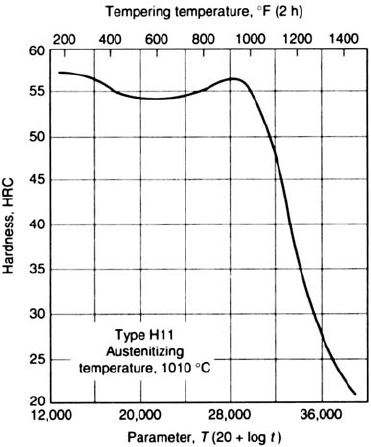
of cementite. At low temperatures, typically
below 500
C, the thermodynamic driving force
(free energy) is insufficient for such carbide
precipitation (mainly molybdenum or vanadium
carbides), and no hardness peak is observed
(Fig. 27). As the temperature increases, carbide
formation starts and very small carbides (a few
nanometers) precipitate within martensite laths.
Because they are fine and large in number, these
carbides are proper for obstructing dislocation
movement, causing substantial improvement in
strength. This occurs only at high temperatures,
with precipitation of alloy carbides pertaining
to materials used in hot working, in this case,
hot work tool steels. For higher temperatures,
carbides tend to transform to more stable types or
to coarsen, which increases the size and thus re-
duces the total number of precipitated carbides.
This results in loss of the dislocation blocking
effect, leading to strength reduction. The total
effect is schematically shown in Fig. 26.
Temperature and time affect the precipitation
behavior. From a thermodynamic point of view,
the lowest energy is obtained after alloy carbide
precipitation (reducing the free energy of ele-
ments in solid solution) and if their sizes are
as large as possible (reducing the surface free
energy). Consequently, the higher the time
or temperature, the easier it is for carbides to
become larger, and strength tends to decrease.
In tempering curves, such as those shown in
Fig. 24 and 28, this can be observed for a fixed
time (twice for 2 h) according to temperature.
However, a complete view is given by using
the tempering parameter, as shown in Fig. 39.
This combines the effects of both time and
temperature in only one variable, the parameter,
proportional to time and to a logarithm of the
temperature. Through this mathematical rela-
tion, it can be seen that temperature actually
has the highest effect; however, if excessively
long times are used at appreciably high tempera-
tures, the same effect may occur. For example,
4 h (twice 2 h tempering) at 600
C (1110
F,
parameter = 32,700) leads to ~46 HRC for H11,
which is equivalent to 15 h at 577
C (1070
F),
or 3 days at 550
C (1020
F), or approximately
1 month at 500
C (930
F). That is why
below 500
C, heating has practically no effect.
However, a second situation should also be
considered. Low times at excessively high
temperatures can produce rather important
effects. This is the situation for several tool
applications, where tools are in contact at very
high temperatures but for very short times. For
example, consider a forging tool that reaches
750
C(~1380
F) for a half-second during each
stroke. After producing 1000 parts, this tool will
be exposed to 750
C for a total time of 8.3 min.
Such heating is equivalent to a tempering para-
meter of 35,260 or 2 h at 691
C (1275
F). In
H11, such heating is capable of reducing the
hardness from 46 to less than 30 HRC.
It is in this context that the failures described
in this section should be considered. In some
situations, tools are correctly heat treated, but,
during hot working operation, heating is so
high that strength is reduced and failure is
accelerated. One example, shown in Fig. 40, is
a hot forging punch that usually exhibits low
life if compared to the whole set of tools. It is
made of DIN 1.2885, a highly temper-resistant
hot work steel that has high amounts of
molybdenum and cobalt for improvement of
this property. Even though the analysis showed
a continuous reduction of hardness approaching
the punch tip, which contacted the hot infor-
ging part. Besides the hardness values, it is
interesting to note the microstructural behavior.
Regions far from the hot working areas are
typically tempered martensite, becoming dar-
ker closer to the punch tip. As previously
explained, secondary carbides are not visible
Fig. 39
Tempering curve as a function of the time-tempera-
ture parameter for H11 steel containing 0.40% C,
0.92% Si, 5.09% Cr, 1.34% Mo and 0.52% V. For this curve,
t = time in hours, and T = temperature in
F+460. Source:
Ref 37
Failure Analysis in Tool Steels / 345
Name ///sr-nova/Dclabs_wip/Failure_Analysis/5113_311-350.pdf/Chap_10/ 18/8/2008 3:42PM Plate # 0 pg 345