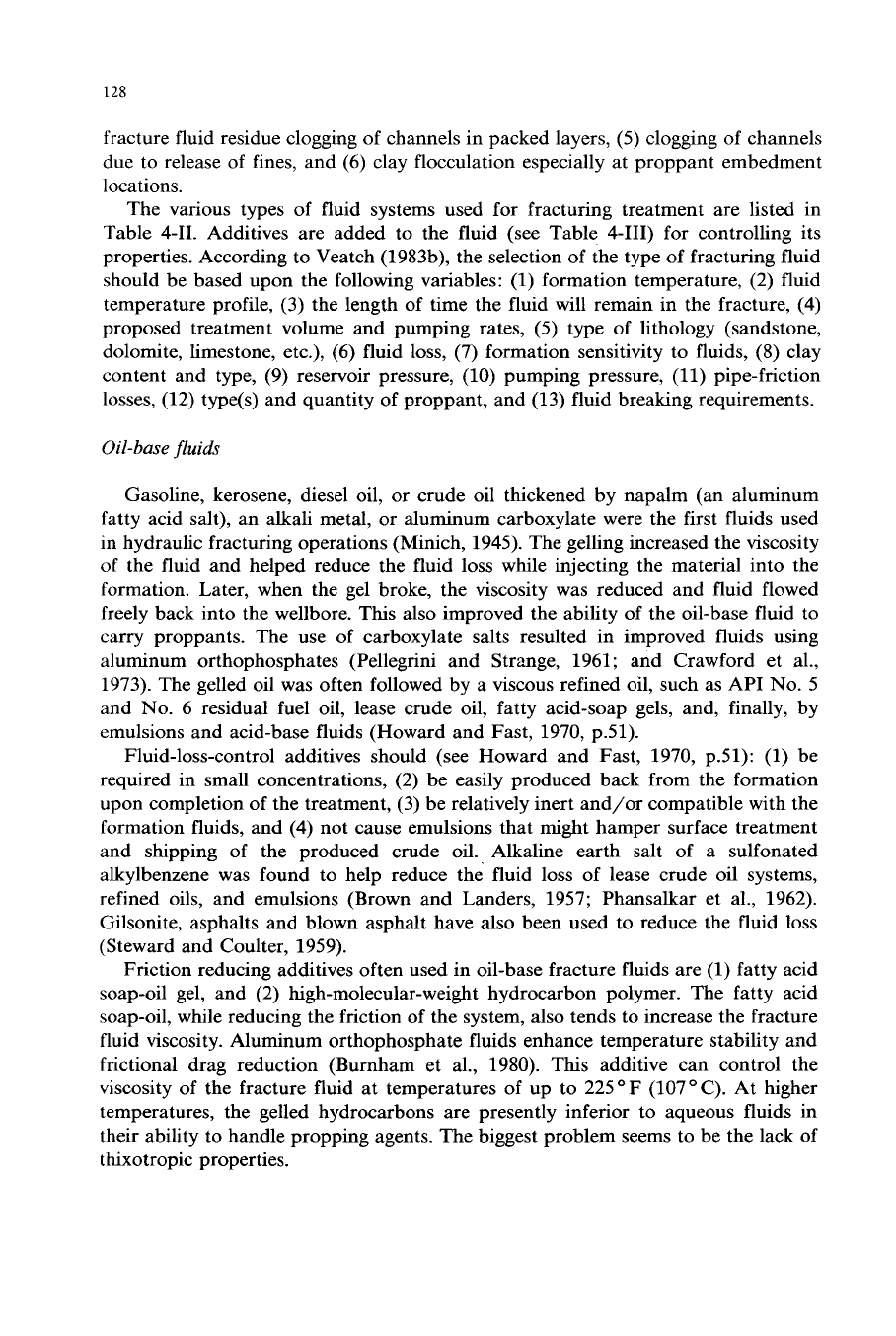
128
fracture fluid residue clogging of channels in packed layers, (5) clogging of channels
due to release of fines, and (6) clay flocculation especially at proppant embedment
locations.
The various types
of
fluid systems used for fracturing treatment are listed in
Table 4-11. Additives are added to the fluid (see Table 4-111) for controlling its
properties. According to Veatch (1983b), the selection of the type of fracturing fluid
should be based upon the following variables:
(1)
formation temperature, (2) fluid
temperature profile, (3) the length of time the fluid will remain in the fracture, (4)
proposed treatment volume and pumping rates, (5) type of lithology (sandstone,
dolomite, limestone, etc.), (6) fluid loss, (7) formation sensitivity to fluids,
(8)
clay
content and type, (9) reservoir pressure,
(10)
pumping pressure, (11) pipe-friction
losses,
(12)
type(s) and quantity of proppant, and
(13)
fluid breaking requirements.
Oil-base
fluids
Gasoline, kerosene, diesel oil, or crude oil thickened by napalm (an aluminum
fatty acid salt), an alkali metal, or aluminum carboxylate were the first fluids used
in hydraulic fracturing operations (Minich, 1945). The gelling increased the viscosity
of the fluid and helped reduce the fluid loss while injecting the material into the
formation. Later, when the gel broke, the viscosity was reduced and fluid flowed
freely back into the wellbore. This also improved the ability of the oil-base fluid to
carry proppants. The use of carboxylate salts resulted in improved fluids using
aluminum orthophosphates (Pellegrini and Strange, 1961; and Crawford et al.,
1973). The gelled oil was often followed by a viscous refined oil, such as API
No.
5
and
No.
6 residual fuel oil, lease crude oil, fatty acid-soap gels, and, finally, by
emulsions and acid-base fluids (Howard and Fast, 1970, p.51).
Fluid-loss-control additives should (see Howard and Fast, 1970,
p.51):
(1)
be
required in small concentrations, (2) be easily produced back from the formation
upon completion of the treatment,
(3)
be relatively inert and/or compatible with the
formation fluids, and (4) not cause emulsions that might hamper surface treatment
and shipping of the produced crude oil. Alkaline earth salt of a sulfonated
alkylbenzene was found to help reduce the. fluid loss of lease crude oil systems,
refined oils, and emulsions (Brown and Landers, 1957; Phansalkar et al., 1962).
Gilsonite, asphalts and blown asphalt have also been used to reduce the fluid loss
(Steward and Coulter, 1959).
Friction reducing additives often used in oil-base fracture fluids are
(1)
fatty acid
soap-oil gel, and (2) high-molecular-weight hydrocarbon polymer. The fatty acid
soap-oil, while reducing the friction of the system, also tends to increase the fracture
fluid viscosity. Aluminum orthophosphate fluids enhance temperature stability and
frictional drag reduction (Burnham et al., 1980). This additive can control the
viscosity of the fracture fluid at temperatures of up to 225
OF
(107
O
C).
At higher
temperatures, the gelled hydrocarbons are presently inferior to aqueous fluids in
their ability to handle propping agents. The biggest problem seems to be the lack of
thixotropic properties.