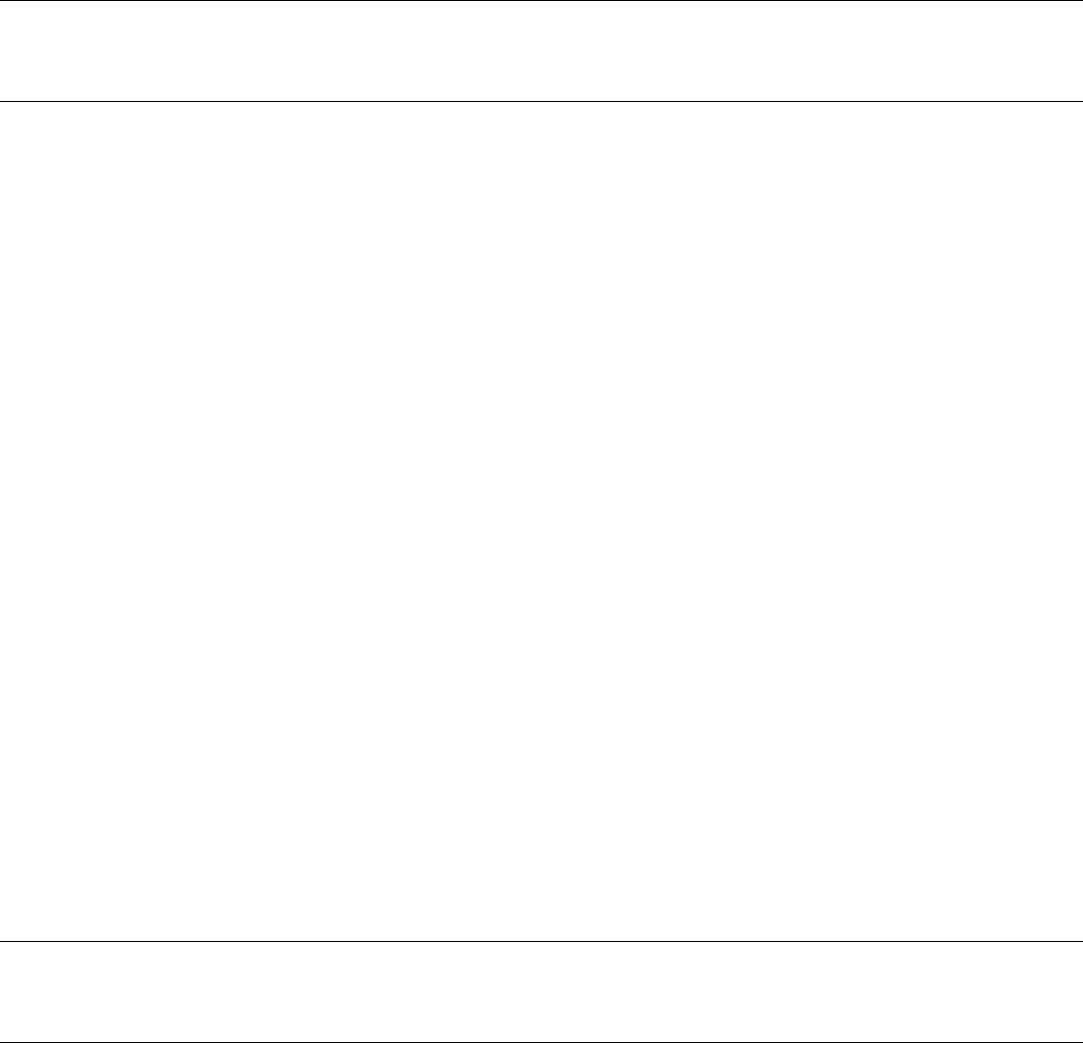
When the eccentric upset is some distance removed from the end of the forging, it is impossible to position the stock in an
initial bending operation. In such parts, the metal must be forced to upset eccentrically into cavities in the punches, dies,
or both by the axial movement of the punches. The degree of eccentricity of such upsets is more limited, because of the
problem of preventing the stock from initially buckling in the direction of the upset and thus producing cold shuts on the
opposite side.
Hot Upset Forging
Revised by Wilfred L. Mehling, Ajax Manufacturing Company
Double-End Upsetting
For many forgings, the use of double-end upsetting--that is, two separate upsetting operations performed on opposite ends
of the stock--is required for producing the desired shape. In double-end upsetting, the passes for the operation at each end
are based on the same design considerations as in producing an upset on only one end of a straight bar. Double-end
upsetting, however, often presents handling and heating problems not encountered in single-end upsetting.
One of the first decisions that must be made in planning the processing for double-end upset forgings is which end is to be
forged in the first heat. If there is a difference in the upset diameters, it is almost always preferable to forge the smaller
diameter first. This usually simplifies handling in the second heat. It also permits closer spacing in the furnace for the
reheating, which results in more efficient use of furnace capacity.
The cut blank for the first-heat operations is handled by tongs or porter bars, as in single-end upsetting. Handling in
second-heat operations is done by similar means, except that the design of the handling tools is influenced by the shape of
the first upset.
If the finished part produced from the forging will have a drilled or bored hole central with the axis of the forging, it is
often desirable, as a first-heat operation, to pierce a hole of suitable diameter and depth to facilitate handling in the second
operation with a porter bar made to fit the pierced hole. When pierced holes are not permitted, some other means must be
used to handle the forging during the second upsetting operation.
When a double-upset forging requires a pierced through hole, part of the hole is pierced in each upset end, and the
connecting metal is removed by trimming, either in an additional pass in the upsetter or in a separate operation. Forgings
to be produced by double-end upsetting must be provided with enough draft to facilitate insertion and removal from the
second operation without pinching or sticking. To prevent distortion of the first-heat upset during the second-heat
operations, the workpiece should be reheated such that the upset portion is kept as cool as possible. The difference in
diameters, together with proper placement in the furnace, usually provides a satisfactory temperature differential. A
greater differential may be provided by the use of a water-cooled furnace front designed to shield the first-heat upset from
furnace heat during reheating.
Hot Upset Forging
Revised by Wilfred L. Mehling, Ajax Manufacturing Company
Upsetting With Sliding Dies
The hot upset forging process is not limited to forging heads or upsets at the ends of bars; it can also gather material for
the upset at any point along the length of a bar. This special type of upsetting, which can be performed on round or
rectangular bars, requires special tooling in the form of sliding dies. These sliding dies are inserted into the gripper-die
frames.
A typical sliding-die arrangement is shown in Fig. 13. With this method, one of the sliding dies moves in the same
direction as the moving gripper die to hold the workpiece firmly against a second sliding die and a stationary gripper die.