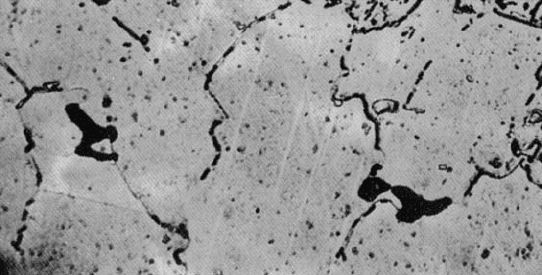
to the creep of metallic materials. Polymeric materials also show creep. In ductile met-
als and alloys subjected to creep, fracture is accompanied by necking, void nucleation
and coalescence, or grain boundary sliding.
A material is considered failed by creep even if it has not actually fractured. When
a material does actually creep and then ultimately break the fracture is defined as stress
rupture. Normally, ductile stress-rupture fractures include necking and the presence of
many cracks that did not have an opportunity to produce final fracture. Furthermore,
grains near the fracture surface tend to be elongated. Ductile stress-rupture failures
generally occur at high creep rates and relatively low exposure temperatures and have
short rupture times. Brittle stress-rupture failures usually show little necking and occur
more often at smaller creep rates and high temperatures. Equiaxed grains are observed
near the fracture surface. Brittle failure typically occurs by formation of voids at the
intersection of three grain boundaries and precipitation of additional voids along grain
boundaries by di¤usion processes (Figure 7-21).
Stress-Corrosion Stress-corrosion is a phenomenon in which materials react with cor-
rosive chemicals in the environment. This leads to formation of cracks and lowering
of strength. Stress-corrosion can occur at stresses well below the yield strength of the
metallic, ceramic, or glassy material due to attack by a corrosive medium. In metallic
materials, deep, fine corrosion cracks are produced, even though the metal as a whole
shows little uniform attack. The stresses can be either externally applied or stored re-
sidual stresses. Stress-corrosion failures are often identified by microstructural exami-
nation of the nearby metal. Ordinarily, extensive branching of the cracks along grain
boundaries is observed (Figure 7-22). The location at which cracks initiated may be
identified by the presence of a corrosion product.
Inorganic silicate glasses are especially prone to failure by reaction with water
vapor. It is well known that the strength of silica fibers or silica glass products is very
high when these materials are protected from water vapor. As the fibers or silica glass
components get exposed to water vapor, corrosion reactions begin leading to formation
of surface flaws, which ultimately cause the cracks to grow when stress is applied.
Polymeric coatings are applied to optical fibers to prevent them from reacting with
water vapor. For bulk glasses, special heat treatments such as tempering are used.
Tempering produces an overall compressive stress on the surface of glass. Thus, even if
the glass surface reacts with water vapor the cracks do not grow since the overall stress
at the surface is compressive. If we create a flaw that will penetrate the compressive
Figure 7-21 Creep cavities formed at grain boundaries in an austentic stainless steel (500).
(From ASM Handbook, Vol. 7, (1972) ASM International, Materials Park, OH 44073.)
C HA P T E R 7 Fracture Mechanics, Fatigue, and Creep Behavior216