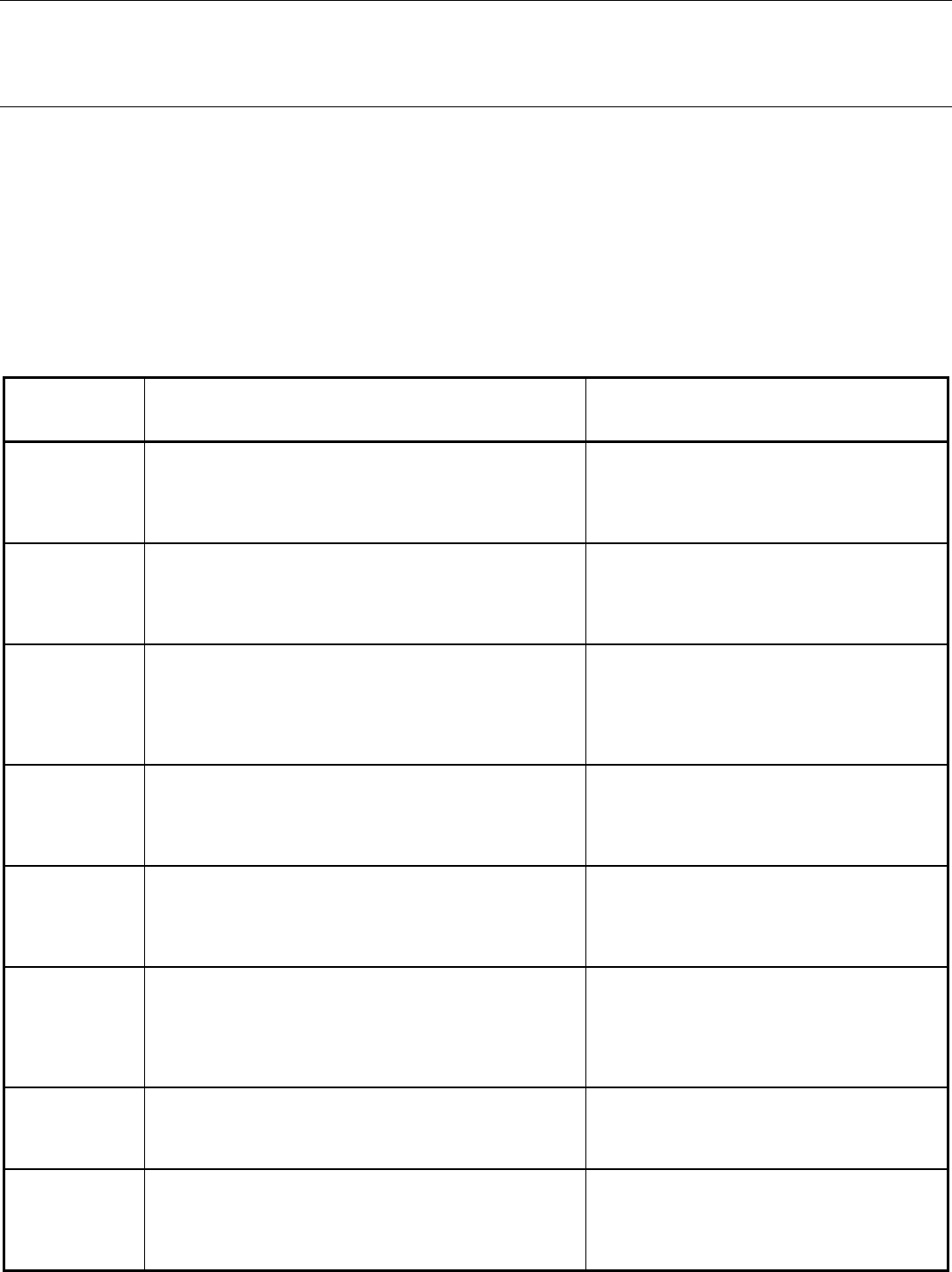
Laser Cutting
Gregg P. Simpson, Peerless Laser Processors Division, Peerless Saw Company; Thomas J. Culkin, Lumonics Materials Processing
Corporation
Competing Cutting Methods
The advantages and disadvantages of several conventional metal-shaping processes that compete with the laser are shown
in Table 1. While the laser does not displace any of these processes in terms of their special capabilities, laser cutting does
fill a very important void. For example, the laser is the ideal method for producing short-run or prototype blanked parts of
large, complex or small, intricate shapes (see Fig. 7). The choice to laser cut these parts is based on cost. The expense of
temporary tooling or edge finishing far exceeds the cost of laser cutting.
Table 1 Advantages and disadvantages of laser cutting versus traditional metal cutting methods
Cutting method Advantages
Disadvantages
Laser Good edge quality, good accuracy, small kerf, narrow HAZ,
no distortion, little noise; cuts nonmetals, cuts small and
complex shapes
High equipment cost, limited to under 13 mm
(0.5 in.) thick, slower feed rates over 6.4 mm
(0.25 in.); cuts single layer
Plasma arc Lower equipment costs, faster feed rates over 6.4 mm (0.25
in.); cuts over 13 mm (0.5 in.) thick
Lower accuracy, decreased edge quality, larger
kerf, wider HAZ, noisy, higher operating costs;
only cuts metal
Laser Good edge quality, good accuracy, lower scrap rate, no
distortion, small kerf, no tooling or tool wear, increased part
nesting; cuts complex shapes, cuts up to 13 mm (0.5 in.) thick,
cuts tempered materials and nonmetals
Higher equipment costs, lower process rate,
higher costs on larger part quantities
Nibbling (turret
punch press)
Good process rate, lower equipment costs, economical on
medium to high production runs
Lower edge quality, high tool wear, high tooling
costs, low accuracy, distortion, scrap; only cuts
10 mm (0.38 in.) thick
Laser Good edge quality, no tooling or dies, short setup times, rapid
and low-cost design changes, noncontact cutting; cuts complex
shapes and three-dimensional shapes, cuts tempered materials
Higher equipment costs, low rate on high
volumes
Punch press High volume rates; lower costs at high volumes; cuts over 13
mm (0.5 in.) thick
Greater tool fabrication time, higher tool costs
and maintenance, more setup time, poorer tool
design, part stresses, lower edge quality; only
cuts annealed steel
Laser High feed rate, economical on small and medium quantities;
cuts nonmetals and nonconductive metals
Lower edge quality, higher equipment costs,
thickness limitations
Wire electric
discharge
machining
Good edge quality, good accuracy, lower equipment costs,
cuts over 13 mm (0.5 in.) thick, cuts very fine and complex
shapes
Very slow on any thickness, fixturing