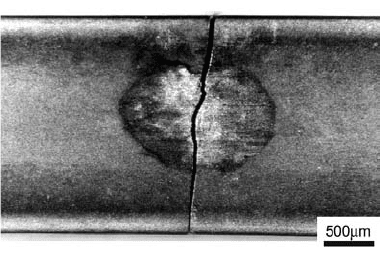
act as abrasives on the surface, since the small-
amplitude movements avoid their dispersion
apart from the source point. Figure 29 presents a
micrograph from a plasma nitrided Cr-Mo-V
steel, where a microcrack formed in the fretting
region.
More than one mechanism can be responsible
for the wear observed on a particular part. The
most critical function provided by lubricants is
to minimize friction and wear to extend equip-
ment service life. Gear failures can be traced to
mechanical problems or lubricant failure.
Lubricant-related failures are usually traced to
contamination, oil film collapse, additive
depletion, and use of improper lubricant for the
application. The most common failures are due
to particle contamination of the lubricant. Dust
particles are highly abrasive and can penetrate
through the oil film, causing plowing wear or
ridging on metal surfaces. Water contamination
can cause rust on working surfaces of gears and
eventually destroy metal integrity. To prevent
premature failure, gear selection requires careful
consideration of the following: gear tooth geo-
metry, tooth action, tooth pressures, construc-
tion materials and surface characteristics,
lubricant characteristics, and operating environ-
ment.
Environmentally Assisted Failure
Corrosion is chemically induced damage
to a material that results in deterioration of
the material and its properties. Corrosion
can seldom be totally prevented, but it can be
minimized or controlled by proper choice of
material, design, coatings, and occasionally
by changing the environment. Various types of
metallic and nonmetallic coatings are regularly
used to protect metal parts from corrosion.
Corrosion may result in failure of the com-
ponent. Several factors should be considered
during a failure analysis to determine the effect
corrosion played in a failure, such as type of
corrosion, corrosion rate, the extent of the cor-
rosion, and the interaction between corrosion
and other failure mechanisms.
Uniform, pitting crevice, galvanic, and stress-
corrosion cracking are the most common types
of corrosion. Uniform corrosion is characterized
by corrosive attack proceeding evenly over the
entire surface area or a large fraction of the total
area. General thinning takes place until failure.
On the basis of tonnage wasted, this is the most
important form of corrosion.
Stress-corrosion cracking necessitates a
tensile stress, which may be caused by residual
stresses, and a specific environment to cause
progressive fracture of a metal. Aluminum
and stainless steel are well known for stress-
corrosion cracking problems. However, all
metals are susceptible to stress-corrosion crac-
king in the right environment.
Pitting corrosion is a localized form of cor-
rosion by which cavities or holes are produced
in the material. Pitting is considered to be
more dangerous than uniform corrosion damage
because it is more difficult to detect, predict, and
design against. Corrosion products often cover
the pits. A small, narrow pit with minimal
overall metal loss can lead to the failure of
an entire engineering system. Pitting corrosion,
which, for example, is almost a common
denominator of all types of localized corrosion
attack, may assume different shapes.
Crevice corrosion is a localized form of
corrosion usually associated with a stagnant
solution on the microenvironmental level. Such
stagnant microenvironments tend to occur in
crevices (shielded areas) such as those formed
under gaskets, washers, insulation material,
fastener heads, surface deposits, disbonded
coatings, threads, lap joints, and clamps. Crevice
corrosion is initiated by changes in local chem-
istry within the crevice.
Galvanic corrosion (also called dissimilar-
metal corrosion or, wrongly, electrolysis) refers
to corrosion damage induced when two dis-
similar materials are coupled in a corrosive
electrolyte. It occurs when two (or more) dis-
similar metals are brought into electrical contact
under water. When a galvanic couple forms, one
of the metals in the couple becomes the anode
Fig. 29 Fretting fatigue at the surface of a Cr-Mo-V steel
General Aspects of Failure Analysis / 131
Name ///sr-nova/Dclabs_wip/Failure_Analysis/5113_111-132.pdf/Chap_03/ 18/8/2008 3:03PM Plate # 0 pg 131