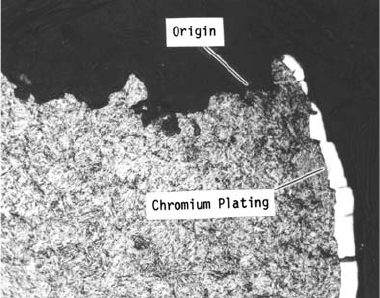
perpendicular to the tensile stresses contributing
to propagation and initiation. However, this is
not always the case. Structural steels exposed to
agricultural ammonia may exhibit nonbranched
cracking.
Stress-corrosion cracking has several special
characteristics that differ entiate it from other
forms of cracking:
Only certain specific environments for a
specific alloy system cause SCC. There is
no general pattern regarding the corroding
environments or alloy system s.
Pure metals are much less susceptible to
SCC.
Cathodic protection has been succe ssful in
preventing the initiation of SCC or in stop-
ping the propagation of SCC.
Addition of certain soluble salts effectively
can “poison” the environment and either re-
duce or stop the propagation of SCC cracks.
Certain metallurgical features, such as grain
size, can influence the susceptibility of an
alloy system to SCC attack.
Macroscopically, fractures produc ed by SCC
show little ductility and nearly always appear
brittle. The fracture surfaces usually contain re-
gions that are identifiable as the crack initiation
site, slow crack propagation, and final failure.
The regions containing the slow propagation
often contain corrosion products or are
discolored. This region extends to the region of
final fast fracture. However, this can also
be misleading, because the fracture could have
corroded before inspection, or the environment
may not be conducive to straining the fracture.
It is often difficult to differentiate between
SCC and hydrog en-induced damage solely from
the fracture surface. Fractures of both types
exhibit intergranular features and tend to follow
prior-austenite grain boundaries. Metallography
is important to determine if branc hed cracking
has occurred. Even so, the absence of branched
cracking may not prec lude SCC. In general, the
environment that the part was exposed to can be
the deciding factor of whether it is SCC or
hydrogen embrittlement (Fig. 48).
Low-carbon steels generally become more
susceptible to SCC as the carbon concentration
increases. Decarburized steels and pure iron are
resistant to SCC. Microstructure plays a greater
role in susceptibility to SCC than does the
alloying elements. High-alloy steels in a variety
of environments show that the heat treated
strength of the alloy is more important than
strictly the concentration. Steels that have been
heat treated to 1240 MPa (180 ksi) or higher are
especially susceptible to SCC. Typical envir-
onments that can cause SCC in steels are shown
in Table 2.
Caustic cracking in boilers is a serious SCC
problem and has caused many failures in steam
boilers. These failures usually initiate in riveted
and welded structures, where small leaks allow
buildup of caustic soda and silica. Cracking is
usually intergranular. Failures of this type have
occurred with concentrations of NaOH as low as
5% in water. Failures take place when the
operating temperature is in the range of 200 to
250
C (390 to 480
F). The concentration of
NaOH needed to cause cracking initiation
decreases as the temper ature is increased.
Cracking of low-carbon steels and low-alloy
steels in nitrate solutions occurs in tubing and
couplings in high-pressure condensate wells.
Cracking in nitrate solutions is intergranular,
following prior-austenite grain boundaries.
Generally, acidic solutions cause this type of
cracking. Raising the pH of the solution enhan-
ces resistance to SCC, while increas ing the
concentration of nitrate-containing solutions
tends to increase the susceptibility to SCC.
Carbon steel tanks containing ammonia have
also developed leaks because of SCC. Both plain
carbon steels and quenched and tempered steel
plate have shown a susceptibility to SCC in
ammonia. Failures occurred in ammoni a mixed
with air and carbon dioxide. The presence of
water vapor delayed cracking.
Halide-containing environments, such as
seawater, are particularly severe for alloy steels
Fig. 47
Micrograph showing quenched and tempered mar-
tensite, typical of 300M heat treated to HRC 54 to 55.
Note that the chromium plating is intact.
Overview of the Mechanisms of Failure in Heat Treated Steel Components / 73
Name ///sr-nova/Dclabs_wip/Failure_Analysis/5113_43-86.pdf/Chap_02/ 18/8/2008 2:56PM Plate # 0 pg 73