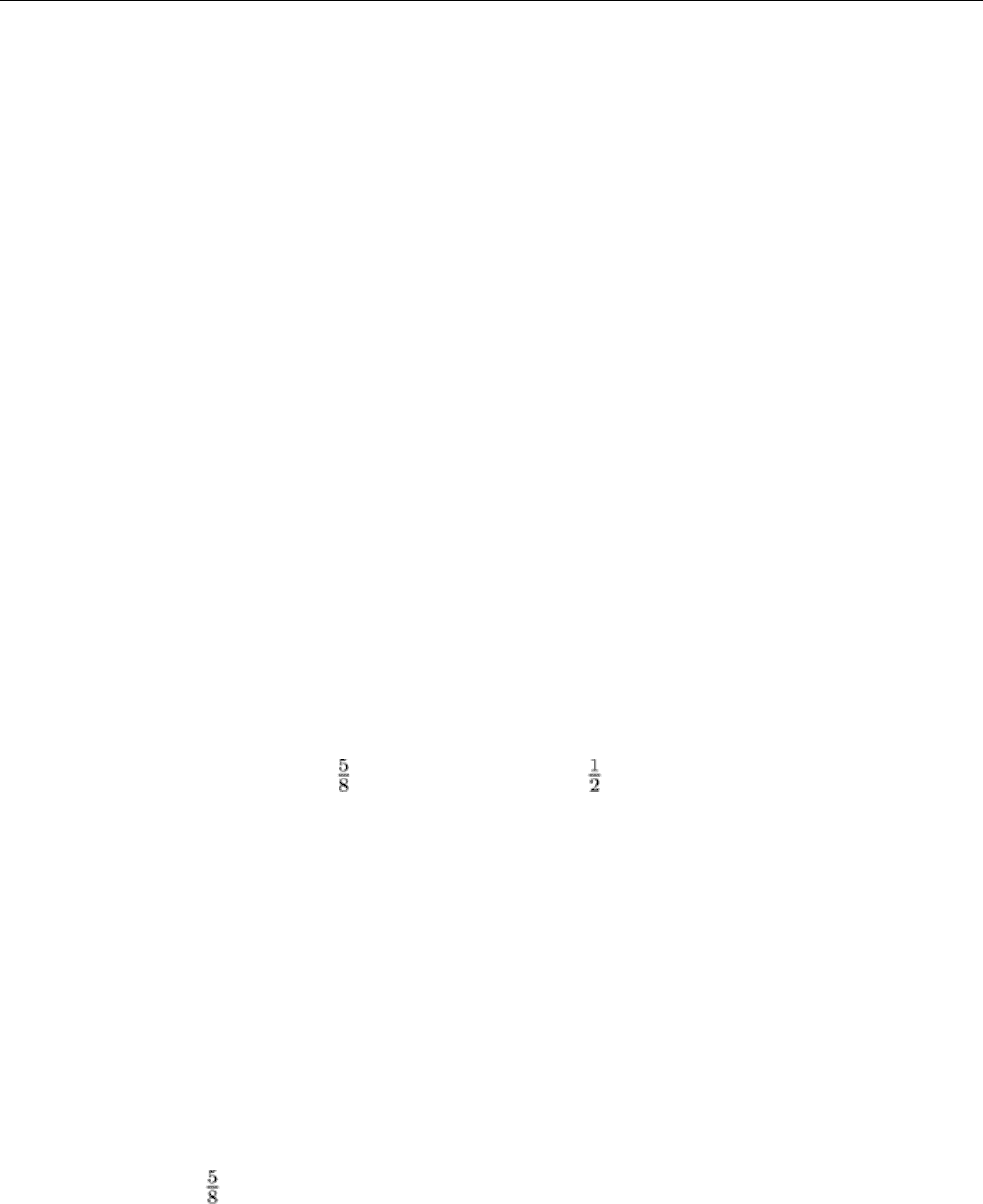
Tube Spinning
Revised by Jack D. Stewart, Sr., Stewart Enterprises, Inc.
