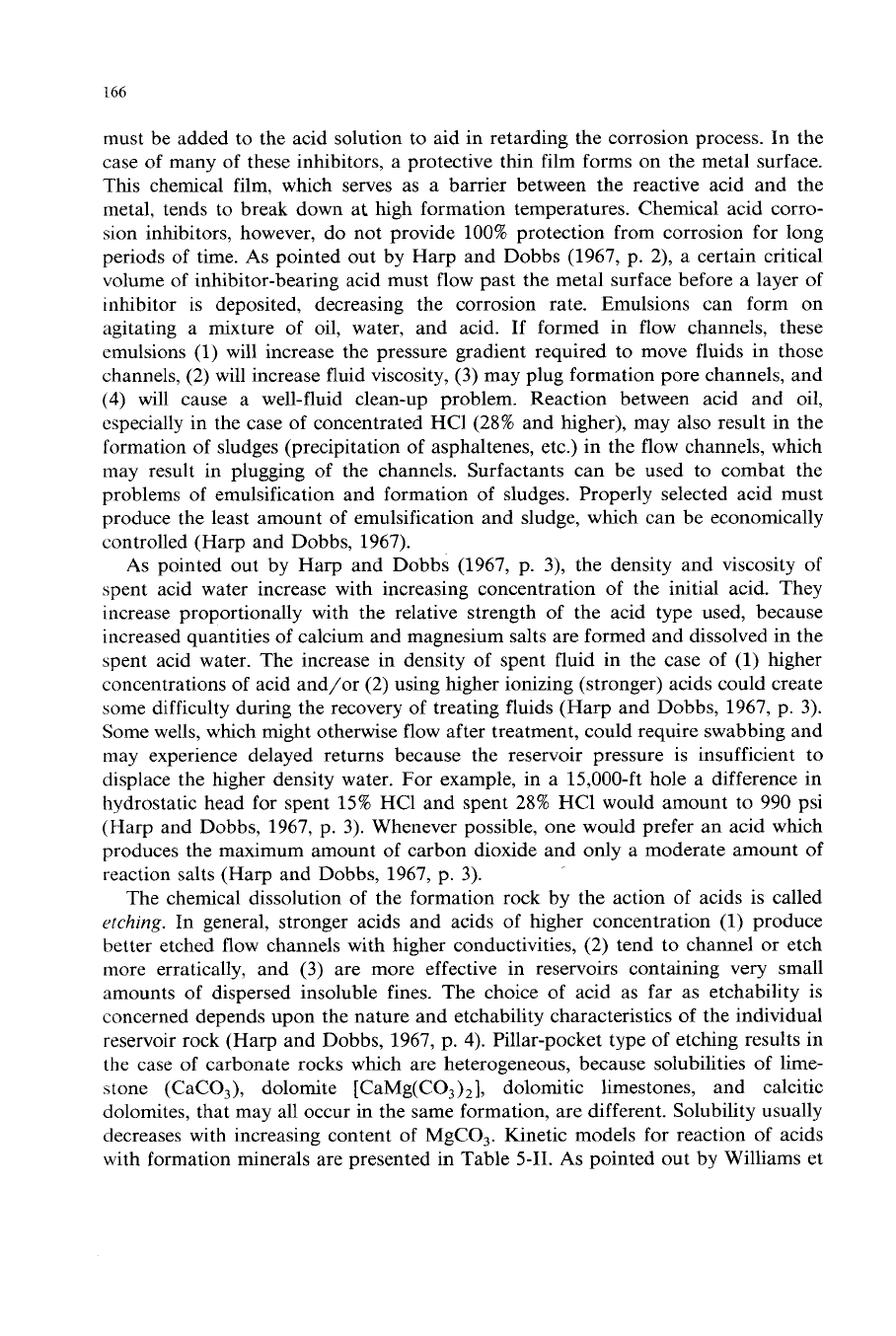
166
must be added to the acid solution to aid in retarding the corrosion process. In the
case
of
many of these inhibitors, a protective thin film forms on the metal surface.
This chemical film, which serves as a barrier between the reactive acid and the
metal, tends to break down at high formation temperatures. Chemical acid corro-
sion inhibitors, however, do not provide
100%
protection from corrosion for long
periods of time.
As
pointed out by Harp and Dobbs (1967, p.
2),
a certain critical
volume of inhibitor-bearing acid must flow past the metal surface before a layer
of
inhibitor is deposited, decreasing the corrosion rate. Emulsions can form on
agitating a mixture of oil, water, and acid. If formed in flow channels, these
emulsions (1) will increase the pressure gradient required to move fluids in those
channels,
(2)
will increase fluid viscosity,
(3)
may plug formation pore channels, and
(4)
will cause a well-fluid clean-up problem. Reaction between acid and oil,
especially in the case of concentrated HCI
(28%
and higher), may also result in the
formation of sludges (precipitation of asphaltenes, etc.) in the flow channels, which
may result in plugging of the channels. Surfactants can be used to combat the
problems
of
emulsification and formation
of
sludges. Properly selected acid must
produce the least amount of emulsification and sludge, which can be economically
controlled (Harp and Dobbs, 1967).
As
pointed out by Harp and Dobbs (1967, p.
3),
the density and viscosity
of
spent acid water increase with increasing concentration of the initial acid. They
increase proportionally with the relative strength of the acid type used, because
increased quantities of calcium and magnesium salts are formed and dissolved in the
spent acid water. The increase in density of spent fluid in the case of
(1)
higher
concentrations of acid and/or
(2)
using higher ionizing (stronger) acids could create
some difficulty during the recovery of treating fluids (Harp and Dobbs, 1967, p.
3).
Some wells, which might otherwise flow after treatment, could require swabbing and
may experience delayed returns because the reservoir pressure is insufficient to
displace the higher density water.
For
example, in a 15,000-ft hole a difference in
hydrostatic head for spent
15%
HC1 and spent
28%
HC1 would amount to 990 psi
(Harp and Dobbs, 1967, p.
3).
Whenever possible, one would prefer an acid which
produces the maximum amount of carbon dioxide and only a moderate amount of
reaction salts (Harp and Dobbs, 1967, p.
3).
The chemical dissolution of the formation rock by the action of acids is called
etching.
In general, stronger acids and acids of higher concentration (1) produce
better etched flow channels with higher conductivities,
(2)
tend to channel or etch
more erratically, and
(3)
are more effective in reservoirs containing very small
amounts of dispersed insoluble fines. The choice of acid as far as etchability is
concerned depends upon the nature and etchability characteristics
of
the individual
reservoir rock (Harp and Dobbs, 1967, p.
4).
Pillar-pocket type of etchng results in
the case of carbonate rocks which are heterogeneous, because solubilities of lime-
stone (CaCO,), dolomite [CaMg(CO,),], dolomitic limestones, and calcitic
dolomites, that may all occur in the same formation, are different. Solubility usually
decreases with increasing content of MgCO,. Kinetic models for reaction of acids
with formation minerals are presented in Table 5-11.
As
pointed out by Williams et