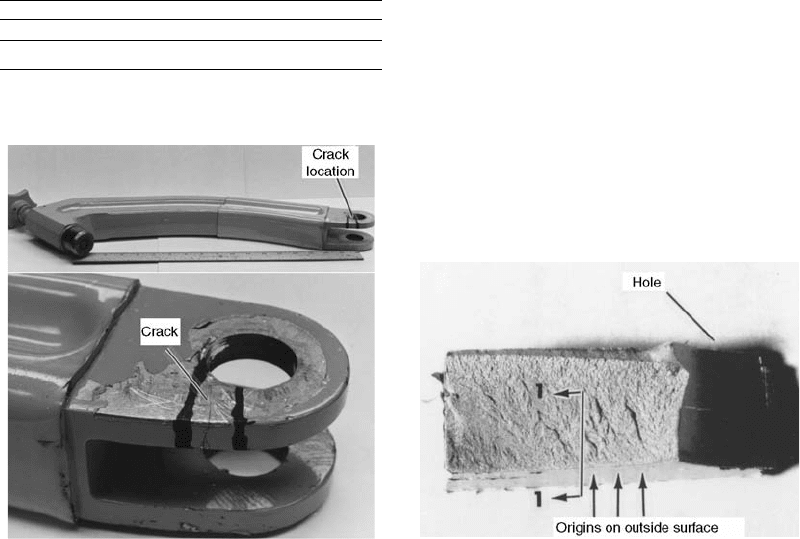
An SEM was used to examine the fracture
surface and the side of the clevis at the origin.
Figure 44 shows SEM photographs document-
ing topographic features of the fracture surface
and corrosion pitting on the side of the clevis
at the fracture origin. The pits were coated with
primer, which indicated they were present
prior to painting. Also documented in Fig. 44
are intergranular topography and corrosion pro-
ducts at the fracture origins. These features are
all characteristic of a stress-corrosion failure
(Ref 4).
A laboratory overload fracture produced in
the clevis was examined in the SEM. Figure 45
shows an SEM fractograph documenting dim-
ples that are characteristic of an overload mode
of failure.
Hardness measurements were made on the
adapter to verify the heat treat condition. The
hardness of the adapter was 41.4 HRC, and this
met the hardness requirement of 40 to 43 HRC.
The hydrogen content of the adapter was
determined to be 1 ppm, which is considered
low in relation to producing a hydrogen em-
brittlement failure.
A metallographic specimen was prepared
through a fracture origin. The specimen was
prepared using standard metallographic techni-
ques. Figure 46 shows the microstructure, which
was normal (tempered martensite).
Also shown in Fig. 46 is a corrosion pit that
was coated with paint, indicating the pit was
present prior to painting.
Based on the results of this investigation,
it was concluded that the adapter failed due to
stress-corrosion cracking. Corrosion pits at the
fracture origin were present prior to painting.
Failure Analysis of an Aircraft Hoist
Sling during Static Test
An aircraft hoist sling was successfully tested
to an ultimate load of 136,000 kg (300,000 lb).
However, shortly after relieving the load,
the weld on the aft right-hand fitting failed.
The fitting was fabricated from welded 17-4PH
stainless steel plates.
Figure 47 shows the as-received failed portion
of the test fixture. The failure occurred in a
consumable electrode weld that traversed
around the length of the fracture, which was
approximately 69 cm (27 in.). A dark, dis-
colored area was present in the fractured weld
over a length of approximately 122 mm (4.8 in.)
(location C).
Lack of fusion was a general condition
of the weld. Figure 48 shows a typical area
where lack of fusion was present in the weld.
Table 1 Chemical analysis of nose landing
gear piston axle
Chemical composition, %
Si Mn Ni Cr Mo V Fe
1.42 0.72 1.79 0.68 0.49 0.008 bal
Fig. 42
As-received failed multiple-leg aircraft-handling
sling
Fig. 43
Appearance of the fracture surface of the multiple-
leg aircraft-handling sling
Case Studies of Steel Component Failures in Aerospace Applications / 373
Name ///sr-nova/Dclabs_wip/Failure_Analysis/5113_351-393.pdf/Chap_11/ 18/8/2008 3:47PM Plate # 0 pg 373