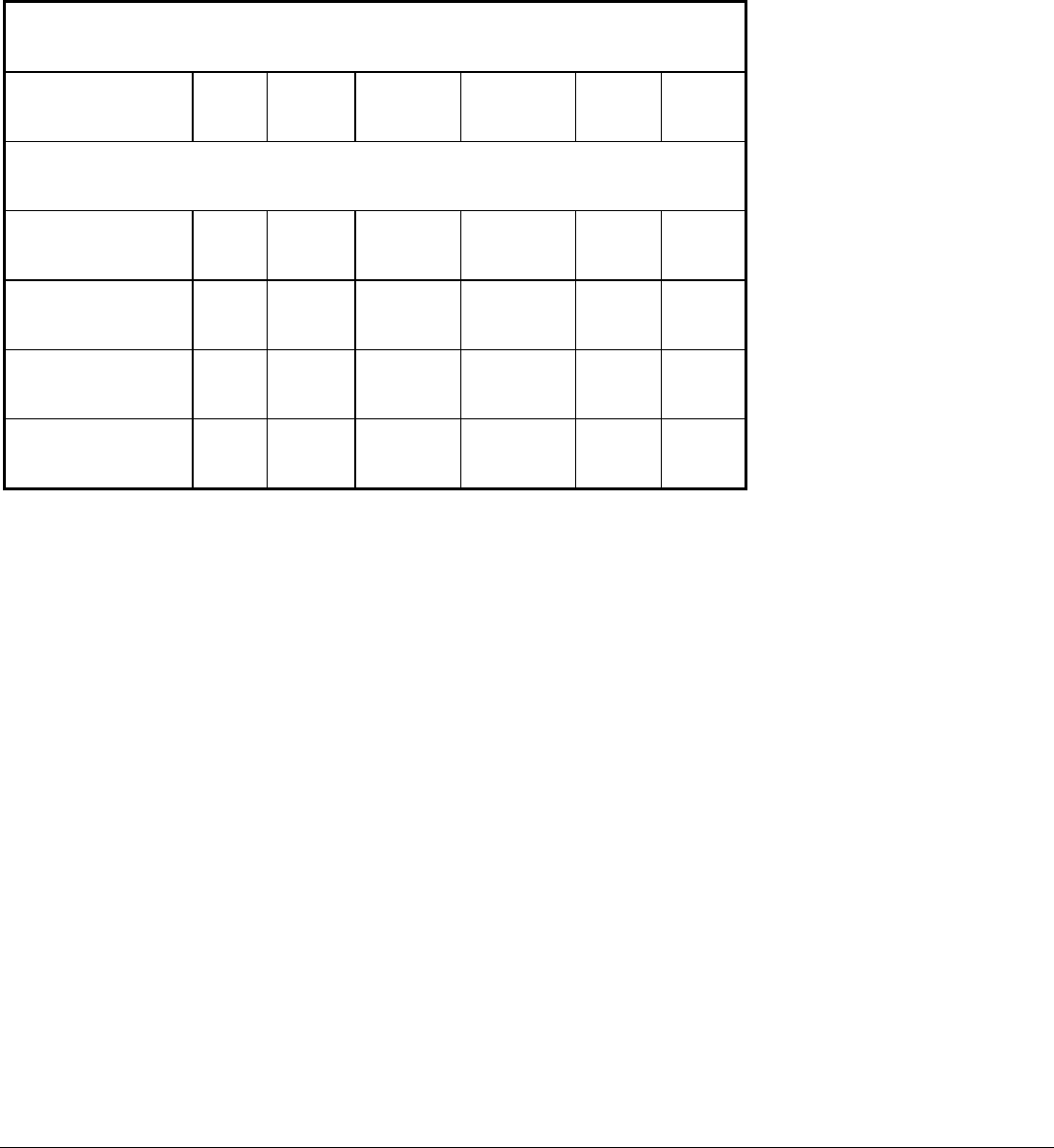
Carbon-tungsten special-purpose tool steels
F2, F3 815 1500 980-1095 1800-2000 900
1650
Low-carbon mold steels
P1 . . . . . . 1205-1290 2200-2350 1040
1900
P3 . . . . . . 1040-1205 1900-2200 845
1550
P4 870 1600 1095-1230 2000-2250 900
1650
P20 815 1500 1065-1230 1950-2250 815 1500
(a)
The temperature at which to begin forging is given as a range; the higher side of the range should be used for large sections and heavy or rapid
reductions, and the lower side for smaller sections and lighter reductions. As the alloy content of the steel increases, the time of soaking at
forging temperature increases proportionately. Similarly, as the alloy content increases, it becomes more necessary to cool slowly from the
forging temperature. With very high alloy steels, such as high-speed steels and air-hardening steels, this slow cooling is imperative in order to
prevent cracking and to leave the steel in a semisoft condition. Either furnace cooling of the steel or burying it in an insulating medium (such
as lime, mica, or diatomaceous earth) is satisfactory.
(b)
Forging temperatures for water-hardening tool steels vary with carbon content. The following temperatures are recommended: for 0.60-1.25%
C, the range given; for 1.25 to 1.40% C, the low side of the range given.
Heating Time. For any steel, the heating time must be sufficient to bring the center of the forging stock to the forging
temperature. A longer heating time than necessary results in excessive decarburization, scale, and grain growth. For stock
measuring up to 75 mm (3 in.) in diameter, the heating time per inch of section thickness should be no more than 5 min
for low-carbon and medium-carbon steels or no more than 6 min for low-alloy steel. For stock 75 to 230 mm (3 to 9 in.)
in diameter, the heating time should be no more than 15 min per inch of thickness. For high-carbon steels (0.50% C and
higher) and for highly alloyed steels, slower heating rates are required, and preheating at temperatures from 650 to 760 °C
(1200 to 1400 °F) is sometimes necessary to prevent cracking.
Finishing temperature should always be well above the transformation temperature of the steel being forged in order
to prevent cracking of the steel and excessive wear of the dies, but should be low enough to prevent excessive grain
growth. For most carbon and alloy steels, 980 to 1095 °C (1800 to 2000 °F) is a suitable range for finish forging. More
information on forging parameters for ferrous alloys is available in the articles "Forging of Carbon and Alloy Steels" and
"Forging of Stainless Steel" in this Volume.
Closed-Die Forging in Hammers and Presses
Forging Temperatures for Steels
Maximum safe forging temperatures for carbon and alloy steels are given in Table 2, which indicates that forging
temperature decreases as carbon content increases. The higher the forging temperature, the greater the plasticity of the
steel, which results in easier forging and less die wear; however, the danger of overheating and excessive grain coarsening
is increased. If a steel that has been heated to its maximum safe temperature is forged rapidly and with large reduction, the
energy transferred to the steel during forging can substantially increase its temperature, thus causing overheating.
Table 2 Maximum safe forging temperatures for carbon and alloy stools of various carbon contents