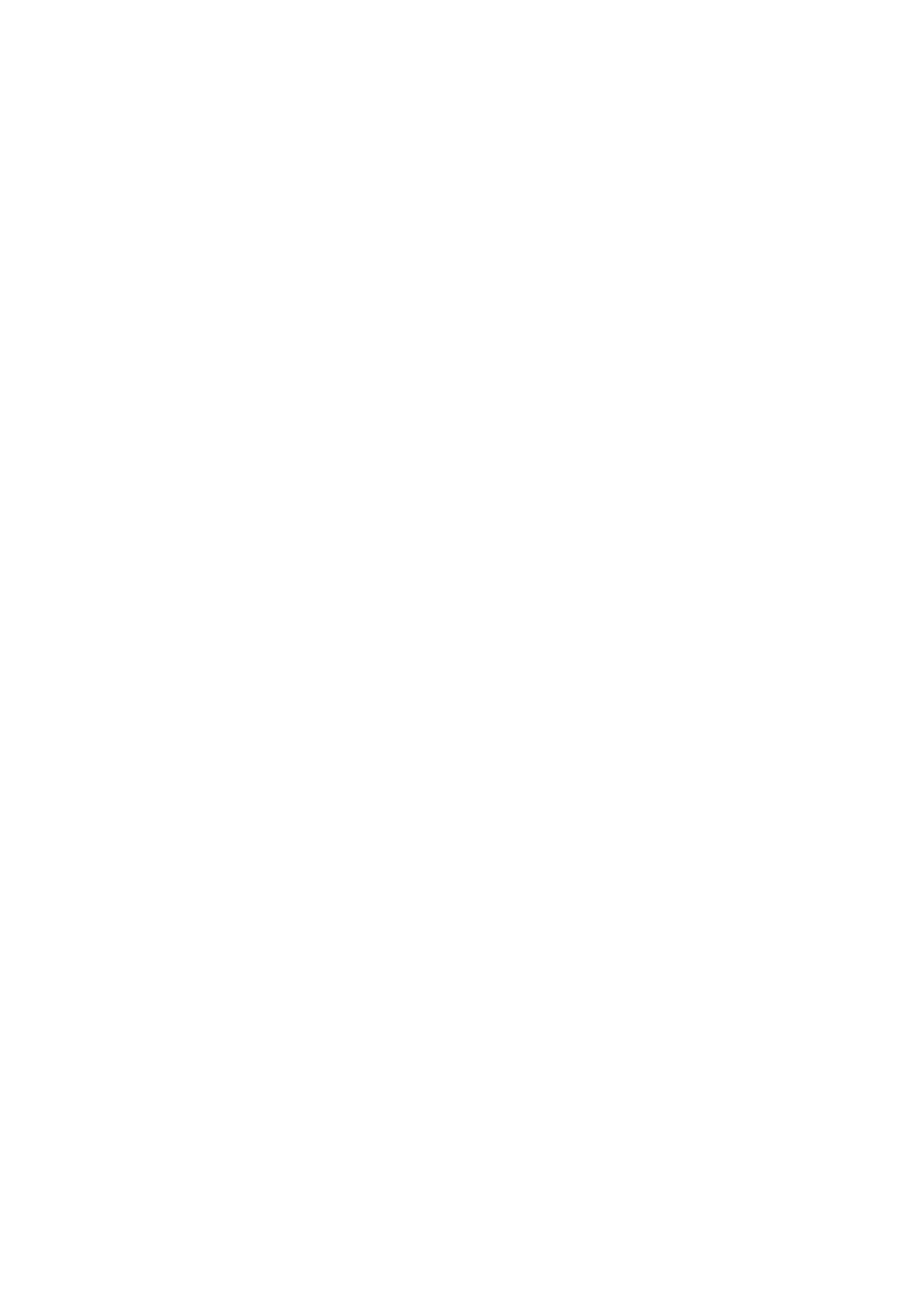
899
выпуске крупных автономных кондиционеров для различных типов зданий. В 1987 году производство этой
продукции было перенесено в Мэйкон с другой фабрики. В 1988 году структура фабрики в Мэйконе была
сформирована как сбалансированная сборочная линия для производства кондиционеров. Эта фабрика
работает восемь часов в день пять дней в неделю. Штат составляют 150 рабочих, из которых 90 человек
заняты непосредственно производством. Все постоянные служащие предприятия получают заработную
плату. Временные работники нанимаются на определенный период через местное агентство по
трудоустройству. Количество временных рабочих варьируется от 0 до 25% размера постоянного штата в
зависимости от нормы выработки. На момент написания этих строк около 20% от 90 производственных
рабочих работали на временной основе. Объем продаж фабрики за 1990 год составил около 25 миллионов
долларов и по критериям общепринятых стандартов бухгалтерского учета предприятие было признано
рентабельным.