Introduction
TUBE SPINNING is a rotary-point method of extruding metal much like cone spinning, except that the sine law (see the
article "Spinning" in this Volume) does not apply. Because the half angle of a cylinder is zero, tube spinning follows a
purely volumetric rule, depending on the practical limits of deformation that the metal can stand without intermediate
annealing. Tube spinning is also limited by the smallest percentage reduction in thickness that will ensure complete flow
of the metal. This minimum reduction is usually 15 to 25%, depending on the metal and on the thickness of the original
tube.
Applicability. Spinning is one method of reducing the wall thickness of tubular shapes and increasing their strength,
particularly for aircraft and aerospace applications. Producing specific shapes from tubing is a major function of tube
spinning. For example, one or more flanges can be spun at selected areas on a tube, often at a savings in labor and
material costs when compared with other processes such as machining. Tube spinning has also been used because ring
forgings having the desired relationship between wall thickness and length were not available.
All ductile work metals are suitable for tube spinning; the practical ranges of compositions and strengths are
approximately the same as for the power spinning of cones. Metals as hard as 35 HRC have been successfully spun. Most
tube spinning is accomplished without heating the workpiece.
The amount of wall reduction that can be accomplished without intermediate annealing is given for a number of metals in
Table 2 in the article "Spinning" in this Volume. The amount of permissible reduction is often greater for the spinning of
tubes than for the spinning of cones or hemispheres, particularly in the case of backward spinning.
The range of tube sizes that can be spun depends primarily on the available equipment. Tubelike preforms that have an
inside diameter in a range from 4.75 mm to 3 m (0.187 to 120 in.) have been successfully spun. Wall thicknesses of the
starting tubes are often as great as 25.4 mm (1.0 in.) for steel and 31.8 mm (1.25 in.) for aluminum and under ideal
circumstances have exceeded 41.3 mm (1 in.) for steel and 63.5 mm (2 in.) for aluminum.
The minimum size of tube that can be spun is more likely to be a limiting factor than the maximum size, because of
machine characteristics. For example, a large machine is not well suited to spinning small tubing, because it has
insufficient spindle speed. The relationship between spindle speed and tube size should be such that a minimum of 120
m/min (400 sfm) can be obtained. Very small (<9.5 mm, or 0.38 in., diam) tubes are usually spun on machines that hold
the tube stationary while the tool rings rotate around it.
Preform Requirements. Preform is the name commonly applied to a tube or a tubular shape before it is spun. A
preform may be a straight, symmetrical tube, or it may have been changed in shape by the addition of an internal flange
for clamping. Tubular shapes used for spinning include forged or centrifugally cast tubes (both of which are completely
machined before spinning), welded tubing, seamless tubing, and extruded tubing.
For spinning, the inside diameter should vary no more than ±0.051 mm (±0.002 in.) on tubes up to 76 mm (3 in.) in inside
diameter or no more than ±0.152 mm (±0.006 in.) on tubes with inside diameters of 75 to 510 mm (3 to 20 in.).
Tolerances of +0.5, -0 mm (+0.020, -0 in.) are typical for tubes 635 mm to 1.27 m (25 to 50 in.) in diameter; tolerances of
+0.75, -0 mm (+0.030, -0 in.) are used for larger sizes. The roundness and wall thickness of the preform will also affect
tolerance. A 41.3-mm (1 -in.) wall thickness, 3-m (120-in.) preform will usually have at least 1.7 mm (0.067 in.), and
frequently 4.75 mm (0.187 in.), of positive tolerance to permit loading.
The wall thickness of the preform should be within ±0.075 mm (±0.003 in.) unless the preform is machined all over in
which case wall thickness should be within ±0.025 mm (±0.001 in.). Ovality should be within 0.05 mm (0.002 in.) for
small-diameter preforms within 0.30 mm (0.012 in.) for large diameters.