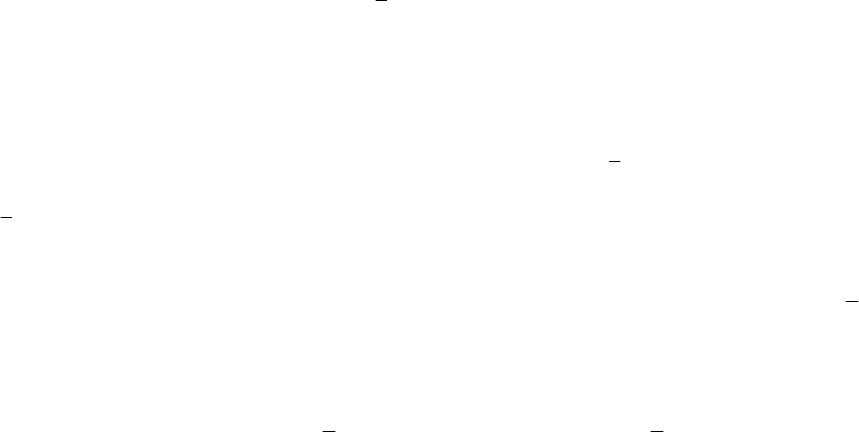
the dome. The piece was drawn from a 280 mm (11
in.) diam blank produced in operation 1 (not shown).
Dimensions in figure given in inches.
The stock was 289 mm (11.375 in.) wide annealed type 304 stainless steel strip, 1.1 mm (0.042 in.) thick. A single-action
mechanical press with a spring-loaded pressure pad was used to cut 280 mm (11
in.) diam blanks from the strip,
leaving 3.2 mm (
in.) minimum scrap on each side of the strip.
The first draw was made in a 2200 kN (250 tonf) double-action mechanical press. The punch was 83 mm (3
in.) in
diameter; therefore, much of the surface of the dome was drawn free (operation 2, Fig. 19). This required careful control
of the blankholder pressure to prevent puckers and wrinkles. Blankholder pressure had to be adjusted for every lot of
steel; it varied from 5.5 to 6.9 MPa (0.8 to 1.0 ksi). The die radius also had to be held closely (5.2 times the stock
thickness). The first draw produced a cup 175 mm (6
in.) in diameter with a 235 mm (9
in.) diam flange.
The second draw was also made in the 2200 kN (250 tonf) double-action press. The punch for the second draw was
shaped to the required inner contour of the part, including the step at the base of the dome, which was formed as the press
bottomed at the end of the second draw stroke (operation 3, Fig. 19). This operation formed the dome shape of the bottle
top by reshaping (mostly by stretching) the cup formed in the first draw. The metal for the cylindrical area above the step
was drawn from the flange metal remaining after the first draw.
In the fourth operation, the hole in the top of the dome was pierced, and an internal stretch flange was formed around the
hole. This was done with a spring-loaded piercing die, which gave sufficient resistance to let the piercing punch shear the
material and then retreat under pressure from the flange-forming part of the punch. Both ends of the part were later
trimmed in a lathe.
Drawing Rectangular Parts. During the deep drawing of a box-shaped part, the metal in the corners of the part and
in the flange around the corner undergoes a change much like that which takes place when a round shell is drawn from a
circular blank. Metal is compressed at the corners, and significant thickening occurs where the metal flows into the
corners. The sides of the box undergo essentially no thickening, because there is no compression of the metal in the flange
areas as it flows or bends over the die radius.
Clearances in the sides between the punch and die are ordinarily about 10% greater than the metal thickness to
compensate for gage variations and to allow for metal flow. At the corners, punch-to-die clearances are similar to those
used for cylindrical parts to allow for thickening.
Blankholding devices are almost always used in producing deeply recessed box-shaped parts in order to control the metal
movement, particularly in the corners. The corners are under severe strain because of the intense compression of the
flange metal, and most fracturing, if it does occur, takes place in the lower wall corner sections.
Punch and die radii are generally the same for rectangular draws as for circular draws. Some fabricators prefer to make
the punch and die radii at the corners larger than along the sides in order to equalize the stress in the metal at the corners.
The top surface of the draw die and the draw radii should be polished smooth (free of grind marks and well blended) to
prevent localized retardation of metal flow with resultant uneven drawing of the metal. Burrs and bent edges on the blank
often restrict metal flow or movement along the blankholder surface to such a degree that vertical wall fractures can
occur.
Semideveloped blanks usually produce better results than rectangular ones. There are a number of patterns for trimming
the corners, ranging from a simple 45° trim to patterns with a carefully developed area containing the optimal volume and
area of metal.
The economic success of the run is related to tool wear and scrap rate. The following example describes a combination of
tool materials that has given satisfactory performance in terms of parts or draws per regrind and redress. The same tooling