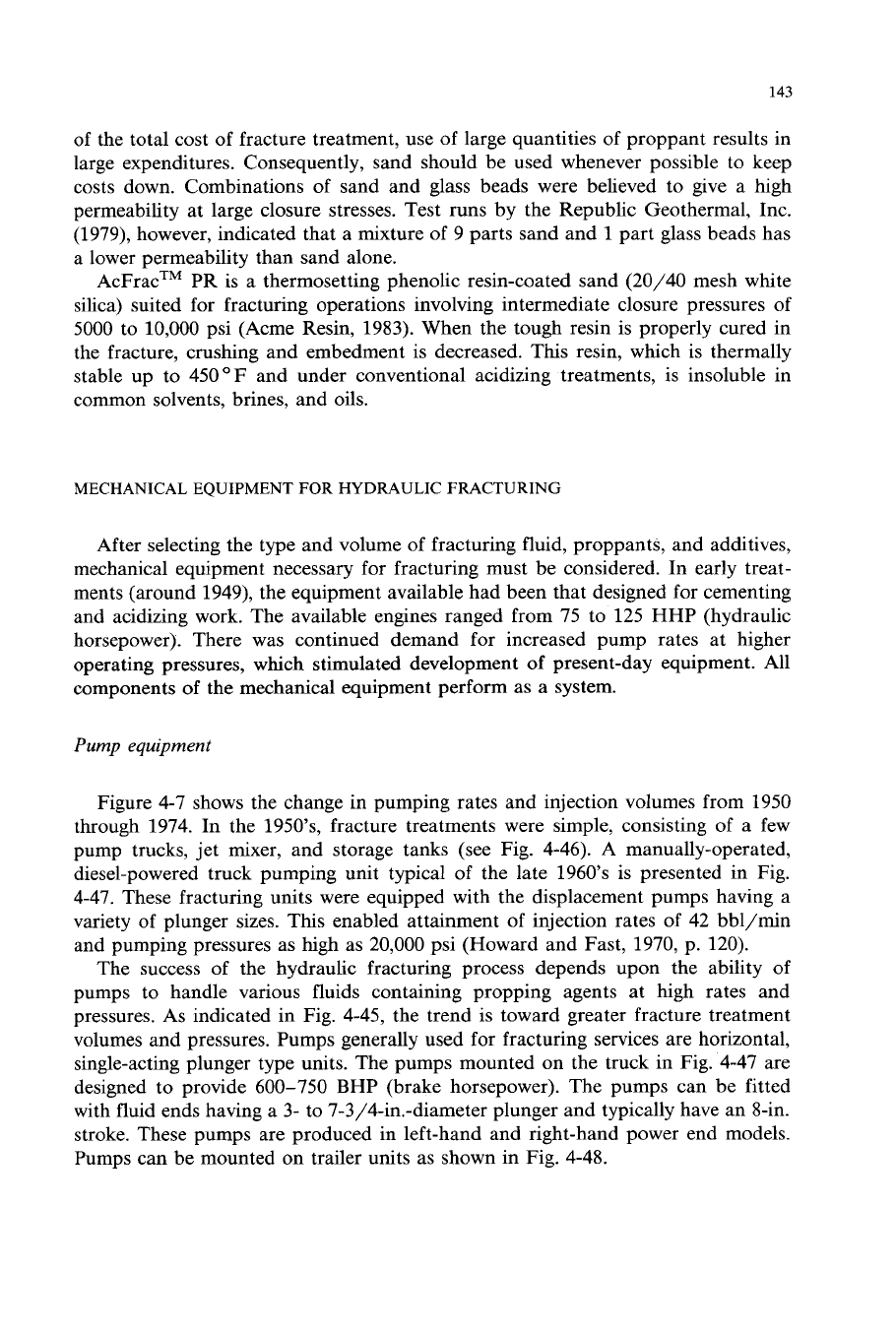
143
of the total cost of fracture treatment, use of large quantities of proppant results in
large expenditures. Consequently, sand should be used whenever possible to keep
costs down. Combinations of sand and glass beads were believed to give a high
permeability at large closure stresses. Test runs by the Republic Geothermal, Inc.
(1979), however, indicated that a mixture of 9 parts sand and
1
part glass beads has
a lower permeability than sand alone.
AcFracTM PR is a thermosetting phenolic resin-coated sand (20/40 mesh white
silica) suited for fracturing operations involving intermediate closure pressures of
5000 to
10,000
psi (Acme Resin, 1983). When the tough resin is properly cured in
the fracture, crushing and embedment is decreased. This resin, which is thermally
stable up to 450
OF
and under conventional acidizing treatments, is insoluble in
common solvents, brines, and oils.
MECHANICAL EQUIPMENT
FOR
HYDRAULIC FRACTURING
After selecting the type and volume of fracturing fluid, proppants, and additives,
mechanical equipment necessary for fracturing must be considered. In early treat-
ments (around 1949), the equipment available had been that designed for cementing
and acidizing work. The available engines ranged from 75 to 125 HHP (hydraulic
horsepower). There was continued demand for increased pump rates at higher
operating pressures, which stimulated development
of
present-day equipment. All
components
of
the mechanical equipment perform as a system.
Pump equipment
Figure 4-7 shows the change in pumping rates and injection volumes from 1950
through 1974. In the 1950’s, fracture treatments were simple, consisting of a few
pump trucks, jet mixer, and storage tanks (see Fig. 4-46). A manually-operated,
diesel-powered truck pumping unit typical of the late 1960’s is presented in Fig.
4-47. These fracturing units were equipped with the displacement pumps having a
variety
of
plunger sizes. This enabled attainment of injection rates of 42 bbl/min
and pumping pressures as high as
20,000
psi (Howard and Fast, 1970, p. 120).
The success of the hydraulic fracturing process depends upon the ability of
pumps to handle various fluids containing propping agents at high rates and
pressures. As indicated in Fig. 4-45, the trend is toward greater fracture treatment
volumes and pressures. Pumps generally used for fracturing services are horizontal,
single-acting plunger type units. The pumps mounted on the truck in Fig. 4-47 are
designed to provide 600-750 BHP (brake horsepower). The pumps can be fitted
with fluid ends having a
3-
to 7-3/4-in.-diameter plunger and typically have an 8-in.
stroke. These pumps are produced in left-hand and right-hand power end models.
Pumps can be mounted on trailer units as shown in Fig. 4-48.