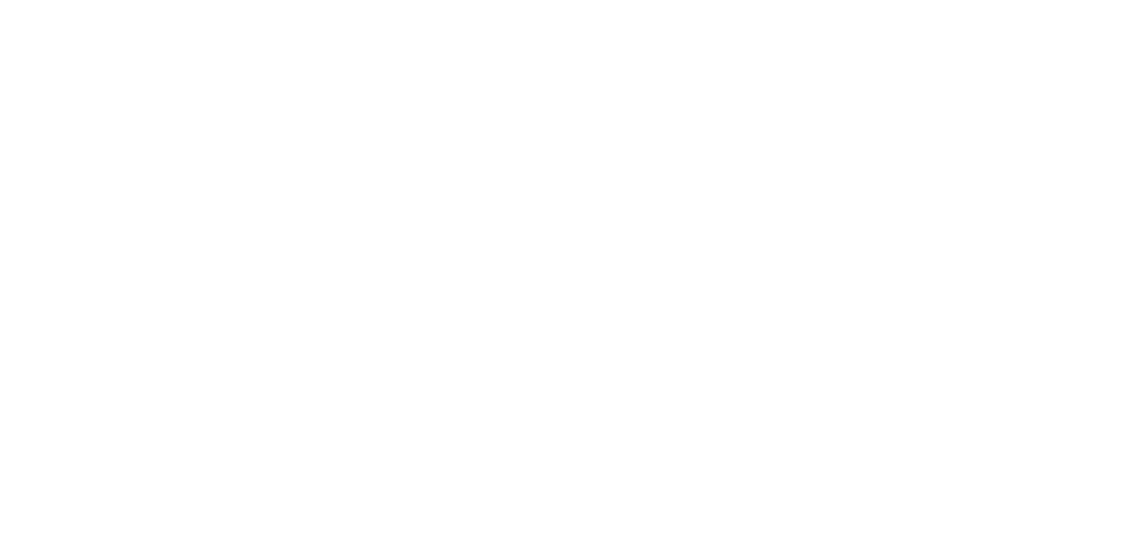
AWS B4.0:2007 CLAUSE 10. WELDABILITY TESTING
93
ture remains below the maximum recommended by the
electrode manufacturer or specification. Despite these
precautions, hydrogen levels in weld metal can exceed
the safe level at which sound weldments can be fabri-
cated. The presence of excessive amounts of dissolved
hydrogen can be observed as time delayed transverse
cracking of weld metal. As hydrogen levels decrease,
weld-metal cracking propensity decreases, however, dif-
fusible hydrogen can result in reduced tensile ductility of
the weld metal.
10.8.4.2 The major characteristics of hydrogen
embrittlement are its strain-rate sensitivity, temperature
dependence and susceptibility to delayed fracture.
Unlike most embrittlement phenomena, hydrogen
embrittlement is enhanced by slow strain rates. For steel,
the region of greatest susceptibility to hydrogen embrit-
tlement is at approximately room temperature.
10.8.4.3 Hydrogen introduction into the weld metal is
not limited to the SMAW process. Other welding pro-
cesses (GMAW, SAW, etc.) may also provide the envi-
ronment that promotes the conditions leading to
hydrogen-related delayed cracking.
10.8.5 Apparatus
10.8.5.1 A simple fixture is required to hold the speci-
men so that the test welds can be deposited in the flat
position. Welding in the flat position minimizes variabil-
ity in welder skill and enhances the depositing of satis-
factory welds not requiring quality interpretation.
10.8.5.2 Electric strip heaters are required to provide
the preweld, intraweld, and postweld heating of the test
specimen. Appropriate temperature control, measuring,
and recording instruments may be needed to document
the thermal treatment applied to the test specimen.
10.8.6 Specimens
10.8.6.1 The specimen and groove configuration is
shown in Figure 10.8.1. The specimen may be prepared
by thermal cutting.
10.8.6.2 The trough is prepared by air carbon arc cut-
ting followed by grinding of the trough surface to bright
metal and required dimensions.
10.8.6.3 The amount of restraint required to produce
time-delayed weld metal cracking is provided by the
mass of the plate surrounding the trough groove.
10.8.6.4 The location of tension test specimens in the
trough weld is shown in Figure 10.8.2. Tension testing is
used to evaluate tensile ductility.
10.8.6.5 A series of test specimens is welded with
each specimen subjected to a thermal treatment proce-
dure designed to eliminate hydrogen related delayed
weld metal cracking and/or reduced tensile ductility.
10.8.7 Procedure
10.8.7.1 The test welds are deposited in the trough in
the flat position.
10.8.7.2 The starts and stops of the weld beads are
stacked in the trough one on top of the other as indicated
in Figure 10.8.2. This is done in order to evaluate the
susceptibility of these locations to high levels of hydro-
gen and possible defect sites. All starts and stops shall be
lightly ground between passes.
10.8.7.3 The initial trough specimen is produced by
continuous welding and minimum preheat and interpass
temperature in order to simulate and effect time delayed
weld metal cracking. Appropriate preheat, interpass, and
postweld thermal treatments are applied to subsequent
specimens until weld metal cracking is eliminated and/or
tensile ductility is recovered. An outline of suggested
thermal treatments is as follows:
(1) Continuous welding with required preheat and
interpass temperature applied; no postweld treatment.
Delayed weld cracking and reduced tensile ductility
should be evident;
(2) Continuous welding of 1/2 in (13 mm) thick lay-
ers with required preheat and interpass temperature
applied; followed by an elevated postweld treatment at
400°F (204°C) for 12 h to 16 h; and
(3) Other thermal treatments may be applied provid-
ing they result in eliminating weld metal cracking and/or
reduced tensile ductility.
10.8.7.4 All trough specimens shall be subjected to
magnetic particle inspection immediately upon comple-
tion of welding and daily for periods up to 30 days. Radi-
ography may be used to confirm the results of magnetic
particle inspection for weld soundness.
10.8.7.5 The location of tension test specimens in the
trough weld is shown in Figure 10.8.2. Tensile testing is
used to evaluate the loss of tensile ductility in the weld
metal as a result of hydrogen embrittlement.
10.8.7.6 When the test is used to evaluate hydrogen-
cracking susceptibility, a diffusible hydrogen determina-
tion shall be performed for each welding process and
consumable in accordance with AWS A4.3. The diffus-
ible hydrogen determination shall be performed under
the same conditions as the test weld.
10.8.8 Report. In addition to the requirements of the
applicable documents, the report shall include the
following:
Copyright American Welding Society
Provided by IHS under license with AWS
No reproduction or networking permitted without license from IHS
--`,,```,,,,````-`-`,,`,,`,`,,`---