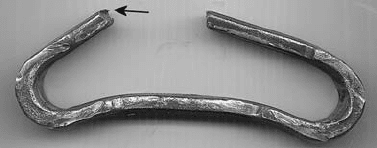
ductile fracture, or could this be a brittle frac-
ture? Imagine that only this one photograph is
available, and it must be determined whether
this was a ductile or brittle crack.
Clearly, the steel that was used to make the
link has the capability of being deformed. In
other words, the steel is ductile at the conditions
present at the time of bending. The analyst must
not be satisfied with that answer, though. The
proper analysis includes a determination of
when the deformation happened. Postfracture
deformation does not make the crack event itself
ductile. The macroscale deformation must occur
during and as an inseparable part of the fracture
process for the crack itself to be a ductile crack
event.
For those unfamiliar with this methodology,
imagining that the link broke suddenly while it
was under load can be helpful. If the crack were
ductile, one would likely see some necking at the
crack location, since chain links are generally
loaded in tension. No such localized deforma-
tion is observed in this case. On closer exam-
ination, one can see a tiny shear lip at the top
edge of the fracture surface. That makes this
crack, for the most part, a brittle crack at the
macroscale, despite the presence of available
ductility in the material. The visible deformation
near the center of the lower (originally straight)
portion of the link happened after the crack was
completely formed.
In doing fracture analysis, it is important
to distinguish the capability of ductility in the
material from the behavior at the time of
the crack event. Despite the material ductility,
the crack happened in a brittle way. Closer
examination of other views not shown provide
clear evidence that this was a fatigue crack.
Beach marks were visible. Fatigue cracks grew
below the yield strength of the component,
creating macroscale brittle features. To clarify
one other potential source of confusion, it is
important to remember that tensile refers to a
loading geometry. Fatigue is a type of crack
path. In this case, a fatigue crack grew due to a
tensile load in the horizontal portions of the link
(as shown).
To add a few more details to this case study,
the chain was in service at a plant that processes
meat, and strong acids were used to clean the
conveyor systems. This crack actually initiated
at a corrosion pit on the inside surface. The
cleaner reached the inner surfaces, but the em-
ployees may not have rinsed the chain very well.
This allowed a corrosion pit to form, which then
allowed a fatigue crack to grow. Again, it is
important to understand that the material itself is
ductile; there is nothing wrong with the material.
People involved with failure analysis need to
keep in mind that material behavior is or at
least may be different from material capability.
People doing failure analysis work need to be
able to distinguish inherent capability and actual
behavior.
To underscore the importance of separating
the behavior from the capability, imagine the
potential corrections that may be considered if
someone found this to be a ductile overload
fracture. The “cure” may be to make it harder. In
the case of the acid cleaning, harder steels are
often more susceptible to stress corrosion than
softer steels. If the “harder-is-the-answer” the-
ory were put into practice, an undesirably short
life may become a horribly short life. It is
important to be sure that a crack that is diag-
nosed as ductile is really ductile and one that is
diagnosed as brittle is really brittle. Finally,
returning to the heat treating issues, the fact that
someone misdiagnosed this crack as a ductile
fracture may lead to the heat treater being
blamed for overtempering or inadequate hard-
ening. In fact, until now, the potential blame or
innocence of the heat treater has not been
investigated in any thorough manner. It is poss-
ible that poor heat treating or poor material
manufacture contributed to the ease of corrosion
attack, and the meat processing plant employees
were blamed incorrectly. Further examination of
the microstructure is required to reveal the root
physical cause of the fracture and its timing.
Finally, there is the shaft fragment shown in
Fig. 5. The shape is cylindrical. The image
shows one fracture face. No necking or reduc-
tion in area is visible at the fracture face location.
However, this is a ductile fracture. It is necessary
to know that this shaft broke in torsional
loading. In torsion, the shear stresses are in
the transverse orientation to the length of the
shaft. To best understand macroscale ductile and
Fig. 4
Example of a macroscale brittle fracture in tensile
loading
92 / Failure Analysis of Heat Treated Steel Components
Name ///sr-nova/Dclabs_wip/Failure_Analysis/5113_87-109.pdf/Chap_02b/ 21/8/2008 10:51AM Plate # 0 pg 92