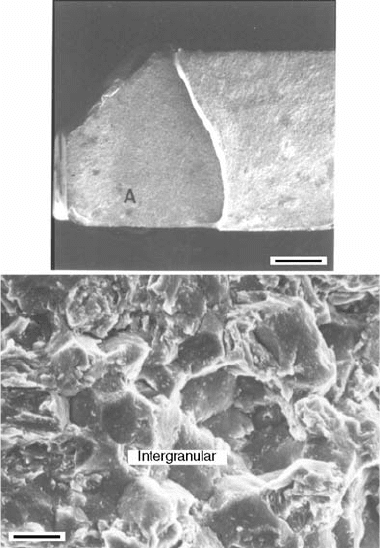
morphology of the cracks is typical of grinding
cracks (Ref 8).
A hydrogen analysis conducted on the inter-
nal gear yielded a value of 1.85 ppm, which is
not considered to be high enough to cause
hydrogen embrittlement.
Hardness measurements were made on the
internal gear to verify the heat treat condition.
The hardness of the gear near the observed
cracking was 44 HRC. This hardness value was
below the drawing hardness requirement of 50
to 53 HRC. The bulk hardness of the gear was
51 HRC.
The lower-than-expected hardness at the
crack initiation sites indicates that there was
some event that caused excessive local heating
of the microstructure. Because of the nature of
the part and typical manufacturing sequence, it
is likely that the grinding cracks occurred as a
result of aggressive grinding. Based on the
results of this investigation, it is concluded that
the internal spur gear failed due to aggressive
grinding.
Main Landing Gear Axle
During taxi, the MLG axle separated. The
axle had been installed for only 90 days, with a
total flight time of 62 h. The axle was fabricated
from 300M high-strength, low-alloy steel.
Shown in Fig. 56 is the as-received failed
MLG axle. Also shown in Fig. 56 is the location
of the fracture, which occurred adjacent to a
chromium- and cadmium-plated area. Also
shown in Fig. 56 is a worn (discolored) area of
chromium plating.
The fracture surface was examined visually
and at up to 50 · magnification using a stereo-
microscope. Figure 57 is a macrograph of the
fracture surface. Shown in Fig. 58 is an SEM
photograph of the wear that had removed the
protective plating adjacent to the fracture sur-
face. Multiple origins were located around the
periphery of the axle. Faceted areas character-
istic of an intergranular, delayed mode of failure
had progressed through approximately 80% of
the thickness. Fatigue propagated from the ends
of the intergranular areas, with several areas of
the wall being totally penetrated by the fatigue.
The relatively large intergranular areas and the
irregular shape of the intergranular area are
indicative of stress corrosion.
An SEM was used to examine the fracture
surface and to document the mode of failure.
Shown in Fig. 59 are SEM fractographs doc-
umenting topographic features, that is, inter-
granular topography and fatigue striations, on
the fracture surface. From the ends of the inter-
granular area, fatigue propagated through the
wall thickness. Also documented in Fig. 59 are
the lack of plating at a fracture origin and cor-
rosion products, which were present at the
intergranular fracture origins. The lack of plat-
ing and the presence of corrosion products are
indicative of a stress-corrosion failure. Also
shown in Fig. 59 is an area where the chromium
was intact.
The hardness of the axle was determined to be
53.9 HRC. This met the hardness requirement of
53 to 55 HRC.
A chemical analysis by atomic absorption
verified that the MLG axle was fabricated from
300M steel.
A metallographic specimen was prepared
through a typical fracture origin on the axle. The
specimen was prepared using standard metallo-
graphic techniques. As determined from the
metallographic specimen, the thickness of the
chromium plating was approximately 0.06 mm
Fig. 54
SEM fractographs showing the topographic features
of a typical fracture origin. (a) Fracture surface. Ori-
ginal magnification: 20·. (b) Location A showing intergranular
fracture. Original magnification: 3000·
378 / Failure Analysis of Heat Treated Steel Components
Name ///sr-nova/Dclabs_wip/Failure_Analysis/5113_351-393.pdf/Chap_11/ 18/8/2008 3:47PM Plate # 0 pg 378