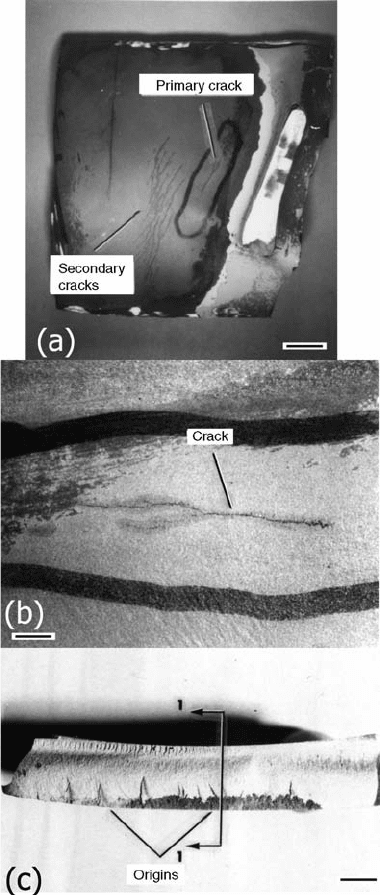
heat treated to the 1515 to 1655 MPa (220 to
240 ksi) tensile strength range. A nut with the
bolt was machined from 4140 steel bar heat
treated to the 1240 to 1380 MPa (180 to 200 ksi
tensile strength range.
Figure 28 shows the inboard flap hinge bolt
and nut as received for examination. The bolt
was approximately 102 mm (4 in.) long. The
bolt consisted essentially of the shank, which
was approximately 23 mm (0.9 in.) in diameter
and 64 mm (2.5 in.) long, and a threaded por-
tion, which was 23 mm (0.9 in.) in length with
thread type 0.5000-20 UNJF-3A THD in accor-
dance with MIL-S-8879. The unthreaded por-
tion of the bolt was chromium plated, while the
threaded portion was aluminum IVD coated.
The fracture had occurred at the transition of the
shank to the threaded portion of the bolt. The
fracture surface was examined visually and at up
to 30 · magnification using a stereomicroscope.
Figure 29 shows a macrograph of the fracture
surface. Fracture ridges emanated from an origin
that was located on the outer diameter surface
of the bolt at the location shown in Fig. 29.
The origin exhibited a reflective, intergranular
appearance. Apparent corrosion products were
also observed on the fracture surface.
Residual stresses were measured on the sur-
face of the bolt at locations 1 and 2, shown in
Fig. 28. The residual stresses were measured
using an x-ray residual-stress analyzer. Prior to
measuring the residual stresses, the chromium
plating (location 1) and the aluminum IVD
coating (location 2) were removed. The residual
stress measured at location 1 was 790+
100 MPa (–115+15 ksi), which indicated that
this area was properly shot peened as required
according to the engineering drawing. The resi-
dual stress measured at location 2 was 140+
100 MPa (20+15 ksi). This indicated that
this area was not shot peened. The engineering
drawing does not require this location to be shot
peened.
An SEM was used to examine the fracture
surface and to document the topographic fea-
tures. Figure 30 shows SEM fractographs taken
of the fracture surface. The fracture topography
at the origin was intergranular. The intergranular
topography extended for approximately
3
/
4
of
the way across the fracture surface, at which
point dimples indicative of ductile rupture were
present.
A laboratory-produced failure yielded a struc-
ture that consisted only of dimples.
The corrosion products on the service failure
fracture surface were subjected to an energy-
dispersive x-ray analysis. Calcium, potassium,
magnesium, and chlorine were identified as
being present.
Rockwell hardness measurements were made
on the inboard flap hinge bolt to verify heat
treatment condition. The hardness of the bolt
averaged 46 HRC. This met the hardness
Fig. 25
Appearance of primary crack removed from part.
(a) Region of primary crack where ion vapor-
deposited coating had been removed (13 mm). (b) Primary crack
showing branching (2 mm). (c) Fracture surface of crack after
opening (3 mm)
Case Studies of Steel Component Failures in Aerospace Applications / 365
Name ///sr-nova/Dclabs_wip/Failure_Analysis/5113_351-393.pdf/Chap_11/ 18/8/2008 3:46PM Plate # 0 pg 365