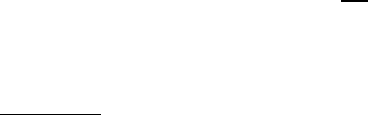
54 2 Material Behaviour and Failure
were, the interatomic forces would act across it and it would cease to be a crack.
However, if the material is brittle, the region in which the elastic solution is inappli-
cable may be restricted to a relatively small process zone surrounding the crack tip.
Furthermore, the certainly very complicated conditions in this process zone can only
be influenced by the surrounding elastic material and hence the conditions for failure
must be expressible in terms of the characteristics of the much simpler surrounding
elastic field. As long as the process zone is small compared with the other linear
dimensions of the body (notably the crack length), it will have only a very localized
effect on the surrounding elastic field, which will therefore be adequately character-
ized by the dominant singular term in the linear elastic solution, whose multiplier
(the stress intensity factor) then determines the conditions for crack propagation.
It is notable that this argument requires no assumption about or knowledge of
the actual mechanism of failure in the process zone and, by the same token, the
success of linear elastic fracture mechanics as a predictor of the strength of brittle
components provides no evidence for or against any particular failure theory.
22
Design based on fracture mechanics
Fracture mechanics methods enable us to predict the load at which a crack in a com-
ponent will start to propagate. The procedure is to calculate the stress intensity factor
at the crack tip and compare it with measured and tabulated values of fracture tough-
ness for the material. In most cases, fracture is dominated by tensile loading and
hence by the mode I stress intensity factor K
I
. The fracture toughness is therefore
defined as the value of K
I
at which fracture occurs and it is usually denoted by K
Ic
.
Fracture toughness is measured by loading a plane edge crack in a configuration
locally similar to that shown in Figure 2.15 (Mode I) above. The results obtained are
independent of the thickness of the specimen if this is sufficiently large, but tests on
thin specimens generally give larger values for fracture toughness because the free
surfaces of the specimen have a stress relieving effect. Standardized test specimens
are therefore used to ensure consistency of the results.
23
The use of tabulated K
Ic
val-
ues in design will give good predictions for cracks in plates as long as the thickness
of the plate t satisfies the condition
t ≥ 2.5
K
Ic
S
Y
2
.
For thinner plates, the condition K
I
<K
Ic
is conservative and a more efficient design
may be possible using more advanced concepts from elastic-plastic fracture mechan-
ics.
24
22
Indeed, experimental values of fracture toughness are not compatible with theoretical pre-
dictions based on Griffith’s theory and estimates of surface energy. For more details of the
extensive development of the field of fracture mechanics, the reader is referred to the many
excellent texts on the subject, such as Kanninen and Popelar (1985), Leibowitz (1971).
23
See, for example, Boresi et al. (1993), Figure 15.2.
24
See, for example, S.T. Rolfe and J.M. Barsom (1977), Fracture and Fatigue Control in
Structures, Prentice-Hall, Englewood Cliffs, NJ, Chapter 19.