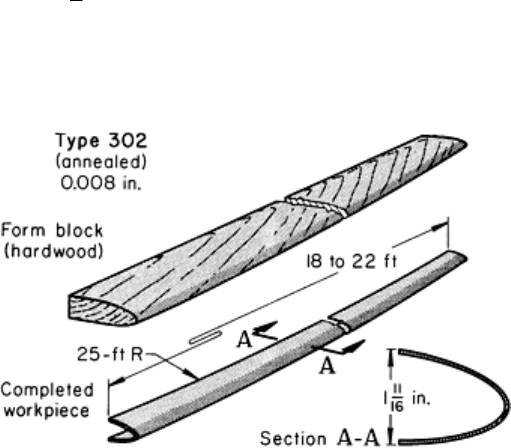
Lubricants. If there is little or no movement after contact between workpiece and form block, as in stretch wrapping or
single-die draw forming, little or no lubricant need be used except when deformation is severe. A low-viscosity
chlorinated oil or wax provides excellent chemical EP action and convenience of use. If there is considerable movement
of the work metal against the dies (such as against the wiper shoe in radial-draw forming), pigmented lubricants are
sometimes used. The following example describes an application in which no lubricant was used in the stretch forming of
a sharply contoured part.
Example 25: Dry Stretch Forming of an Airfoil Leading Edge.
The leading edge of an airfoil was stretch formed dry from a type 302 stainless steel blank, 0.20 mm (0.008 in.) thick, 115
mm (4
in.) wide, and 5.5 to 6.7 m (18 to 22 ft) long, that had been roll formed to the airfoil contour shown in section
A-A in Fig. 30. The blank had been annealed before roll forming, and it was stretch formed, without further annealing, to
a 7.6 m (25 ft) radius with the heel of the contour pointing out (Fig. 30).
The airfoil was stretch formed in a radial-draw former over
a hard-maple form block with the airfoil contour carved
into its surface (Fig. 30). Lubricant was not used, because
it had previously caused local variations in friction. Time
for forming was 10 min per piece with three men working.
Setup time was 2 h. A typical production lot was 100
pieces.
The rolled contour had to be held within ±0.1 (±0.005 in.)
after stretch forming. The envelope tolerance on the
stretch-formed shape was 0.76 mm (0.030 in.).
Springback. In sharply contoured pieces that have a
relatively deep, wide cross section, some springback
cannot be avoided, even in annealed metal. During severe
stretch forming, considerably higher strength, and
therefore appreciably higher elastic recovery, is developed
in the more highly stressed convex surface.
Springback in regular, symmetrical sections can usually be
offset by overbending the piece. Dimensional variations in workpieces are primarily caused by variations in springback,
which are in turn caused by variations in mechanical properties from sheet to sheet.
If the workpiece is irregular in cross section, if preformed flanges are to be held to a certain angular position, or if the
curve of the form varies in severity, springback may cause twist or irregular distortion of the workpiece. Various methods
of blocking, pretwisting, or overforming are used to prevent or correct this distortion. In the following example, an
asymmetrical cross section was twisted during forming to offset the twist caused by springback.
Example 26: Use of Twisting to Compensate for Springback in Stretch Forming.
The curved channel section shown in Fig. 31 was stretch formed from quarter-hard type 302 stainless steel strip, 1.07 mm
(0.042 in.) thick, that had been preformed in a press brake. Although the channel fit closely in the groove of the form
block, springback caused considerable twist in the finished piece.
Fig. 30 Airfoil on which the l
formed to a long convex shape without lubricant in a
radial-draw former.