Система производственного планирования и контроля, используемая на мэйконской фабрике,
представляет собой комбинацию систем планирования материальных потребностей (MRP), "точно в срок"
(JIT) и теории ограничений (ТОС, см. табл. 20. 2). Система MRP была приобретена компанией в 1989 году.
Пакет программного обеспечения CONTROL разработан фирмой Cincom, Inc. Решение приобрести именно
это обеспечение было обосновано заключением фабричного специалиста, который провел исследования
нескольких разных систем MRP. Данная система MRP включает в себя ряд общих модулей, объединенных
отлаженными интерфейсами. В настоящее время на фабрике используется основной модуль
производственного планирования, модуль вычислений MRP, модуль бухгалтерского учета и модуль
накладных на материалы. В 1989 году была также выбрана и реализована отдельная закупочная система.
Модуль цехового контроля, прилагаемый к программе CONTROL, не реализован. Решение не внедрять
этот модуль на фабрике основано на желании полнее использовать методы ТОС и JIТ. Управленческий
персонал был убежден, что система MRP обеспечит необходимую основу для применения этих двух
методов.
В 1988 году компания наняла независимого консультанта, чтобы с применением методов JIТ
улучшить некоторые аспекты производственного процесса. На фабрике используется сбалансированный
основной план производства, линейное производственное планирование, профилактическое плановое
техническое обслуживание и ремонт, многопрофильный персонал и пересматривается планировка
производственных помещений, что должно способствовать внедрению методов JIТ. Для доставки
сборочных узлов на участки окончательной сборки используются также элементы системы "канбан".
Поставщики тоже применяют такие методы для пополнения материально-технических запасов и
закупаемых фабрикой готовых деталей. Весь персонал фабрики разбит на пять рабочих групп, которые
называются ячейками, все руководители этих ячеек прошли специальную подготовку по использованию
методов JIТ. Производственные решения, такие, например, как составление графиков сверхурочной
работы, принимаются по результатам общего обсуждения в ячейках.
В 1989 году на фабрике были внедрены методы ТОС. В ходе принятия внутренних управленческих
решений применяются такие критерии эффективности, как выручка, товарно-материальные запасы и
эксплуатационные расходы. Работа цехов контролируется с использованием таких методов, как "барабан-
амортизатор—веревка" и управление резервами. Управленческий персонал прошел специальную
подготовку по применению методов ТОС и лежащих в основе этого подхода критериев эффективности.
Программное обеспечение ОРТ на фабрике не применяется. "Узкое место" процесса идентифицировано, в
результате чего после этой операции созданы "ограничительный" и "пространственный" резервы.
Управление товарно-материальными запасами входит в общую компетенцию руководителей ячеек и
рабочих-специалистов. Время производства составляет от двух до пяти дней. Сырье составляет 70% общих
товарно-материальных запасов, а показатель его оборачиваемости около шести раз в год. Запасы
незавершенного производства составляют 10% общей суммы инвестиций в товарно-материальные запасы,
их оборачиваемость — 100 раз в год. Готовая продукция составляет 20% общих запасов и ее
оборачиваемость — около 10 раз в год. На 1992 год управленческий персонал фабрики наметил цель
повысить оборачиваемость сырья до 12 раз, незавершенного производства — до 250, а готовой продукции
— до 15 раз в год. Сразу после ввода сбалансированной сборочной линии на фабрике использовалась
система "канбан" и производилось в среднем по три кондиционера в день. После внедрения таких методов,
как "барабан-амортизатор—веревка" и управление резервами, мощность сборочной линии при тех же
людских ресурсах выросла до шести единиц продукции в день. Управленческий персонал склонен
приписывать заслуги такого повышения производительности внедрению принципов теории ограничений и
считает, что столь значительное сокращение времени производства очень сильно способствует повышению
конкурентоспособности ассортимента продукции компании на рынке.
Освоение новой продукции
В 1991 году перед The Тrапе встала необходимость принять решение относительно вывода на рынок
двух новых видов продукции — блока для очистки хладагента с приблизительными размерами 1, 5x1, 2x1