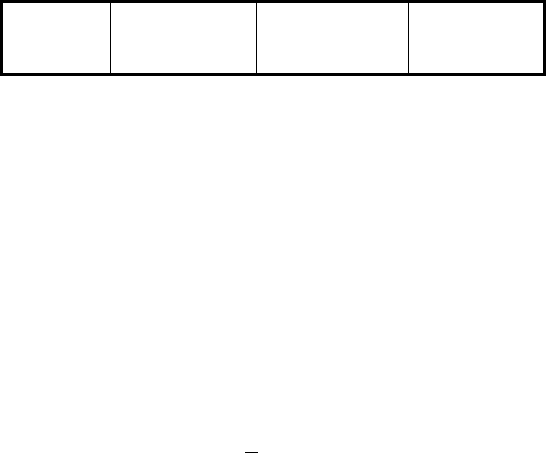
10 2250 20 200
(a)
1 in. = 25.4 mm.
(b)
1 tonf = 8.896 kN
Gripper-die stroke is one of the simplest indicators of the maximum diameter of upset (assuming that the stock is a
readily forgeable carbon or alloy steel) that can be safely produced on a given size of machining. This stroke must permit
a forging having a maximum-diameter upset to drop freely between the dies into the discharge chute below the dies. In
using this criterion, allowance must be made for the fact that, unless brake adjustment is perfect, there will be some
override (failure of the brake to stop the movement in the extreme open condition), which will reduce the effective
clearance between the dies. Therefore, the maximum diameter of upset on forgings that are to drop between the dies
should be 12.5 to 25 mm (
to 1 in.) less than the gripperdie stroke, depending on machine size. This is a general rule
that is applicable to simple upsets in readily forgeable steels and adjustments must be made to accommodate varying
conditions. For example, the maximum diameter of upset on forging from more difficult materials, such as stainless steel
or heat-resistant alloys, must be reduced in proportion to the reduced forgeability of the material. Similarly, on extremely
thin flanges or on upsets having difficult-to-fill contours, maximum diameters must be reduced in proportion to the
increase in force required to finish the upset; otherwise, the part will not be completely filled.
Under some circumstances, with special consideration to die design to avoid overloading the machine, it is possible to
produce forgings with larger-diameter upsets than the above rule would indicate. When this is done, forgings must be
moved forward ahead of the dies if they are to be dropped into the chute, or if long bars are being upset, they are moved
forward to clear the dies and then raised and brought back over the top of the dies and out the rear of the machine, where
they are unloaded by the operator. The following three techniques can be employed to extend the maximum diameter of
upset that can be produced in a machine of a given size.
The first technique involves the use of a blocking pass that finishes the center portion of the upset, followed by a final
pass that finishes the outer portion. By this procedure, the effective area of the metal being worked is lessened in each
pass. To be effective, however, the face of the finished upset should be slightly concave, so that the finishing punch does
not contact the center area finished by the blocking pass.
Second, flange diameters that are in excess of the normal machine capacity can be forged if no attempt is made to confine
the outside diameter of the flange. This requires some additional stock removal by machining or trimming, but is an
effective means of producing a larger-than-normal upset on an available machine without damage to the machine.
Lastly, the maximum diameter of upset that can be produced in a given size of machine can sometimes be increased by
slightly modifying the shape of the upset to facilitate metal flow. Upset shapes that restrict metal flow should be avoided
in favor of those that encourage the metal to flow in the desired direction. Small corner or fillet radii and thin flanges
should be avoided when the size of a forging makes it borderline for machine capacity.
Die Space. For some applications, a larger machine must be selected because more die space is needed. Die blocks must
be high enough to accommodate all passes, and the dies should be long enough to contain all impressions and to allow for
gripping or for tong or porter-bar backup. Dies are normally thick enough for any forging that can be produced in the
machine in which they fit.
Throat clearance through the machine may become a limiting factor, particularly in upsetting long bars or tubes that
extend through the machine throat during operation. The extension of the stationary die beyond the throat is one-half of
the maximum diameter of stock that can be cleared.
Header-slide stroke is normally adequate for any forging that can be produced on a given size of machine. However,
in some applications, unusually long punches will be retracted insufficiently when the machine is open, thus inhibiting
installation and removal of the dies without interference. Under these circumstances, a larger machine may be required.