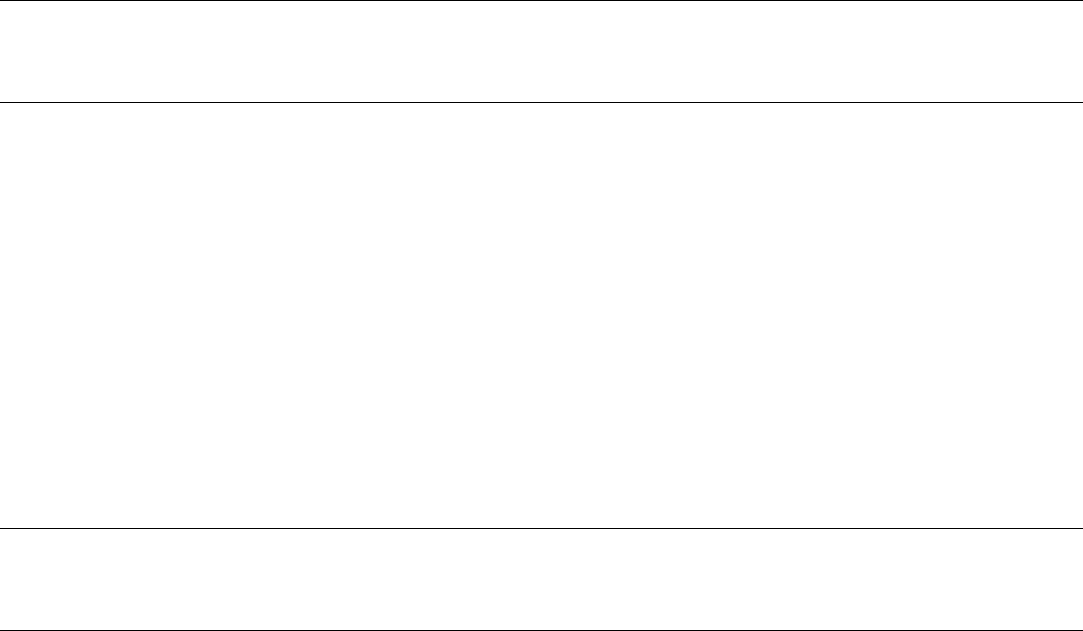
Abrasive Waterjet Cutting
J. Gerin Sylvia, Department of Industrial and Manufacturing Engineering, University of Rhode Island
Safety
Safety problems caused by such conditions as fire hazards and dust and noise pollution are minimized through the use of
abrasive waterjet cutting, as follows:
•
Safety is increased in an already hazardous atmosphere, particularly in comparison to flame and/or
plasma cutting torches. Because there is no heat buildup with abrasive waterjet cutting, fire hazards are
eliminated. There is no radiation emission or danger from flying slag particles
•
Airborne dust is virtually eliminated, making operation less hazardous to personnel working in close
proximity to the machine. Containment or other methods of airborne dust control are unnecessary
• Noise levels range from 85 to 95 dBA, which is consistent with OSHA regulations
Abrasive Waterjet Cutting
J. Gerin Sylvia, Department of Industrial and Manufacturing Engineering, University of Rhode Island
Selected References
• M. Hashish, Cutting With Abrasive Waterjets, Mech. Eng., Vol 106 (No. 3), March 1984, p 60-69
• D.L. Malm, Waterjets Add Impact to Abrasive Cleaning, Mod. Cast., Oct 1984, p 34-36
• J. Steinhauser, Abrasive Waterjets: The Cutting Edge of Technology, Cut. Tool Eng., Oct 1986, p 37-39
• J.G. Sylvia, Abrasive Waterjet--A New Technology, in
Proceedings of the 14th International Conference
on Flexible Manufacturing Systems, Oct 1985, Stockholm, p 157-166
• J.G. Sylvia and T.J. Kim, New High Pressure Jet Cutting and Cleaning, in
Proceedings of the 23rd Abrasive
Engineering Conference, May 1985, Bloomingdale, IL, p 83-90