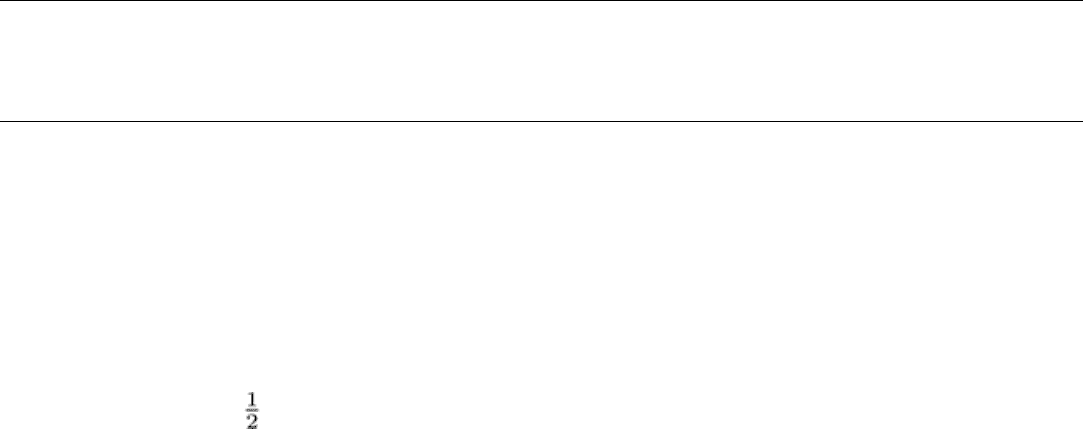
Laser Cutting
Gregg P. Simpson, Peerless Laser Processors Division, Peerless Saw Company; Thomas J. Culkin, Lumonics Materials Processing
Corporation
Laser-Cutting Applications
Virtually any metal can be laser cut. The conditions for cutting some metals, however, are difficult to obtain. Following is
a general description of how well each metal group can be cut.
All carbon and alloy steels can be laser cut to over 13 mm (0.50 in.) thick with an oxygen assist gas. As Fig. 9
shows, the feed rates are dependent on available power at the workpiece. A general rule of thumb is that for a given
thickness, the feed rate increases about 50% when power is doubled. The resulting kerfs can be as small as 0.1 mm (0.004
in.) thick with a 65 mm (2 in.) focal length lens. The resulting HAZ is small (about 0.1 to 0.3 mm, or 0.004 to 0.012
in.), depending on thickness and speed. The edges are clean, smooth, and square.
Higher-carbon steel exhibits an improved edge quality, although the HAZ is slightly larger and harder. Impurities of
phosphorus and sulfur can cause some edge burning: Lower-quality steels exhibit this edge burning, whereas alloy steels
generally do not. In fact, the alloy steels, such as chrome-nickel-moly (for example, 4340), and chrome-moly (for
example, 4130), are perfect candidates for extremely high quality edges that are very smooth and clean. These steels do,
however, require about 50% more time to pulse a starting hole than is the case with a similar thickness of plain carbon
steel. Another consideration is that the HAZ is slightly larger and harder (about 45 to 60 HRC) depending on the alloy
and carbon content. This means that further processing can be difficult on the laser-cut edges unless they are annealed.
Laser-cut tool steels have almost the same results. The exceptions are the alloys that have very dense alloying elements,
such as tungsten. These alloys retain a large amount of heat when molten, which helps to limit thickness and produce very
rough cuts having heavy slag deposits. The air- and oil-hardened alloys exhibit very good edge quality and can be cut up
to 10.2 mm (0.400 in.) thick at about 0.8 m/min (32 in./min) at 1300 W. Alloys such as D-2 and M-2 can only be cut up to
about 4 mm (0.160 in.) thick with the same power.
Stainless steel alloys are also readily cut using a laser. The feed rates are reduced, however, because these alloys do
not react as effectively with oxygen as carbon steel alloys do. An inert assist gas may be used to obtain a weld-ready
edge, free of all oxides, at the expense of about one-half the oxygen-assisted speed. Stainless steels maintain their
corrosion resistance because the HAZ is small.
In general, the ferritic (400 series) stainless steels produce smoother cuts with less slag than austenitic (300 series)
stainless steels do. These stainless alloys do not contain nickel and can be cut to about 6.5 mm (0.260 in.) thick.
The added presence of nickel does affect the energy coupling and heat transfer in the alloy. This means that these alloys
are not effectively laser cut above 5 mm (0.197 in.) thick. The viscosity of the molten nickel is very high and has a
tendency to migrate and adhere to the bottom of the cut. This increases the heat in the metal and produces a large HAZ, as
well as a rough cut starting approximately one-third to one-half the way through the material. This effect can be reduced
by using high-pressure assist gas jets or rapid-cooling methods (such as water) in the cut.
Nonferrous Alloys. Aluminum alloys can readily be laser cut, but only to about 4 mm (0.160 in.) thick. The thickness
is limited because aluminum has high reflectivity at infrared wavelengths and high thermal conductivity. To overcome
these effects, the laser must have a TEM
00
mode, which allows for tighter focusing and higher power outputs, that is, 500
W or more. To further improve the cutting, short focal length lenses and high assist gas pressures help reduce and/or
eliminate slag that forms when molten material is blown to the back side of the cut and solidifies; the slag is very easily
removed. Feed rates are generally 25% slower than when laser cutting stainless steels.
Copper, brass, and bronze are even more reflective and heat conductive than is aluminum. Because brass and bronze are
alloys of copper, they can be laser cut, but with limited thickness and speed. The cuts can be rough, and a slag is present
on the bottom of the cut. Copper has been cut under ideal conditions in thicknesses up to 6.35 mm (0.25 in.) with 1200 W.
The speeds are extremely slow, so practical upper cutting is limited to about 2.6 mm (0.100 in.).