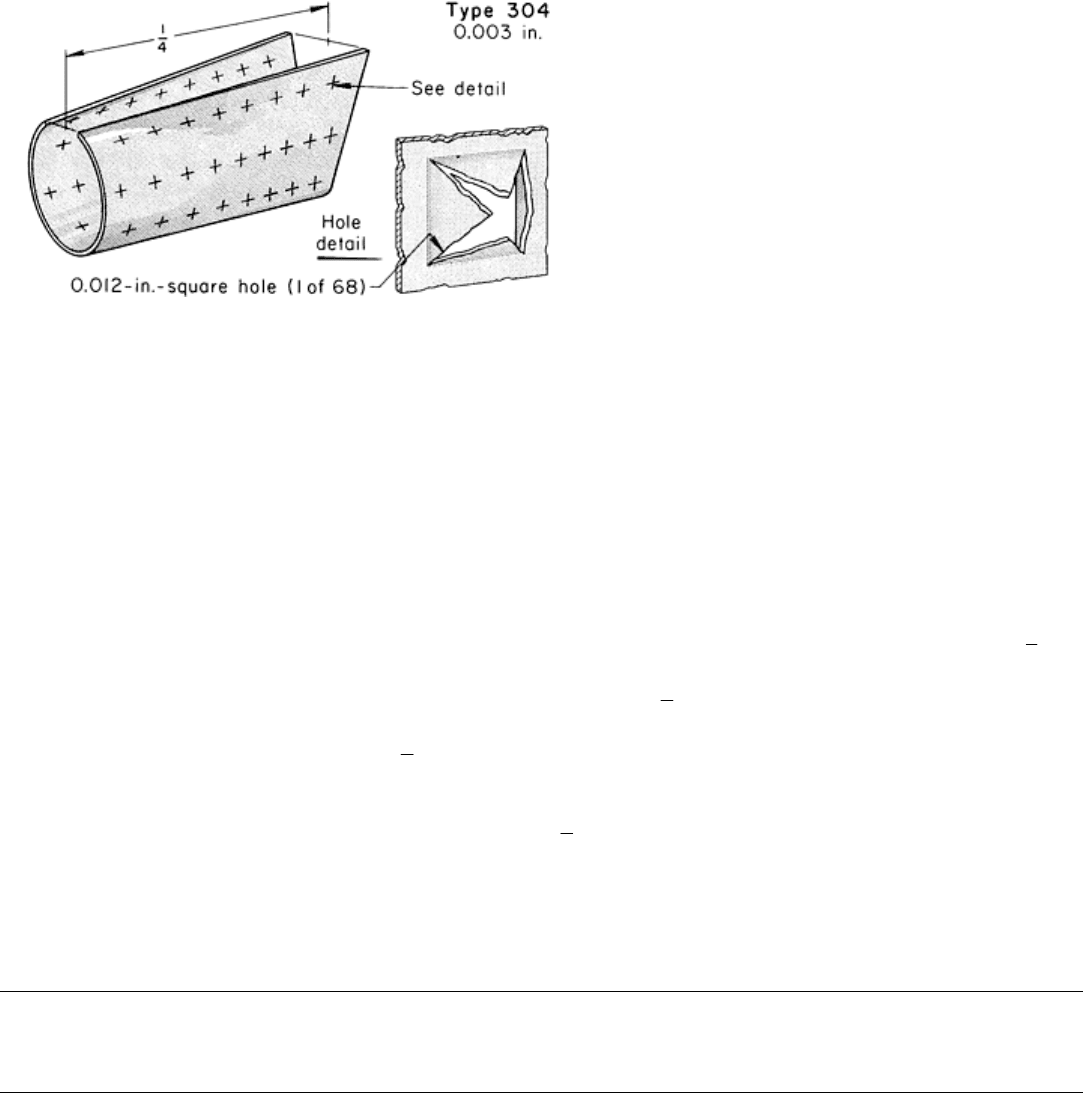
Clearance between punch and die should be about
the same as that for the blanking and piercing of cold-
rolled low-carbon steel. Some manufacturers use less
than 0.03 mm (0.001 in.) per side; others specify 5 to
10% of stock thickness per side for sheet and 10 to
15% of stock thickness for plates and bars. Studies
have shown, however, that larger clearances--12.5 to
13.5%, and even up to 42%, of stock thickness--have
resulted in increased die life (see the article "Piercing
of Low-Carbon Steel" in this Volume).
Cutting edges should be carefully aligned, sharp,
clean, and free of burrs. The importance of sharpness
of cutting edges cannot be overemphasized.
Deburring. Generally, stainless steel does not shear
clean, but leaves a rough work-hardened edge that is
dangerous to handle and may adversely affect
subsequent operations. Flat pieces can be rolled or pressed between dies adjusted exactly to the thickness of the stock, or
the burrs can be removed by grinding, stoning, or filing.
Lubrication. The blanking and piercing of stainless is often done dry, but the lubricants indicated in Table 2 are
sometimes used to prolong die life. Lubricants containing sulfur or chlorine are the most effective for this purpose.
Emulsions are used for high-speed work.
Dimensions. Pierced holes should not be smaller than the thickness of the stock. Holes larger than 3.18 mm (
in.)
should be spaced so that the distance between centers is not less than 1
times the hole diameter. Small holes should
have a distance between centers of at least 1
times the diameter of the holes. Holes should never be closer together than
one stock thickness, nor should the edge of blanks be less than one stock thickness from the edge of the stock. For
progressive-die operation, edge distances should be between 1
and 2 times stock thickness.
Nibbling. In some applications, an irregular contour is cut out by punching a series of overlapping holes along the
contour. This process is called nibbling. A variety of unusual shapes can be cut at 300 to 900 strokes per minute by a
press equipped with either a round or a rectangular punch.
Forming of Stainless Steel
Revised by Joseph A. Douthett, Armco Inc.
Press-Brake Forming
All of the austenitic stainless steels in the soft condition can be bent 180° over one stock thickness, but need up to 50%
more power to form than that required by low-carbon steel. Springback is more severe with austenitic stainless steels than
with low-carbon steel, and it must be allowed for. Work-hardened austenitic steel can be press-brake formed only to a
very limited degree. If austenitic stainless steel is heated to about 65 °C (150 °F), it can be formed with appreciably less
power than that required when it is cold and yet can be handled easily.
The straight-chromium grades of stainless steels vary in their response to press-brake forming. The low-carbon stainless
steels containing 12 to 17% Cr bend readily but, like the austenitic steels, need more power for bending than that required
for low-carbon steel. High-chromium low-carbon types, such as 446, bend better when heated to 175 to 205 °C (350 to
400 °F). The heating of these high-chromium low-carbon grades tends to lower the yield strength, but can simultaneously
Fig. 3
Cathode produced in a progressive die with carbide
tools. Dimensions given in inches.