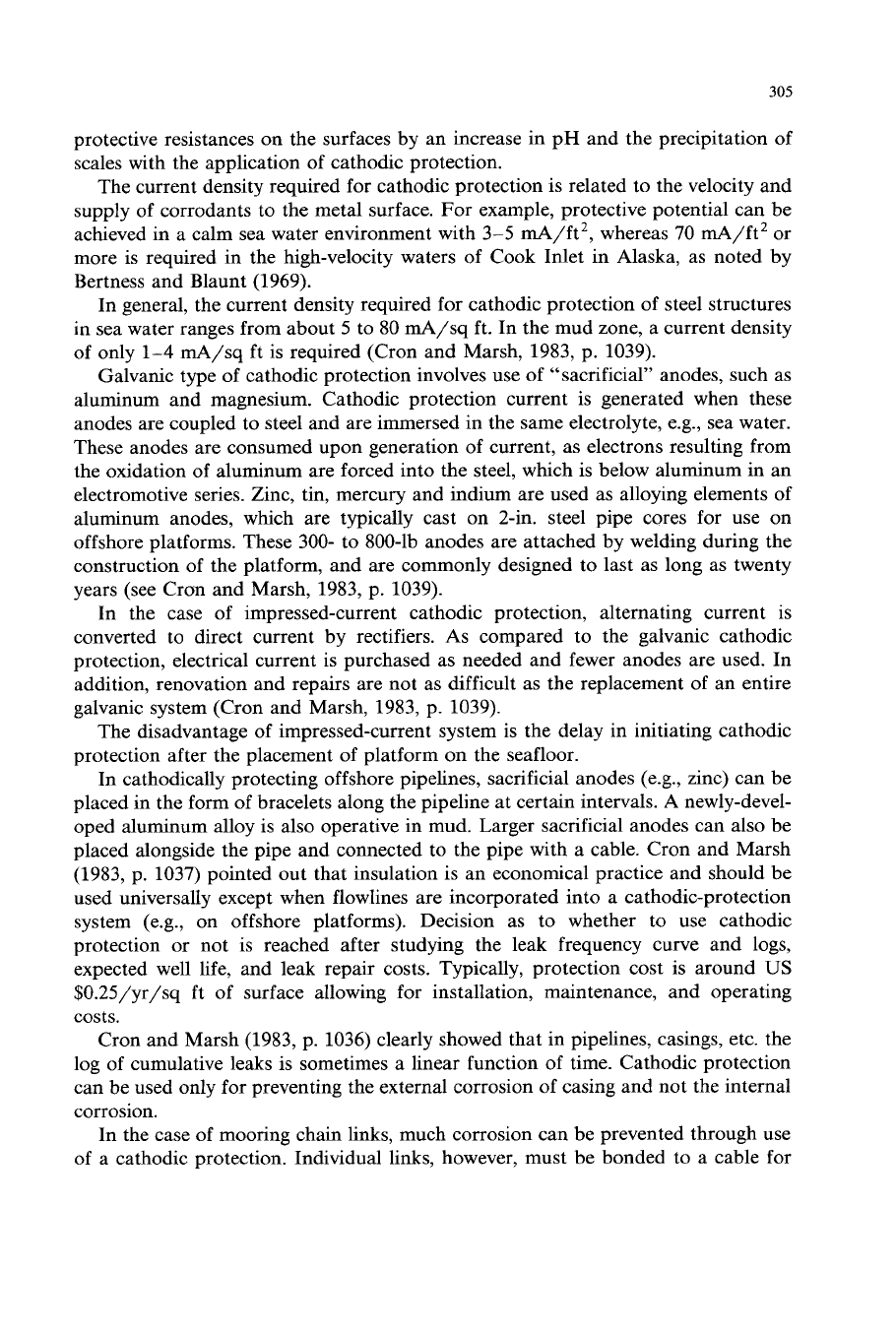
305
protective resistances on the surfaces by an increase in pH and the precipitation of
scales with the application of cathodic protection.
The current density required for cathodic protection is related to the velocity and
supply of corrodants to the metal surface. For example, protective potential can be
achieved in a calm sea water environment with 3-5 mA/ft*, whereas 70 mA/ft2 or
more is required in the high-velocity waters of Cook Inlet in Alaska, as noted by
Bertness and Blaunt (1969).
In general, the current density required for cathodic protection of steel structures
in sea water ranges from about
5
to
80
mA/sq ft. In the mud zone, a current density
of only 1-4 mA/sq
ft
is required (Cron and Marsh, 1983, p. 1039).
Galvanic type of cathodic protection involves use of “sacrificial” anodes, such as
aluminum and magnesium. Cathodic protection current is generated when these
anodes are coupled to steel and are immersed in the same electrolyte, e.g., sea water.
These anodes are consumed upon generation of current, as electrons resulting from
the oxidation of aluminum are forced into the steel, which is below aluminum in an
electromotive series. Zinc, tin, mercury and indium are used as alloying elements of
aluminum anodes, which are typically cast on 2-in. steel pipe cores for use on
offshore platforms. These 300- to 800-lb anodes are attached by welding during the
construction of the platform, and are commonly designed to last as long as twenty
years (see Cron and Marsh, 1983, p. 1039).
In the case of impressed-current cathodic protection, alternating current is
converted to direct current by rectifiers. As compared to the galvanic cathodic
protection, electrical current is purchased as needed and fewer anodes are used. In
addition, renovation and repairs are not as difficult as the replacement of an entire
galvanic system (Cron and Marsh, 1983, p. 1039).
The disadvantage of impressed-current system is the delay in initiating cathodic
protection after the placement of platform on the seafloor.
In cathodically protecting offshore pipelines, sacrificial anodes (e.g., zinc) can be
placed in the form of bracelets along the pipeline at certain intervals. A newly-devel-
oped aluminum alloy is also operative in mud. Larger sacrificial anodes can also be
placed alongside the pipe and connected to the pipe with a cable. Cron and Marsh
(1983,
p. 1037) pointed out that insulation is an economical practice and should be
used universally except when flowlines are incorporated into a cathodic-protection
system (e.g., on offshore platforms). Decision as to whether to use cathodic
protection or not is reached after studying the leak frequency curve and logs,
expected well life, and leak repair costs. Typically, protection cost is around
US
$0.25/yr/sq ft of surface allowing for installation, maintenance, and operating
costs.
Cron and Marsh (1983, p. 1036) clearly showed that in pipelines, casings, etc. the
log of cumulative leaks is sometimes a linear function of time. Cathodic protection
can be used only for preventing the external corrosion of casing and not the internal
corrosion.
In the case of mooring chain links, much corrosion can be prevented through use
of a cathodic protection. Individual links, however, must be bonded to a cable for